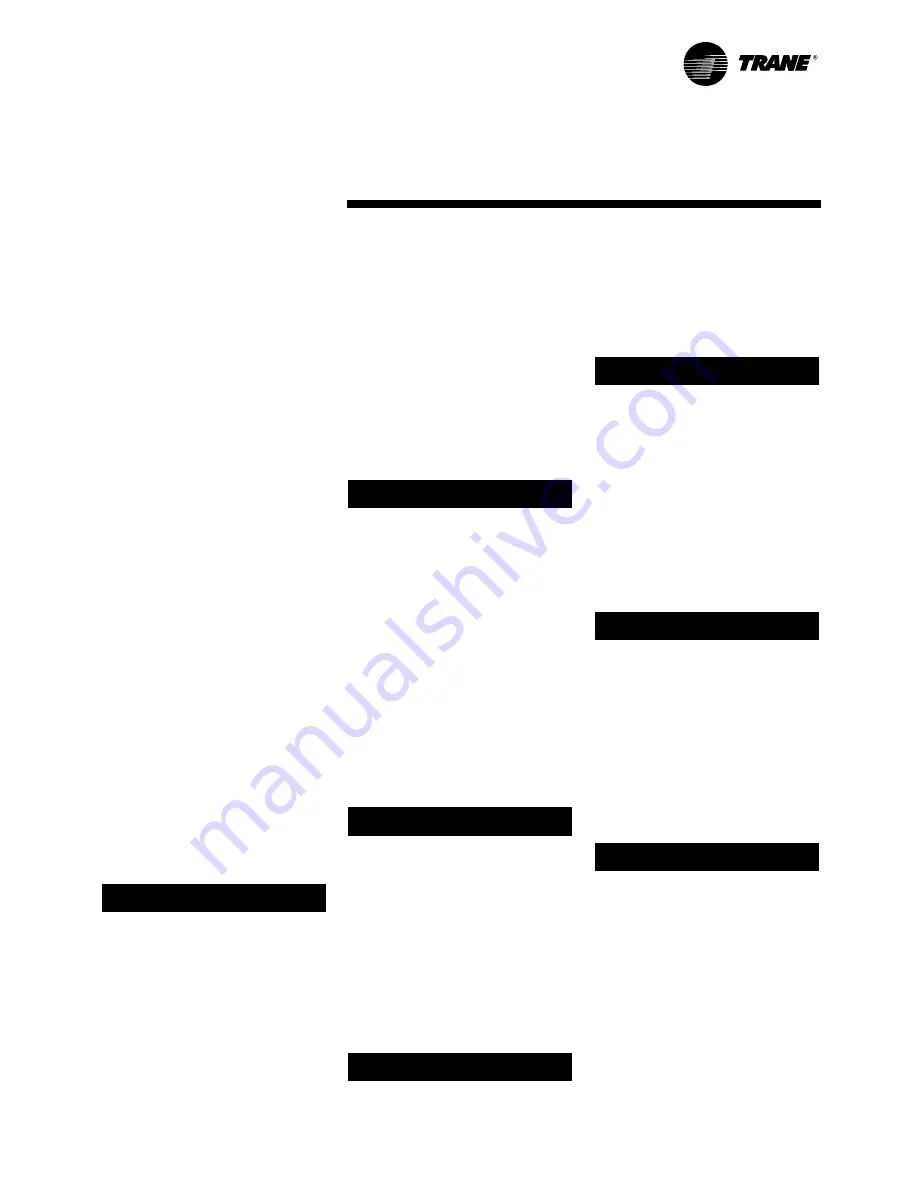
23
operating load. Overheating may
vary slightly on the circuit if the
system load is lower, when the slide
valve is moving.
Overheating must stabilize at
approximately 4°C when the above
components have stabilized.
Subcooling
Normal subcooling for each circuit
ranges from 8-10°C, depending on
the units. If subcooling for either
circuit does not fall within these
values, check the overheating for the
circuit and adjust if necessary. If
overheating is normal but
subcooling is not, contact a qualified
service technician.
