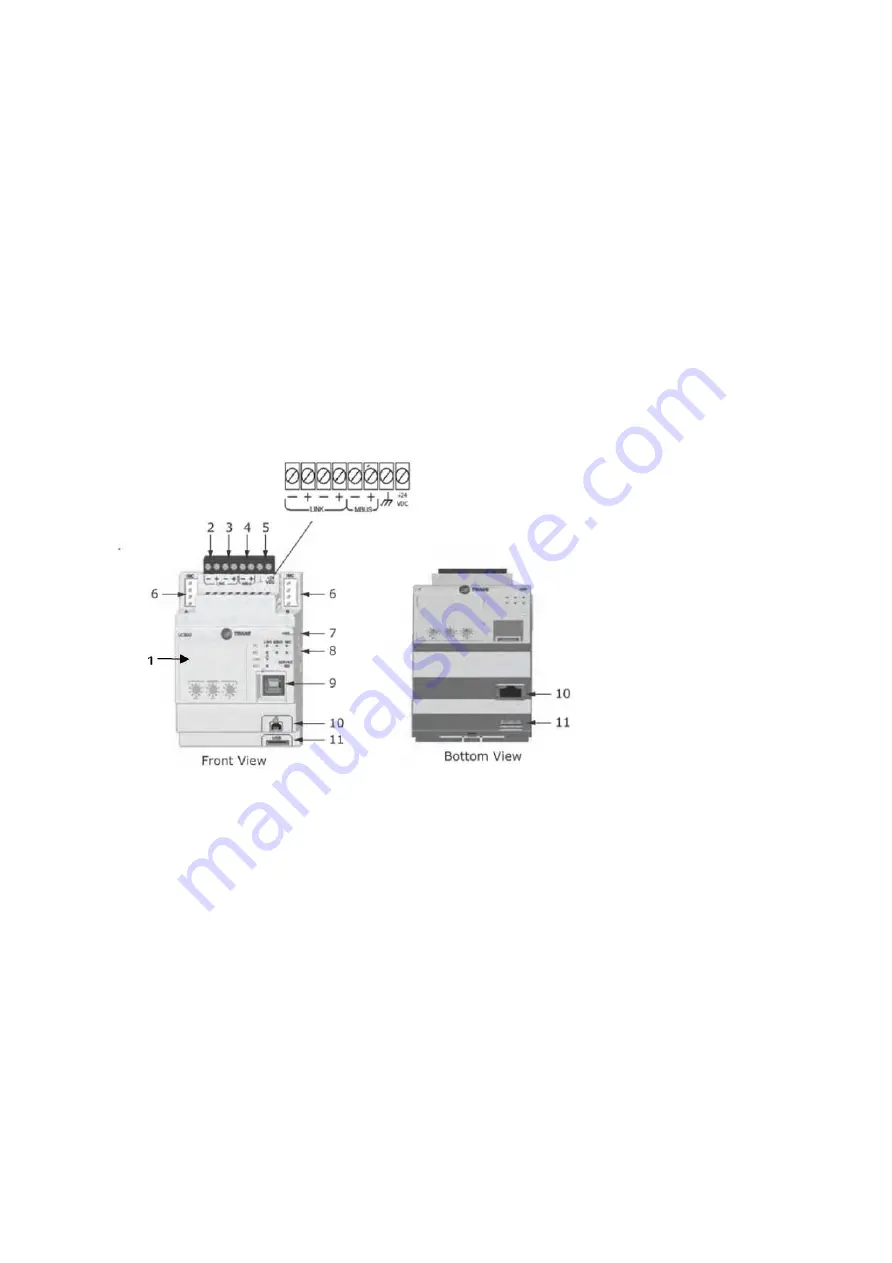
34
Controls
Overview
RTXC
units utilize the following control/ interface components:
•
Tracer® UC800 Controller
•
Tracer® AdaptiView™ TD7 Operator Interface (Refer to RTXC Tracer® AdaptiView™ Operations Guide
for details)
UC800 Specifications
Power Supply
The UC800 receive 24 VDC (210 mA) power from the power supply located in the unit control
panel.
Wiring and Port Descriptions
Below
illustrates the UC800 controller ports, LEDs, rotary switches, and wiring terminals. The
numbered list following the figure corresponds to the numbered callouts in the illustration.
Figure 14 UC800 Wiring locations and connection ports
1) Rotary Switches for setting BACnet® MAC address or MODBUS ID.
2) LINK for BACnet MS/TP, or MODBUS Slave (two terminals, ±). Field wired if used.
3) LINK for BACnet MS/TP, or MODBUS Slave (two terminals, ±). Field wired if used.
4) Machine bus for existing machine LLIDs (IPC3 Tracer® bus 19.200 baud). IPC3 Bus: used for Comm4 using
TCI or LonTalk® using LCI-C.
5) Power (210 mA at 24 Vdc) and ground terminations (same bus as item 4). Factory wired.
6) IMC for MODBUS Master (two terminals, ±). Field wired if used.
7) Marquee LED power and UC800 Status indicator.
8) Status LEDs for the BAS link, MBus link, and IMC link.
9) USB device type B connection for the service tool (Tracer® TU).
10) The Ethernet connection can only be used with the Tracer® AdaptiView™ display.
11) USB Host (not used).
Communication Interfaces
There are four connections on the UC800 (Refer to the
) that support the communication interfaces
listed.
•
BACnet® MS/TP