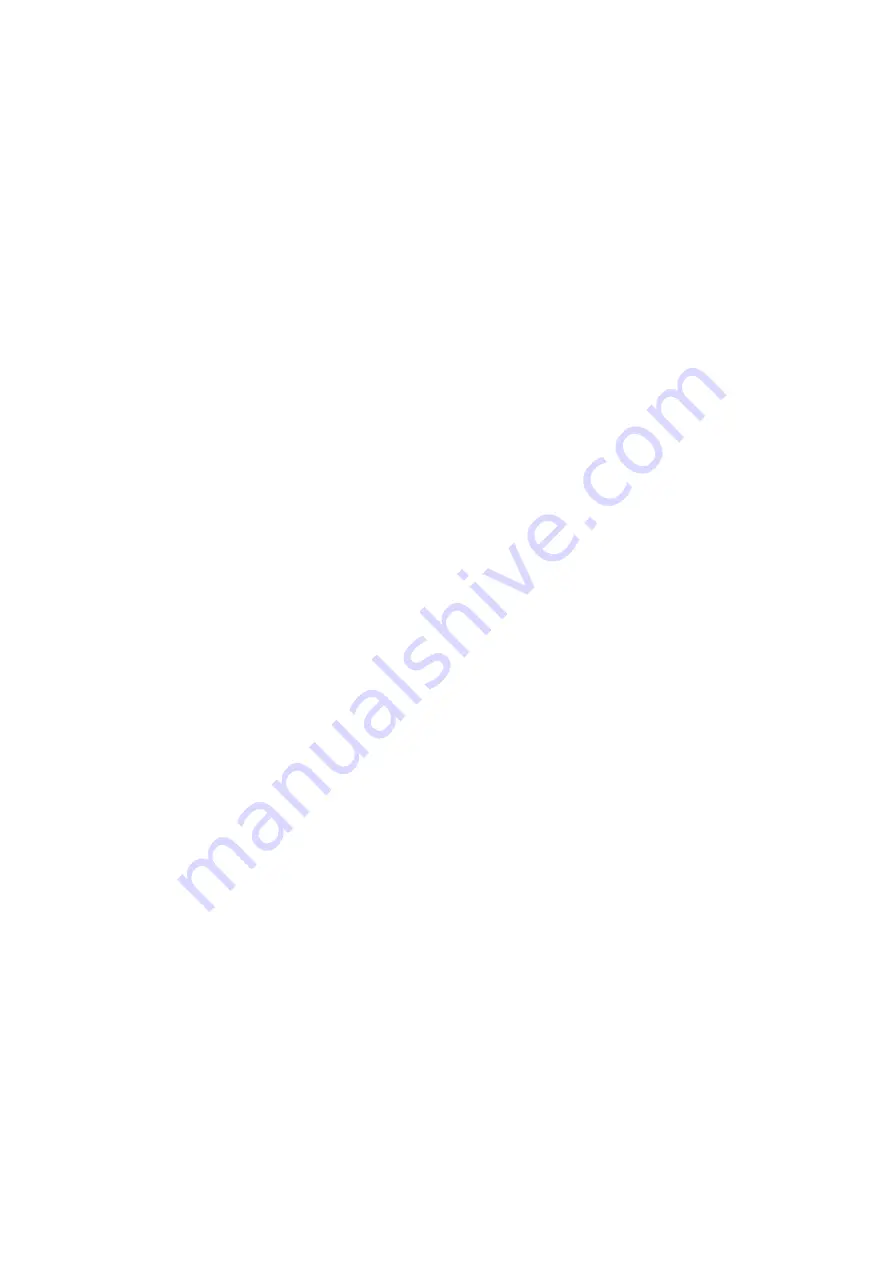
52
the compressor may shut down on a “Low Oil Flow” diagnostic.
Fin-tube Coil Cleaning
Clean the fin-tube coils at least once a year or more frequently if the unit is in a “dirty” environment. A
clean coil will help to maintain unit operating efficiency. Follow the detergent manufacturer's instructions to
avoid damaging the coils.
To clean the coils use a soft brush and a sprayer such as a garden pump type or a high-pressure type. A
high quality detergent such as Trane Coil Cleaner (Part No. CHM-00255) is recommended. See RTAC-
SVG01B-EN for maintenance and cleaning procedures.
Note:
If detergent mixture is strongly alkaline (pH value greater than 8.5, an inhibitor must be added).
WARNING - Hazardous Chemicals!
Coil cleaning agents can be either acidic or highly alkaline and can burn severely if contact with
skin occurs. Handle chemical carefully and avoid contact with skin. ALWAYS wear Personal
Protective Equipment (PPE) including goggles or face shield, chemical resistant gloves, boots,
apron or suit as required. For personal safety refer to the cleaning agent manufacturer’s Materials
Safety Data Sheet and follow all recommended safe handling practices. Failure to follow all safety
instructions could result in death or serious injury or equipment damage.
Water side heat exchanger maintenance
CAUTION! Proper Water Treatment!
The use of untreated or improperly treated water in a RTXC may result in scaling,
erosion,corrosion, algae or slime. It is recommended that the services of a qualified water
treatment specialist be engaged to determine what water treatment, if any, is required. The Trane
Company assumes no responsibility for equipment failures which result from untreated or
improperly treated water, saline or brackish water.
Since the water side heat exchanger is typically part of a closed circuit, it does not accumulate appreciable
amounts of scale or sludge. However, if cleaning is deemed necessary, use the cleaning methods
recommended as following.
•
Use a nondestructive tube test to inspect the evaporator tubes at 3-year intervals.
Note
: It may be desirable to perform tube tests on these components at more frequent intervals,
depending upon unit application. This is especially true of critical process equipment.
•
Tube fouling is suspect when the approach temperature is higher than predicted. Standard water
applications will operate with less than a 5.6°
C
(10
°
F) approach. If the approach exceeds 5.6°
C
(10°
F
)
cleaning the tubes is recommended.
If the annual tube inspection indicates that the tubes are fouled, two cleaning methods can be used to rid
the tubes of contaminants. The methods are:
Mechanical Cleaning Procedure
Mechanical tube cleaning method is used to remove sludge and loose material from smooth-bore tubes.
Review mechanical space limitations and determine the safest method or methods of rigging and lifting the
waterboxes.
1. Disconnect water pipes, if connected. Mind the temperature sensor and insulation.
2. Select the proper lift connection device from
Table 8 Main components weights
. The rated lifting capacity