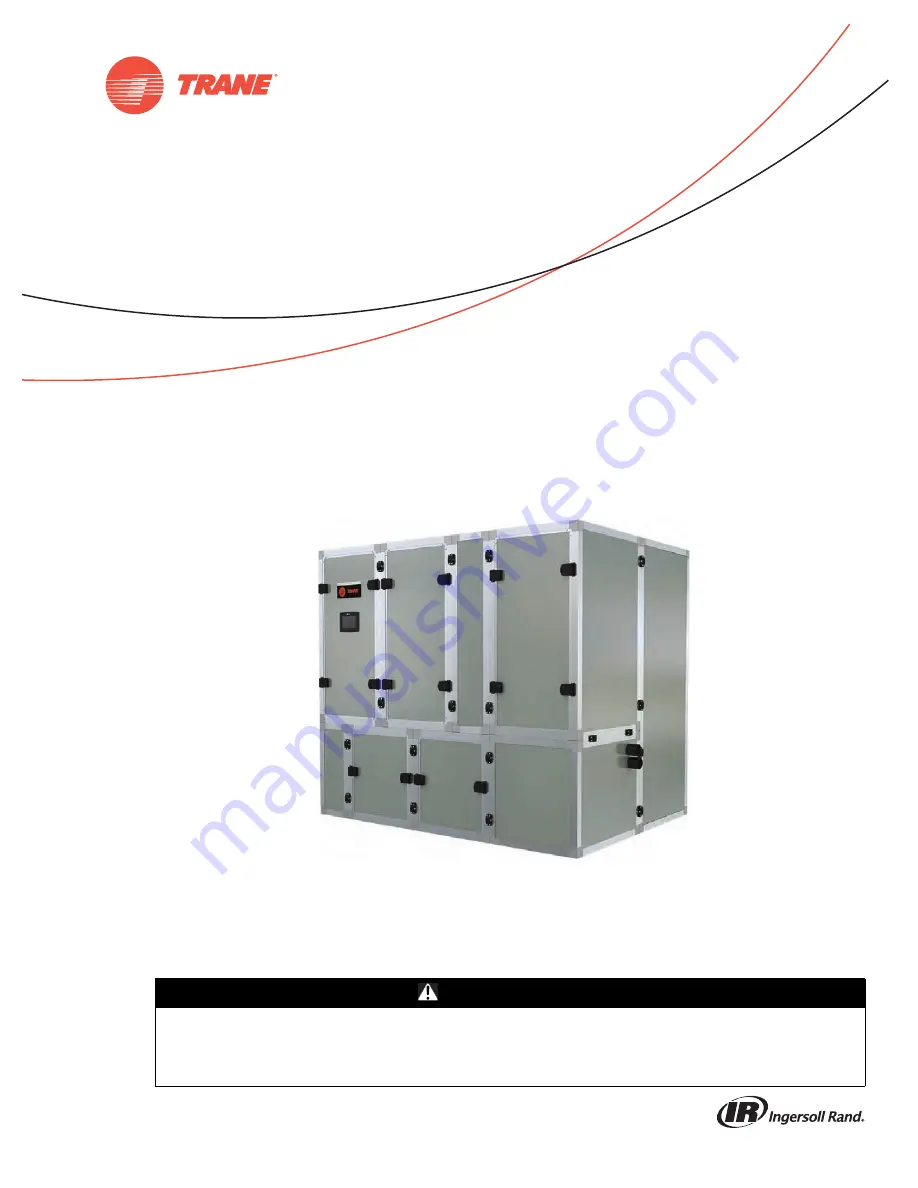
SAFETY WARNING
Only qualified personnel should install and service the equipment. The installation, starting up, and servicing
of heating, ventilating, and air-conditioning equipment can be hazardous and requires specific knowledge and
training. Improperly installed, adjusted or altered equipment by an unqualified person could result in death or
serious injury. When working on the equipment, observe all precautions in the literature and on the tags,
stickers, and labels that are attached to the equipment.
Modular Self-Contained
40 to 80 Tons
Installation, Operation,
and Maintenance
SCWM
40 to 80 Tons
PKG-SVX027A-EN
October 2019