Seasonal Unit Start-up
1. Close all valves and reinstall the
drain plugs in the evaporator.
2. Service the auxiliary equipment
according to the startup and
maintenance instructions provided
by the respective equipment
manufacturers.
3. Close the vents in the evaporator
chilled-water circuits.
4. Open all the valves in the
evaporator chilled-water circuits.
5. Open all refrigerant valves to
verify they are in the open
condition.
6. If the evaporator was previously
drained, vent and fill the
evaporator and chilled-water
circuit. When all air is removed
from the system (including each
pass), install the vent plugs in the
evaporator water boxes.
C
CA
AU
UT
TIIO
ON
N
Ensure that the compressor and oil-
separator heaters have been
operating for a minimum of 24 hours
before starting. Failure to do so may
result in equipment damage.
7. Check the adjustment and
operation of each safety and
operating control.
8. Close all disconnect switches.
9. Refer to the sequence for daily
unit startup for the remainder of
the seasonal startup.
Shutdown procedures
Temporary Shutdown and Restart
To shut the unit down for a short
time, use the following procedure:
1. Press the Stop key on the UCM-
CLD. The compressors will
continue to operate and, after
unloading for 20 seconds, will stop
when the compressor contactor
de-energizes.
2) Stop the water circulation by
disconnecting the power supply to
the chilled water and cooling
water pumps.
C
CA
AU
UT
TIIO
ON
N
Under freezing conditions, the chilled
water pump must remain in
operation during the full shutdown
period of the chiller if the chilled
water loop does not contain glycol,
to prevent any risk of evaporator
freeze-up.
Extended period shutdown
The procedure below must be
performed if the system has to be
stopped for a prolonged period, for
example seasonal shutdown.
1. Test the unit for refrigerant leakage
and repair as necessary.
2. Open the electrical disconnect
switches for the chilled-water
pump. Lock the switches in the
"Open" position.
C
CA
AU
UT
TIIO
ON
N
Lock the chilled-water pump
disconnects open to prevent pump
damage.
3. Close all chilled-water supply
valves. Drain the water from the
evaporator.
4. Open the unit main electrical
disconnect and unit-mounted
disconnect (if installed) and lock in
the "Open" position. If the optional
control-power transformer is not
installed, open and lock the 115 V
disconnect.
C
CA
AU
UT
TIIO
ON
N
Lock the disconnects in the "Open"
position to prevent accidental startup
Operation
and damage to the system when it
has been set up for extended
shutdown.
5. At least every three months
(quarterly), check the refrigerant
pressure in the unit to verify that
the refrigerant charge is intact.
C
CA
AU
UT
TIIO
ON
N
During an extended shutdown
period, especially over the winter
season, the evaporator must be
drained of water, if the chilled water
loop does not contain glycol, to
prevent any risk of evaporator freeze-
up.
System Restart After Extended
Shutdown
1. Verify that the liquid-line service
valves, oil line, compressor
discharge service valves, and
suction service valves are open
(backseated).
C
CA
AU
UT
TIIO
ON
N
To prevent damage to the
compressor, ensure that all
refrigerant valves are open before
starting the unit.
2. Check the oil separator oil level
(see Maintenance section).
3. Fill the evaporator water circuit.
Vent the system while it is being
filled. Open the vent on the top of
the evaporator and condenser
while filling, and close it when
filling is completed.
C
CA
AU
UT
TIIO
ON
N
Do not use untreated or improperly
treated water. Equipment damage
may occur.
4. Close the fused-disconnect
switches that provide power to the
chilled-water pump.
5. Start the evaporator water pump
and, while water is circulating,
inspect all piping for leakage.
Make any necessary repairs before
starting the unit.
6. While the water is circulating,
adjust the water flows and check
the water pressure drops through
the evaporator. Refer to "Water-
RLC-SVX03A-E4