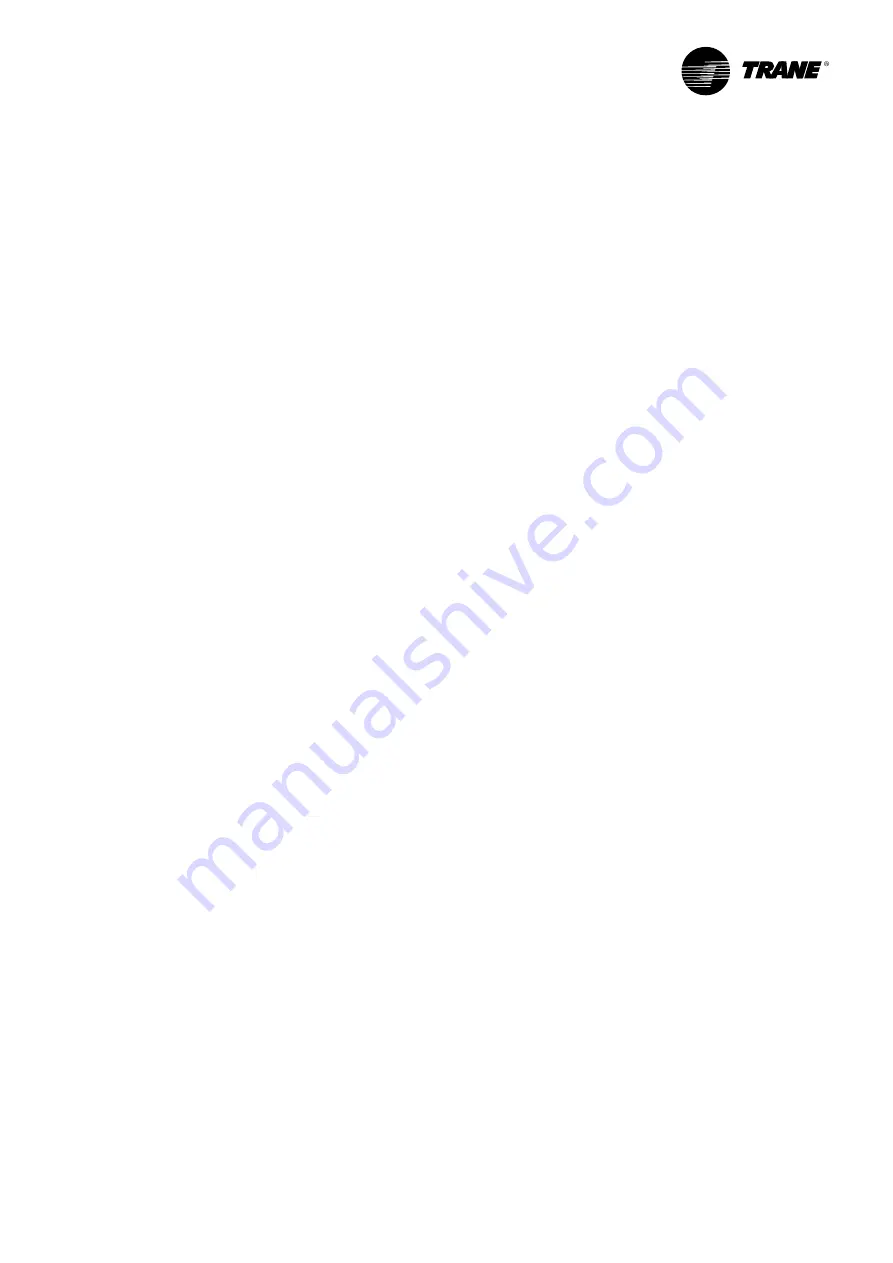
RLC-SVX19G-GB
103
11
UNT-PRC002-GB
Sound power levels
Discharge
Measurement conditions:
Measurements taken in a room adjacent to the room containing the FWD, at the outlet of the rectangular duct (1.5 m
long) fixed to its discharge opening.
Fan
Power level in dB(A), per Hz frequency band
Overall power
Unit
speed
125
250
500
1000
2000
4000
8000
dB(A)
1
55
50
42
37
37
31
30
46
FWD 08
2
57
54
47
40
30
38
40
50
3
58
57
50
42
32
40
43
53
1
57
51
45
42
34
33
28
48
FWD 10
2
58
54
48
45
38
39
35
51
3
60
58
50
48
40
42
39
54
1
57
51
45
42
34
33
28
48
FWD 12
2
58
54
48
45
38
39
35
51
3
60
58
50
48
40
42
39
54
1
56
62
50
48
39
38
36
56
FWD 14
2
61
66
55
53
47
46
45
60
3
63
69
58
56
50
50
49
63
1
57
63
51
49
40
39
37
57
FWD 20
2
61
66
55
53
47
46
45
60
3
63
69
58
56
50
50
49
63
Intake
Measurement conditions:
Measurements taken at the horizontal air intake.
