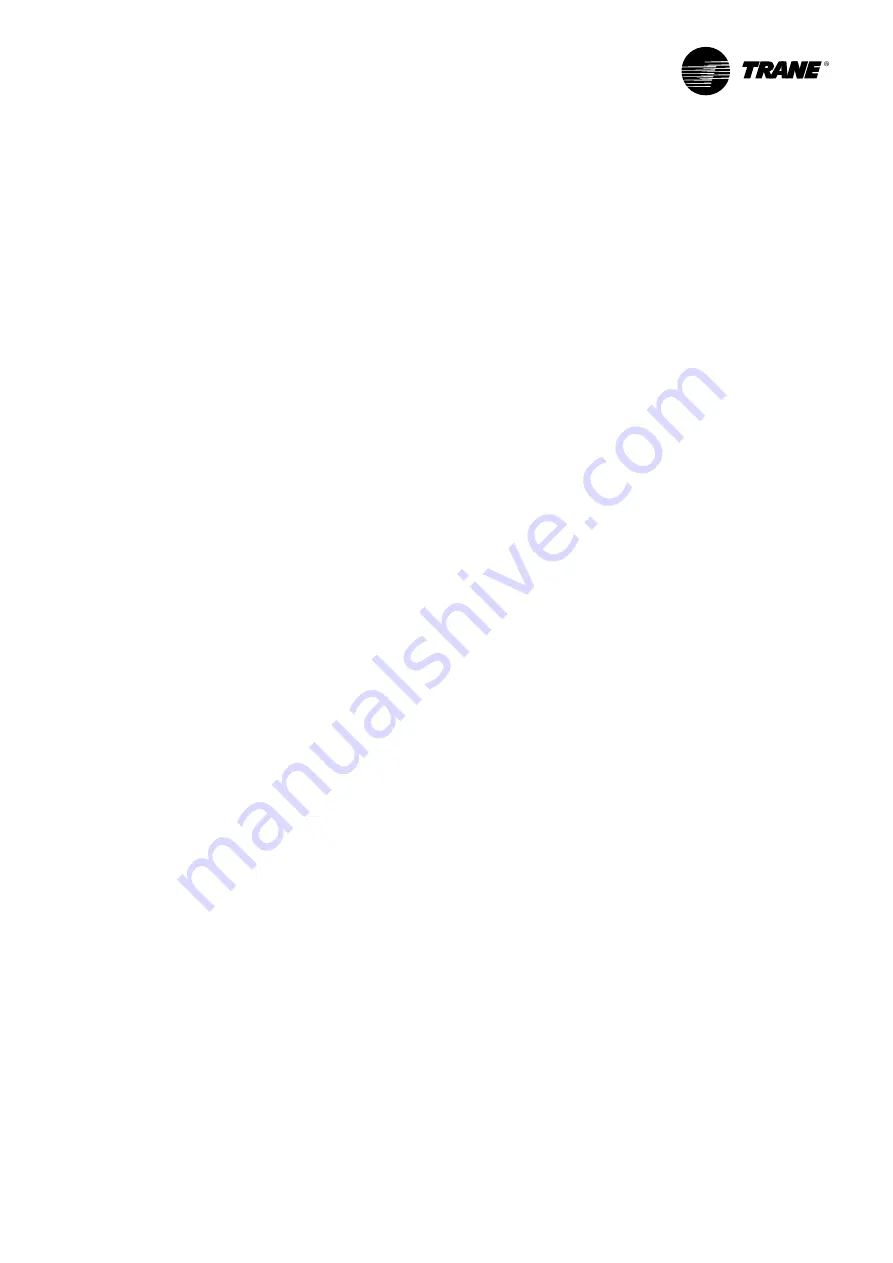
RLC-SVX19G-GB
153
11
UNT-PRC002-GB
Sound power levels
Discharge
Measurement conditions:
Measurements taken in a room adjacent to the room containing the FWD, at the outlet of the rectangular duct (1.5 m
long) fixed to its discharge opening.
Fan
Power level in dB(A), per Hz frequency band
Overall power
Unit
speed
125
250
500
1000
2000
4000
8000
dB(A)
1
55
50
42
37
37
31
30
46
FWD 08
2
57
54
47
40
30
38
40
50
3
58
57
50
42
32
40
43
53
1
57
51
45
42
34
33
28
48
FWD 10
2
58
54
48
45
38
39
35
51
3
60
58
50
48
40
42
39
54
1
57
51
45
42
34
33
28
48
FWD 12
2
58
54
48
45
38
39
35
51
3
60
58
50
48
40
42
39
54
1
56
62
50
48
39
38
36
56
FWD 14
2
61
66
55
53
47
46
45
60
3
63
69
58
56
50
50
49
63
1
57
63
51
49
40
39
37
57
FWD 20
2
61
66
55
53
47
46
45
60
3
63
69
58
56
50
50
49
63
Intake
Measurement conditions:
Measurements taken at the horizontal air intake.
