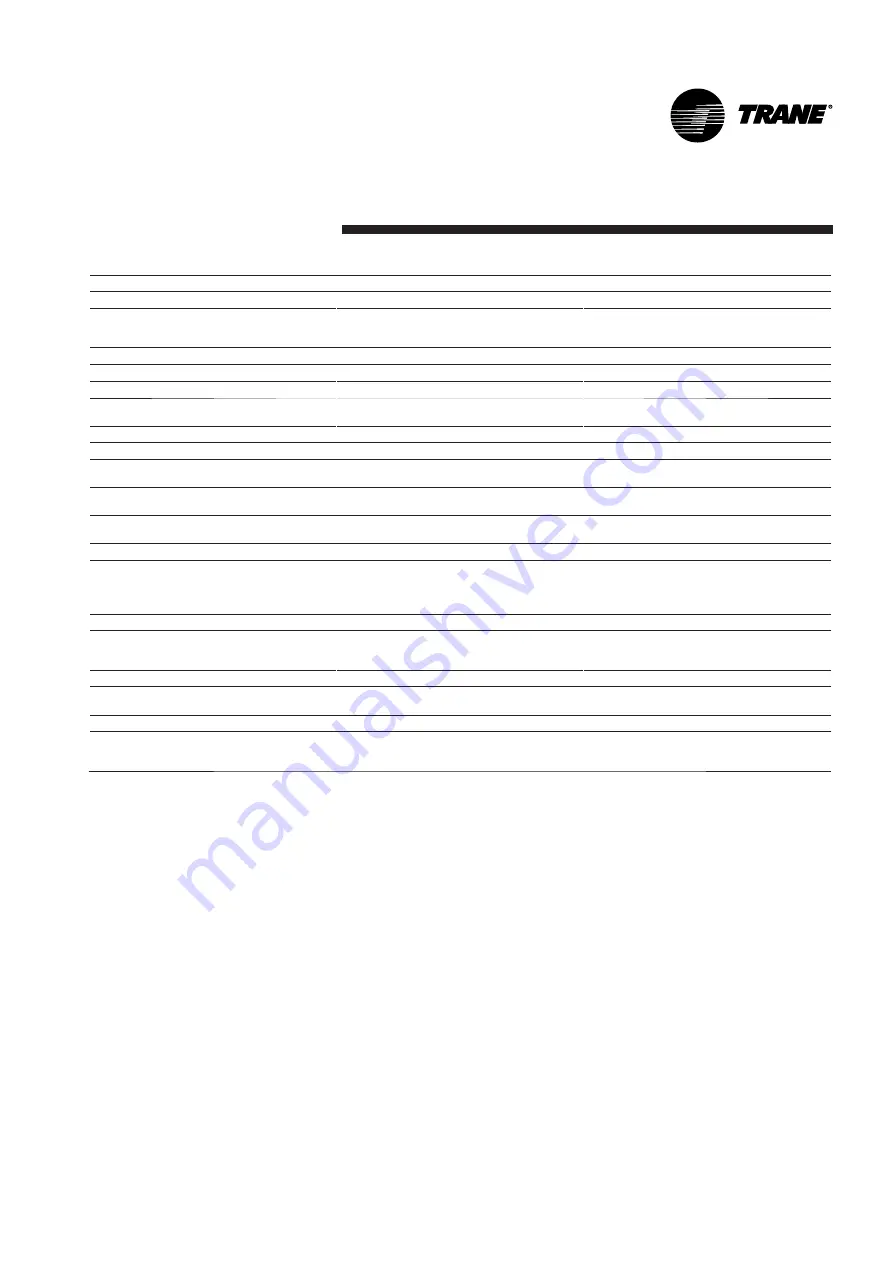
43
CG-SVX06F-GB
Maintenance
F) Compressor noisy
Compressor knocks.
Components broken in compressor.
Change compressor.
Suction duct abnormally cold.
a) Uneven liquid flow.
b) Expansion valve locked in open position.
a) Check superheat setting and fixing of expansion valve
bulb.
b) Repair or replace.
G) Insufficient cooling capacity
Thermostatic expansion valve “whistles”.
Not enough refrigerant.
Check refrigerant circuit tightness and add refrigerant.
Excess pressure drops through filter drier
Drier filter clogged.
Replace.
Excessive superheat.
Superheat not properly adjusted.
Check adjustment of superheat and adjust thermostatic
expansion valve.
Insufficient water flow.
Chilled water pipes obstructed.
Clean pipes and strainer.
H) Discharge pressure too high
Condenser abnormally hot.
Presence of uncondensable liquids in system, or excess
refrigerant.
Purge uncondensable fluids and drain off excess
refrigerant.
Chilled water leaving temperature too high.
Overload on cooling system.
Reduce load on system.
Reduce water flow if necessary.
Condenser air output too hot.
Reduced air flow. Air intake temperature higher than
specified for unit
Clean or replace air filters. Clean coil. Check operation
of fan motors.
I) Suction pressure too high
Compressor operates continuously.
Suction duct abnormally cold.
Refrigerant flows back to compressor.
Excess cooling demand on evaporator
a) Expansion valve too far open.
b) Expansion valve locked in open position.
Check system.
a) Check for superheat and check that expansion valve
bulb is secure.
b) Replace.
J) Suction pressure too low
Excessive pressure drop through filter drier.
Refrigerant does not flow through thermostatic
expansion valve.
Filter drier clogged.
Expansion valve bulb has lost its refrigerant.
Replace the filter drier.
Replace the bulb.
Loss of power.
Expansion valve obstructed.
Replace.
Superheat too low.
Excessive pressure drops through evaporator.
Check adjustment of superheat and adjust thermostatic
expansion valve.
K) Insufficient cooling capacity
Low pressure drops through evaporator
Low water flow rate.
Check water flow rate. Check state of strainer, check
for obstruction in chilled water pipes.
Check pressure switch contact in water.