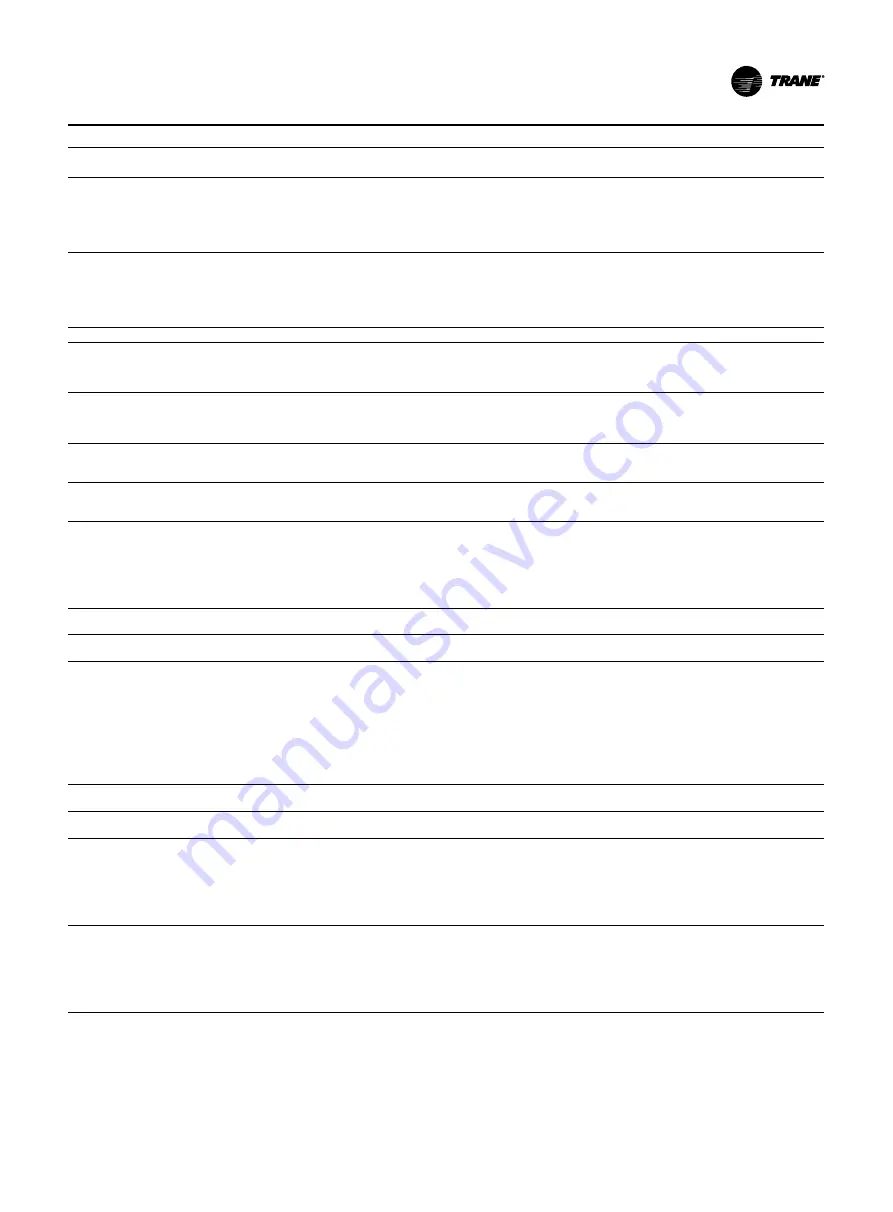
Daily
Every 3
months
Every 6 months
Annual
evaporator and condenser pres-
sures, oil tank pressure, differ-
ential oil pressure and discharge
oil pressure. Compare the read-
ings with the values provided in
the above.
Check the oil level in the chiller
oil sump using the two sight
glasses provided in the oil sump
head. When the unit is oper-
ating, the oil level should be
visible in the lower sight glass.
Complete logs on a daily basis.
Clean all water
strainers in the
water piping
system.
Lubricate the vane control linkage
bearings, ball joints, and pivot
points. See “General Lubrication,”
p. 84.
Lubricate vane operator tang
O-rings. See “General Lubrication,”
p. 84.
Lubricate the oil filter shutoff valve
O-rings. See
Step 7
in “Oil Filter
Replacement Procedure,” p. 83.
Drain contents of the rupture
disc and purge discharge ventline
drip-leg into an evacuated waste
container. Do this more often if the
purge is operated excessively. Ap-
ply oil to any exposed metal parts
to prevent rust.
Shut down the chiller once each year to check the
items listed on the “Annual Inspection Checklist”.
Refer to Operation and Maintenance Guide to perform
purge maintenance procedures once a year.
Use an ice water bath to verify that the accuracy
of the evaporator refrigerant temperature sensor
(4R10) is still within tolerance (+ or - 2.0°F at
32°F (1°C at 0°C)). If the evaporator refrigerant
temperature displayed on the control panel read-
out is outside this 4-degree tolerance range,
replace the sensor. If the sensor is exposed to
temperature extremes outside its normal operat-
ing range (0°F to 90°F) (-18°C to 32°C), check its
accuracy at six- month intervals.
Inspect the condenser tubes for fouling; clean if
necessary.
Submit a sample of the compressor oil to a Trane
qualified laboratory for comprehensive analysis.
Measure the compressor motor winding resistance
to ground; a qualified service technician should
conduct this check to ensure that the findings are
properly interpreted. Contact a qualified service
organization to leak-test the chiller; this proce-
dure is especially important if the system requires
frequent purging.
Every 3 years, use a nondestructive tube test to inspect the condenser and evaporator tubes.
Note:
It may be desirable to perform tube tests on these components at more frequent intervals, depending upon chiller application. This is espe-
cially true of critical process equipment.
Contact a qualified service organization to determine when to conduct a complete examination of the unit to discern the condition of the compres
-
sor and internal components.
Note:
(a) Chronic air leaks, which can cause acidic conditions in the compressor oil and result in premature bearing wear; and, (b) Evaporator or
condenser water tube leaks. Water mixed with the compressor oil can result in bearing pitting, corrosion, or excessive wear
RELEASED 10/Mar/2020 06:59:20 GMT