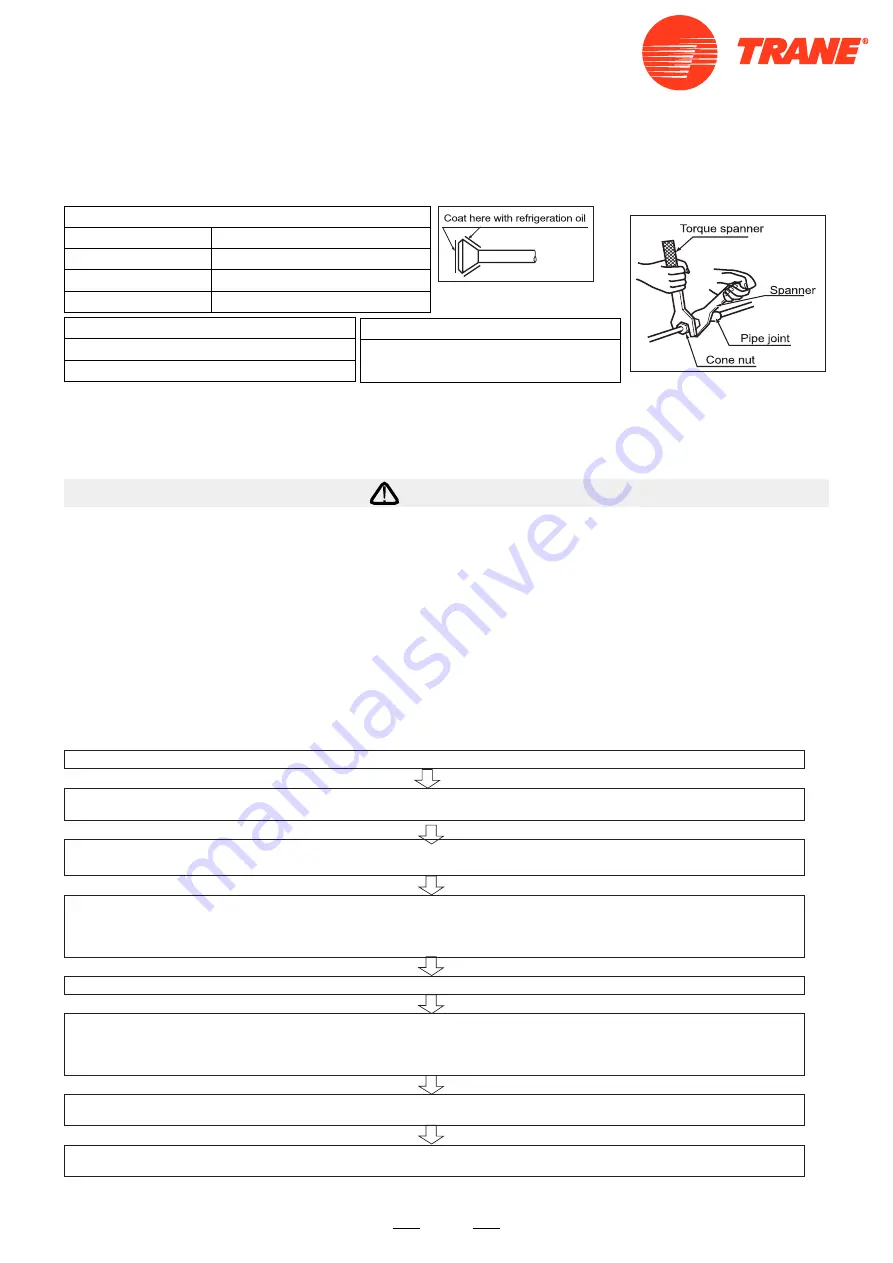
91
3. Refrigerant piping work
1). Align the centers of both flares and tighten the flare nuts 3 or 4 turns by hand. Then tighten them fully with the tor
wrenches. Use torque wrenches when tightening the flare nuts to prevent damage to the flare nuts and escaping
gas.
Flare nut fightening torque
Flare nut for Ø6.35 14.2-17.2N.m (144-175kgf.cm)
Flare nut for Ø9.52 32.7-39.9N.m (333-407kgf.cm)
Flare nut for Ø12.7 49.5-60.3N.m (505-615kgf.cm)
Flare nut for Ø15.88 61.8-75.4N.m (630-769kgf.cm)
Valve cap tightening torque
Liquid pipe 26.5-32.3N.m(270-330kgf.cm)
Gas pipe 48.1-59.7N.m(490-610kgf.cm)
2) To prevent gas leakage, apply refrigeration oil on both inner and outer surfaces of the flare. (Use refrigeration oil
for R410A)
4. Purging air and checking gas leakage
When piping work is completed, it is necessary to purge the air and check for gas leakage.
Service port cap tightening torque
10.8-14.7N.m(110-150kgf.cm)
WARNING
1) Do not mix any substance other than the specified refrigerant (R410A) into the refrigeration cycle.
2) When refrigerant gas leaks occur, ventilate the room as soon and as much as possible.
3) R410A, as well as other refrigerants, should always be recovered and never be released directly into the
environment.
4) Use a vacuum pump for R410A exclusively. Using the same vacuum pump for different refrigerents may damage
the vacuun pump or the unit.
• If using additional refrigerant, perform air purging from the refrigerant pipes and indoor unit using a vacuum pump,
then charge additional refrigerant.
• Use a hexagonal wrench (4mm) to operate the stop valve rod.
• All refrigerant pipe joints should be tightened with a torque wrench at the specified tightening torque.
Connect projection side of charging hose(Which comes from gauge manifold) to gas stop valve's service port.
Remove covers from liquid stop valve and gas stop valve.
Fully open gauge manifold's low-pressure valve(Lo) and completely close its high-pressure valve(Hi).
(High-pressure valve subsequently requires no operation.)
Apply vacuum pumping. Check that the compound pressure gauge reads-0.1MPa(-76cmHg).
Evacuation for at lease 1 hour is recommended.
Disconnect charging hose from gas stop valve's service port, then fully open liquid and gas stop valves.
(Do not attempt to turn valve rodj beyond its stop.)
Tighten valve caps and service port caps for the liquid and gas stop valves with a torque wrench at the
specified torques. See "3 Refrigerant piping " on page 6 for details.
Close gauge manifold's low-pressure valve(Lo) and stop vacuum pump.
(Leave as is for 4-5 minutes and make sure the coupling meter needie does not go back.
If it does go back, this may indicate the presence of moisture or leaking from connecting parts. After inspecting
all the connection and loosening then retightening thenuts, reqeat steps 2-4. )
Turn the liquid stop valve's rod 90 degrees counterclockwise with a hexagonal wrench to open valve.
Close it after 5 seconds, and check for gas leakage.
Using soapy water, check for gas leakage from indoor unit's flare and outdoor unit's flare and valve rods.
After the check is complete, wipe all soapy water off.
Содержание 4TXM2318BF300AA
Страница 102: ...100 PCB 0151800611 4MXE2309BF0W0AA 4MXE2312BF0W0AA...
Страница 116: ...114 PCB 0151800364D Power Module 0011800377C...
Страница 117: ...115 Power Module 0011800377AJ PCB 0151800364C...
Страница 153: ...151 Screw 0010600325 Terminal block 0010452210E Connection cable 0150400330 Install the connection cable like this way...