Fan
Power level in dB(A), per Hz frequency band
Overall power
Unit
speed
125
250
500
1000
2000
4000
8000
dB(A)
1
56
55
55
53
46
45
42
57
FWD 08
2
63
62
60
60
53
53
53
64
3
66
65
63
62
56
55
57
67
1
62
58
55
58
51
48
44
61
FWD 10
2
66
63
60
62
56
55
52
66
3
70
67
63
65
59
59
57
69
1
62
58
55
58
51
48
44
61
FWD 12
2
66
63
60
62
56
55
52
66
3
70
67
63
65
59
59
57
69
1
66
65
65
65
57
50
46
68
FWD 14
2
73
72
69
71
64
59
57
74
3
78
76
73
75
69
64
63
78
1
68
72
64
64
56
52
50
69
FWD 20
2
76
76
68
71
65
61
61
75
3
78
79
71
74
69
66
66
78
Drainage
Notice: Waterbox Damage!
Failure to follow these instructions could result in
damage to the waterbox. Do not use Teflon® pipe tape
or overtighten when installing valves, drains, plugs, and
vents on cast iron waterboxes.
RTAF chillers are equipped with two drain connections,
one located on each waterbox. Waterboxes also include
vent connections to assist in bleeding air from the
chilled water loop. These vent connections should not
be assumed to be capable of venting all chilled water
piping.
In order to completely remove water from the evaporator
tubes and waterboxes, vent and drain connections on
both waterboxes should be opened. Use pressurized
air to ensure all water is removed from the evaporator.
In addition, two-pass supply waterboxes should have
drainage capability through supply water piping.
Incomplete drainage increases the risk of damage due
to expansion associated with trapped water freezing.
Note: If evaporator will be drained for winter storage, the
heaters must be disconnected to prevent overheating.
It is also mandatory to fulfill the drainage for winter
season for unit arriving from factory.
Sufficient glycol quantity and concentration must be
introduced in the lower part of the evaporator head to
prevent damage from stagnating water freezing.
Pressure Gauges
Install field-supplied pressure components as shown in
Figure 6. Locate pressure gauges or taps in a straight
run of pipe; avoid placing them near elbow (at least at
10 pipe diameter from discontinuity).
To read manifold pressure gauges, open one valve and
close the other (depending on the side of the desired
reading), this eliminate errors resulting from differently
calibrated gauges installed at unmatched elevations.
Pressure Relief Valves
Install a water pressure relief valve in the evaporator
inlet piping between evaporator and the inlet shutoff
valve. Water vessels with close-coupled shutoff valves
have high potential for hydrostatic pressure buildup on
a water temperature increase. Refer to applicable local
codes for relief valve installation.
Evaporator Flow Switch
Specific connection and schematic wiring diagram
are shipped within the unit. Some piping and control
schemes, particularly those using a single water pump
for both chilled and hot water, must be analyzed to
determine how and/or if a flow sensing device will
provide the desired operation.
Flow Switch Installation – Typical Requirements
1. Mount the switch upright, with a minimum of
10 pipes diameters of straight horizontal run on
each side. Do not install close to elbows, orifices,
or valves. The arrow on the switch must point in the
direction of the flow. For additional information,
consult the flow switch information sheet coming
with the part.
2. To prevent switch fluttering, remove all air from the
water system. Tracer UC800 provides a 6 second
time delay after a “loss-of-flow” diagnostic before
shutting the unit down. Contact a Trane service
representative if nuisance machine shutdowns
persist.
3. Adjust the switch to open when water flow falls
below nominal values. Evaporator data is given
on the General Information Section. Flow Switch
contacts are closed on proof of water flow.
4. Install a pipe strainer in the entering evaporator-
water line to protect components.
CAUTION!
Control voltage from the chiller to the flow
proving device is 110V AC.
Notice: Evaporator Damage!
If the microprocessor calls for a pump to start and
water does not flow, the evaporator may be damaged
catastrophically. It is the responsibility of the installing
contractor and/or the customer to ensure that a pump
will always be running when called upon by the chiller
controls.