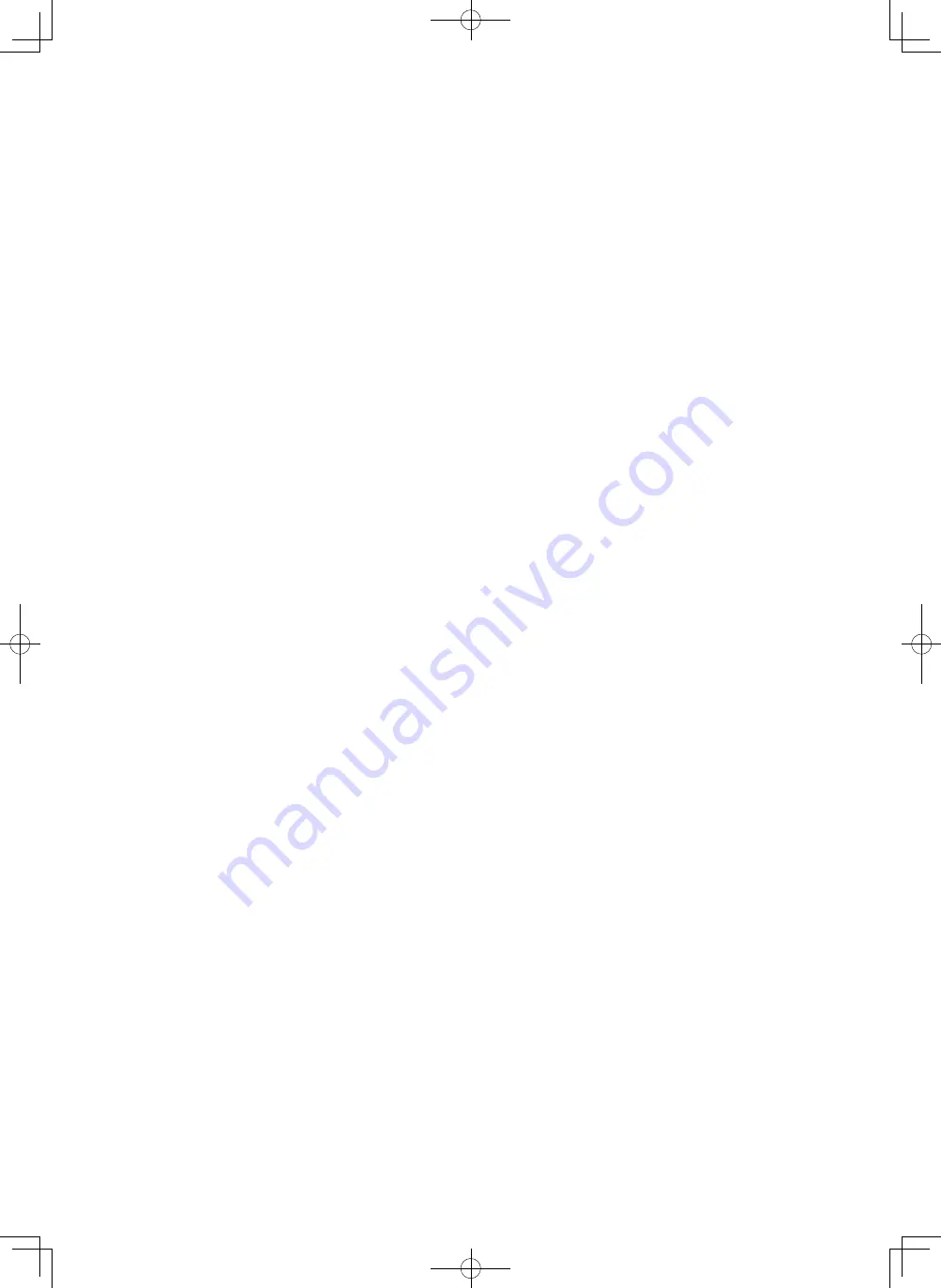
ENGLISH
6
9. NOTE FOR MAINTENANCE WORK
1. Checks to the area
Prior to beginning work on systems containing flammable re-
frigerants, safety checks are necessary to ensure that the risk
of ignition is minimised. For repair to the refrigerating system,
the following precautions shall be complied with prior to con-
ducting work on the system.
Work procedure
Work shall be undertaken under a controlled procedure so as
to minimise the risk of a flammable gas or vapour being pres-
ent while the work is being performed.
2. General work area
All maintenance staff and others working in the local area shall
be instructed on the nature of work being carried out. Work in
confined spaces shall be avoided. The area around the work-
space shall be sectioned off. Ensure that the conditions within
the area have been made safe by control of flammable material.
3. Checking for presence of refrigerant
The area shall be checked with an appropriate refrigerant detec-
tor prior to and during work, to ensure the technician is aware of
potentially flammable atmospheres. Ensure that the leak detec-
tion equipment being used is suitable for use with flammable re-
frigerant, i.e. nonsparking, adequately sealed or intrinsically safe.
4. Presence of fire extinguisher
If any hot work is to be conducted on the refrigeration equip-
ment or any associated parts, appropriate fire extinguishing
equipment shall be available to hand. Have a dry powder or
CO2 fire extinguisher adjacent to the charging area.
