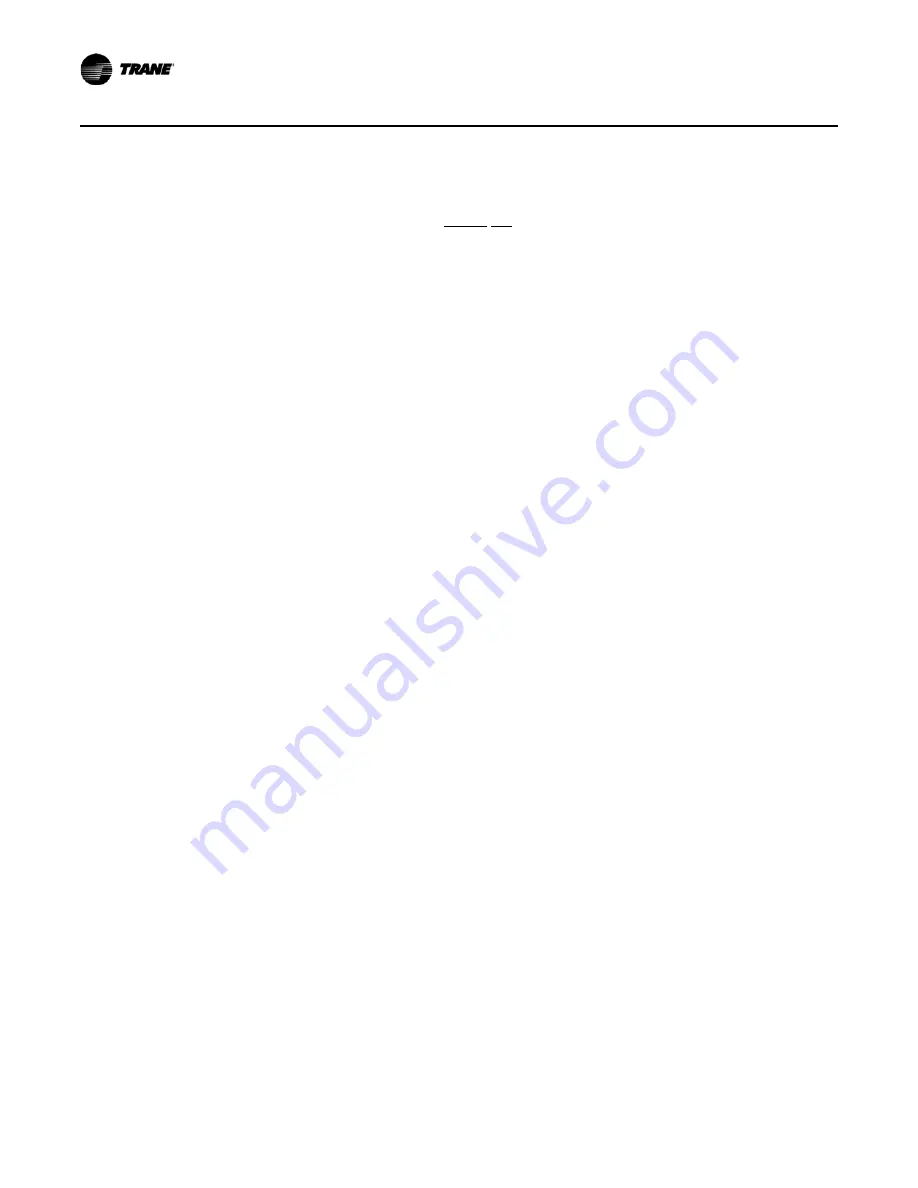
40
CNT-SVX08F-EN
PID Control
is 0.5°F (0.3°C). This setting ensures that the sensor reading has changed an adequate amount
before the controller responds.
Important:
The error deadband should not be smaller than the sensor resolution or the
controller will react to noise.
Adjusting Error Deadband for Staged Outputs
This section describes how to adjust the error deadband for staging applications. Finding the best
error deadband for staged output applications is more difficult than for modulating outputs.
Instead of using a continuous actuator (such as a chilled water valve), staged systems use binary
outputs to start and stop pieces of equipment, such as fans in a cooling tower. Each piece of
equipment contributes a set amount to the final output. When setting the error deadband for staged
outputs, the main goal is to reduce equipment cycling.
provides good initial values, but the error deadband should be adjusted at the site
with the equipment running.
Follow these guidelines when adjusting the error deadband:
•
Determine how tight deadband control should be. A smaller error deadband results in tighter
control, but control should not be so tight that the stages cycle on and off too frequently.
For example, for a VAV air-handler turning on cooling stages, control can be somewhat loose.
The individual VAV boxes control their valve to the space depending on the supply air
temperature. If the supply air temperature is relatively warm, the VAV box allows more air flow.
If the supply air temperature is somewhat cool, the VAV box constricts the air flow.
•
The contribution of each stage can change depending on external circumstances, so make
adjustments under worst case conditions. Adjust the error deadband for cooling tower fan
stages on very warm days, and adjust the error deadband for boiler stages on very cold days.
With the preceding guidelines in mind, use the following procedure to determine and adjust error
deadband staged outputs:
37. Run the system manually. If possible, do so under worst case conditions for the site. Although
it is not always possible for a technician to do this, it is possible for a well-trained customer.
38. Find the smallest change in temperature, DT, that the first stage can contribute (the quantity
could also be building static pressure for fans or flow for pumps).
Pay attention to possible changes in external circumstances, such as the amount of water flow.
If the system uses a lead-lag approach to the equipment, it will be necessary to find the
minimum DT for all stages.
39. Multiply DT by 0.45 (the error deadband should be slightly less than half of DT). Note the
resolution of the sensor. It may be necessary to round the error deadband to a more reasonable
value.
40. Run the system with the new error deadband. Cycling should be reduced as much as possible.