Fan
Power level in dB(A), per Hz frequency band
Overall power
Unit
speed
125
250
500
1000
2000
4000
8000
dB(A)
1
56
55
55
53
46
45
42
57
FWD 08
2
63
62
60
60
53
53
53
64
3
66
65
63
62
56
55
57
67
1
62
58
55
58
51
48
44
61
FWD 10
2
66
63
60
62
56
55
52
66
3
70
67
63
65
59
59
57
69
1
62
58
55
58
51
48
44
61
FWD 12
2
66
63
60
62
56
55
52
66
3
70
67
63
65
59
59
57
69
1
66
65
65
65
57
50
46
68
FWD 14
2
73
72
69
71
64
59
57
74
3
78
76
73
75
69
64
63
78
1
68
72
64
64
56
52
50
69
FWD 20
2
76
76
68
71
65
61
61
75
3
78
79
71
74
69
66
66
78
Installer-Supplied Components
Customer wiring interface connections are shown in
the electrical schematics and connection diagrams that
are shipped with the unit. The installer must provide the
following components if not ordered with the unit:
• Power supply wiring (in conduit) for all field-wired
connections
• All control (interconnecting) wiring (in conduit) for field
supplied devices
• Fused-disconnect switches
Power Supply Wiring
All power supply wiring must be sized and selected
accordingly by the project engineer in accordance
with standard IEC 60364. All wiring must comply with
local codes. The installing (or electrical) contractor
must provide and install the system interconnecting
wiring, as well as-the power supply wiring. It must be
properly sized and equipped with the appropriate fuse-
disconnect switches. The type and installation location(s)
of the fused-disconnect switches must comply with all
applicable codes.
Cut holes into the sides of the control panel for the
appropriately-sized power wiring conduits. The wiring
is passed through these conduits and connected to the
terminal blocks.
To provide proper phasing of 3 phase input, make
connections as shown in field wiring diagrams and as
stated on the yellow WARNING label in the starter panel.
Proper equipment grounds must be provided to each
ground connection in the panel
CAUTION!
Customer wiring interface connections are
shown in the electrical schematics and connection
diagrams that are shipped with the unit. The installer
must provide the following components if not ordered
with the unit.
WARNING!
To prevent injury or death, disconnect all
electrical power sources before completing wiring
connections to the unit.
CAUTION!
The use of copper mono-conductors is the
preferred solution to avoid corrosion and overheating
at terminal connections.
Control Power Supply
Chiller is provided with control power transformer, it is
not necessary to provide additional control power voltage
to the unit.
Heater Power Supply
The evaporator shell is insulated from ambient air and
protected from freezing for temperature down to -20°C
by two thermostatically-controlled immersion heaters
combined with evaporator pumps activation through
Tracer UC800. Whenever the ambient temperature
drops below 0°C the thermostat energizes the heaters
and the Tracer UC800 activates the pumps. If ambient
temperatures below -20°C are expected, contact your
Trane local office.
CAUTION!
The control panel main processor does
not check for loss of power to the heat tape nor does
it verify thermostat operation. A qualified technician
must frequently verify power to the heat tape and
confirm operation of the heat tape thermostat, to avoid
catastrophic damage to the evaporator.
CAUTION!
With factory-fitted disconnect switch, trace
heating is taken from the live side of the isolator so
power remains on. Supply voltage to the heating tapes
is 400V.
In case of winter water drainage for freeze protection, it
is compulsory to disconnect the evaporator heaters to
protect them from burning due to overheat.
Water Pump Power Supply
Provide power-supply wiring with fused disconnect
switch(es) for the chilled water pump(s).
Interconnecting Wiring
Chilled-Water Flow (Pump) Interlock
RTAF requires a field-supplied, control-voltage contact
input through a flow proving switch (6S51) and an
auxiliary contact (6K51). Connect the proving switch and
auxiliary contact to terminal 2 connector J2 cards (1A14).
Refer to the field wiring diagram for details.
Chilled-Water Pump Control
An evaporator water-pump output relay closes when
the chiller is given a signal to go into the AUTO mode
of operation from any source. The contact is opened to
turn off the pump in the event of most machine-level
diagnostics, to prevent the buildup of pump heat.
CAUTION!
The evaporator water pump output relay
must be used to control the chilled water pump and to
benefit from the water pump timer function at startup
and shutdown of the chiller. This is required when
the chiller is in operation under freezing conditions,
especially if the chilled water loop does not contain
glycol.
CAUTION!
Refer to Freeze Protection section for
information about the evaporator circulating pump.