5. No ignition sources
No person carrying out work in relation to a refrigerant system
which involves exposing any pipe work that contains or has
contained flammable refrigerant shall use any sources of igni-
tion in such a manner that it may lead to the risk of fire or explo-
sion. All possible ignition sources, including cigarette smoking,
should be kept sufficiently far away from the site of installation,
repairing, removing and disposal, during which flammable re-
frigerant can possibly be released to the surrounding space.
Prior to work taking place, the area around the equipment is to
be surveyed to make sure that there are no flammable hazards
or ignition risks. ”No Smoking” signs shall be displayed.
6. Ventilated area
Ensure that the area is in the open or that it is adequately venti-
lated before breaking into the system or conducting any hot
wok. A degree of ventilation shall continue during the period
that the work is carried out. The ventilation should safely dis-
perse any released refrigerant and preferably expel it externally
into the atmosphere.
7. Checks to the refrigeration equipment
Where electrical components are being changed, they shall be
fit for the purpose and to the correct specification. At all times
the manufacturer’s maintenance and service guidelines shall be
followed. If in doubt consult the manufacturer’s technical de-
partment for assistance.
The following checks shall be applied to installations using
flammable refrigerants:
- the charge size in accordance with the room size within which
the refrigerant containing parts are installed;
- the ventilation machinery and outlets are operating adequately
and are not obstructed.
8. Checks to electrical devices
Repair and maintenance to electrical components shall include
initial safety checks and components inspection procedures. If
a fault exists that could compromise safety, then no electrical
supply shall be connected to the circuit until it is satisfactorily
dealt with. If the fault cannot be corrected immediately but it is
necessary to continue operation, an adequate temporary solu-
tion shall be used. This shall be reported to the owner of the
equipment so all parties are advised.
Initial safety checks shall include:
- that capacitors are discharged: this shall be done in a safe
manner to avoid possibility of sparking;
- that there no live electrical components and wiring are ex-
posed while charging, recovering or purging the system;
- that there is continuity of earth bonding.
9. Repairs to sealed components
During repairs to sealed components, all electrical supplies
shall be disconnected from the equipment being worked upon
prior to any removal of sealed covers, etc.
If it is absolutely necessary to have an electrical supply to
equipment during servicing, then a permanently operating form
of leak detection shall be located at the most critical point to
warn of a potentially hazardous situation.
Particular attention shall be paid to the following to ensure that
by working on electrical components, the casing is not altered
in such a way that the level of protection is affected. This shall
include damage to cables, excessive number of connections,
terminals not made to original specification, damage to seals,
incorrect fitting of glands, etc.
Ensure that apparatus is mounted securely.
Ensure that seals or sealing materials have not degraded such
that they no longer serve the purpose of preventing the ingress
of flammable atmospheres, Replacement parts shall be in ac-
cordance with the manufacturer’s specifications.
NOTE: The use of silicon sealant may inhibit the effectiveness of
some types of leak detection equipment. Intrinsically safe
components do not have to be isolated prior to working on
them.
10. Repair to intrinsically safe components
Do not apply any permanent inductive or capacitance loads to
the circuit without ensuring that this will not exceed the permis-
sible voltage and current permitted for the equipment in use.
Intrinsically components are the only types that can be worked
on while live in the presence of a flammable atmosphere. The
test apparatus shall be at the correct rating.
Replace components only with parts specified by manufactur-
er. Other parts may result in the ignition of refrigerant in the at-
mosphere from a leak.
11. Cabling
Check that cabling will not be subject to wear, corrosion, ex-
cessive pressure, vibration, sharp edges or any other adverse
environmental effects. The check shall also take into account
the effects of aging or continual vibration from sources such as
compressors or fans.
12. Leakage detection for flammable refrigerants
Under no circumstances shall potential sources of ignition be
used in the searching for or detection of refrigerant leaks. A ha-
lide torch (or any other detector using a naked flame) shall not be
used.
13. Leak detection methods
The following leak detection methods are acceptable for sys-
tems containing flammable refrigerant.
Electronic leak detectors shall be used to detect flammable re-
frigerants, but the sensitivity may not be adequate, or may
need recalibration (Detection equipment shall be calibrated in a
refrigerant-free area). Ensure that detector is not a potential
source of ignition and is suitable for the refrigerant used.
Leak detection fluids are suitable for use with most refrigerants
but the use of detergents containing chlorine shall be avoided
as the chlorine may react with the refrigerant and corrode the
copper pipe-work.
If a leak is suspected, all naked flames shall be removed/extin-
guished.
If a leak of refrigerant is found which requires brazing, all of the
refrigerant shall be recovered from the system. Oxygen free ni-
trogen (OFN) shall then be purged through the system both be-
fore and during the brazing process.
14. Removal and evacuation
When breaking into the refrigerant circuit to make repairs-or for
any other purpose-conventional procedures shall be used.
However, it is important that best practice is followed since
Flammability is a consideration. The following procedure shall
be adhered to:
Remove refrigerant;
Purge the circuit with inert gas;
Evacuate;
Purge again with inert gas;
Open the circuit by cutting or brazing.
The refrigerant charge shall be recovered into the correct re-
covery cylinders. The system shall be “flushed” with OFN to
render the unit safe. This process may need to be repeated