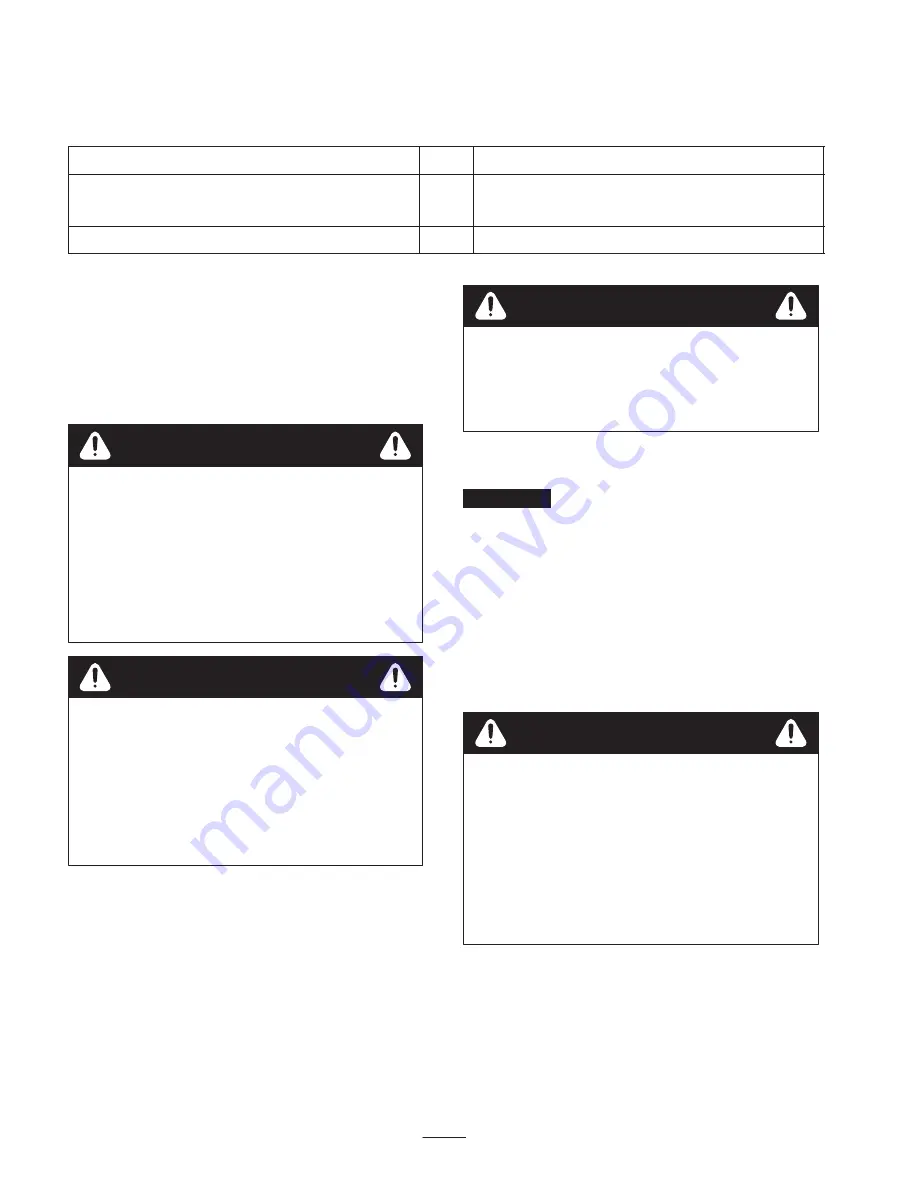
8
Setup
Note:
Determine the left and right side of the machine from the normal operating position.
Description
Qty.
Use
Operator’s Manual
Engine Operator’s Manual
1
1
Read before operating the machine.
Parts Catalog
1
Remove, Activate And Charge
Battery
1.
If Battery is not filled with electrolyte or activated, bulk
electrolyte with 1.260 specific gravity must be
purchased from a local battery supply outlet and added
to battery.
Danger
Battery electrolyte contains sulfuric acid which is a
deadly poison and causes severe burns.
•
Do not drink electrolyte and avoid contact with
skin, eyes or clothing. Wear safety glasses to
shield your eyes and rubber gloves to protect
your hands.
•
Fill the battery where clean water is always
available for flushing the skin.
CALIFORNIA
Proposition 65 Warning
Battery posts, terminals, and related accessories
contain lead and lead compounds, chemicals
known to the State of California to cause cancer
and reproductive harm.
Wash hands after
handling.
Warning
2.
Unhook springs from battery cover, remove cover and
lift battery out of battery box.
3.
Remove filler caps from battery and slowly fill each
cell until electrolyte is up to fill line.
4.
Replace filler caps and connect a 3 to 4 amp battery
charger to the battery posts. Charge the battery at a rate
of 3 to 4 amperes for 4 to 8 hours.
Charging the battery produces gasses that can
explode.
Never smoke near the battery and keep sparks and
flames away from battery.
Warning
5.
Remove filler caps and slowly add electrolyte to each
cell until level is up fill line. Install filler caps.
Important
Do not overfill battery. Electrolyte will
overflow onto other parts of the machine and severe
corrosion and deterioration will result.
6.
When battery is charged, disconnect charger from
electrical outlet and battery posts. Allow battery to sit
for 5 to 10 minutes before proceeding to next step.
Install Battery
1.
Slide the battery into battery box with the terminals to
the inside.
Battery terminals or metal tools could short
against metal tractor components causing sparks.
Sparks can cause the battery gasses to explode,
resulting in personal injury.
•
When removing or installing the battery, do not
allow the battery terminals to touch any metal
parts of the tractor.
•
Do not allow metal tools to short between the
battery terminals and metal parts of the tractor.
Warning
2.
Attach the negative cable (wire from engine block) to
the negative (–) terminal of the battery.
Содержание RAKE-O-VAC 07050
Страница 6: ...6 92 8309 93 4041...