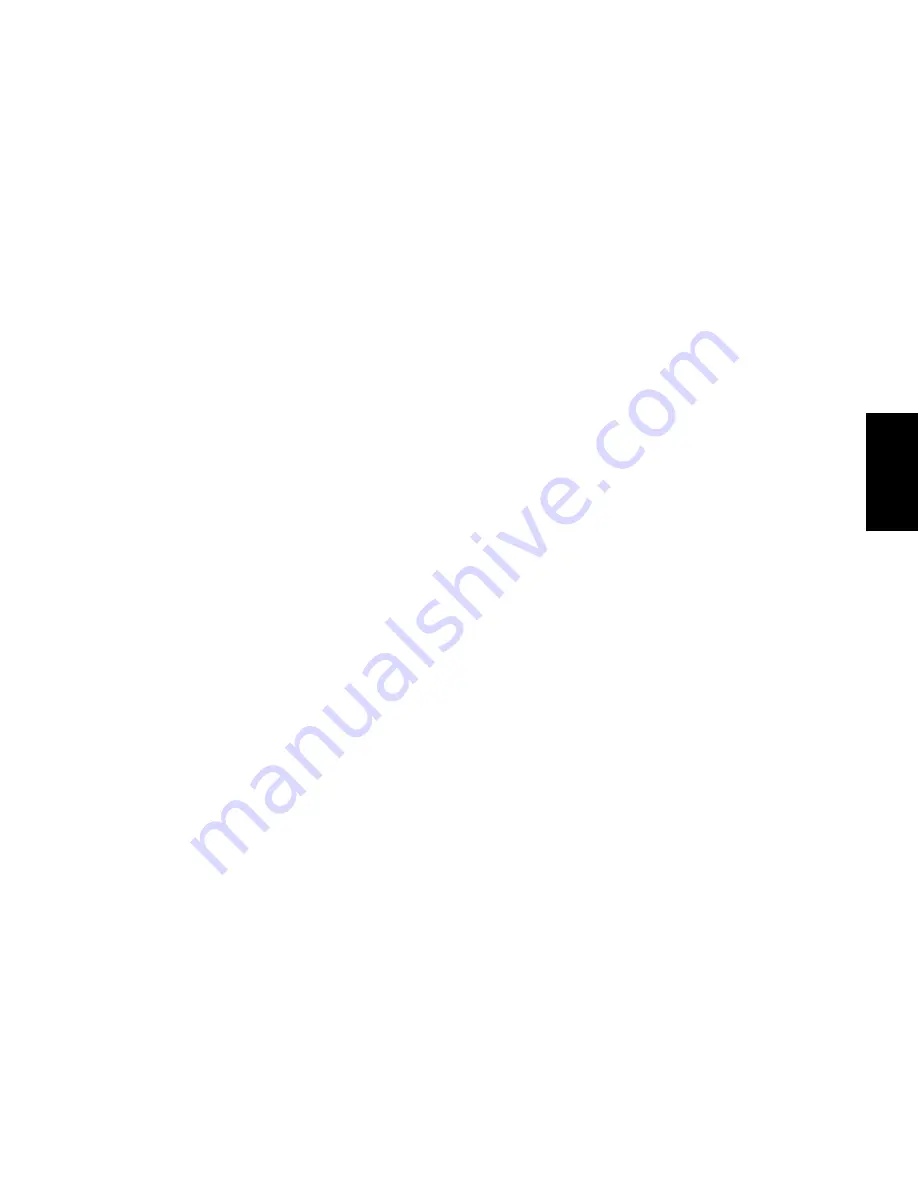
Groundsmaster 4100--D
Hydraulic System
Page 4 -- 95
Removal
1. Park machine on a level surface, lower cutting
decks, stop engine, engage parking brake, and remove
key from the ignition switch.
2. Read the General Precautions for Removing and
Installing Hydraulic System Components at the begin-
ning of the Service and Repairs section of this chapter.
3. To prevent contamination of hydraulic system during
steering valve removal, thoroughly clean exterior of
steering valve and fittings.
4. Remove steering valve from machine using Figure
75 as a guide.
Installation
1. Install steering valve using Figure 75 as a guide.
2. Make sure hydraulic tank is full. Add correct oil if nec-
essary before returning machine to service (see Opera-
tor’s Manual).
Hydraulic System
Содержание 30411
Страница 1: ...Form No 03116SL Rev G Groundsmaster 4100 D Model 30411 Original Instructions EN...
Страница 4: ...NOTES _...
Страница 6: ...Groundsmaster 4100 D This page is intentionally blank...
Страница 8: ...Groundsmaster 4100 D This page is intentionally blank...
Страница 14: ...Groundsmaster 4100 D Page 1 6 Safety This page is intentionally blank...
Страница 16: ...Groundsmaster 4100 D Page 2 2 Product Records and Maintenance Equivalents and Conversions...
Страница 22: ...Groundsmaster 4100 D Page 2 8 Product Records and Maintenance This page is intentionally blank...
Страница 27: ...Groundsmaster 4100 D Page 3 5 Kubota Diesel Engine Rev A This page is intentionally blank Kubota Diesel Engine...
Страница 42: ...Groundsmaster 4100 D Page 3 20 Kubota Diesel Engine Rev A This page is intentionally blank...
Страница 48: ...Groundsmaster 4100 D Hydraulic System Page 4 6 This page is intentionally blank...
Страница 99: ...Groundsmaster 4100 D Hydraulic System Page 4 57 This page is intentionally blank Hydraulic System...
Страница 115: ...Groundsmaster 4100 D Hydraulic System Page 4 73 This page is intentionally blank Hydraulic System...
Страница 126: ...Groundsmaster 4100 D Hydraulic System Page 4 84 This page is intentionally blank...
Страница 131: ...Groundsmaster 4100 D Hydraulic System Page 4 89 This page is intentionally blank Hydraulic System...
Страница 190: ...Groundsmaster 4100 D Page 5 36 Electrical System This page is intentionally blank...
Страница 197: ...Groundsmaster 4100 D Page 6 7 Axles Planetaries and Brakes This page is intentionally blank Axles Planetaries and Brakes...
Страница 226: ...Groundsmaster 4100 D Page 7 8 Chassis This page is intentionally blank...
Страница 231: ...Groundsmaster 4100 D Cutting Deck Page 8 5 This page is intentionally blank Cutting Deck...
Страница 235: ...Groundsmaster 4100 D Cutting Deck Page 8 9 This page is intentionally blank Cutting Deck...
Страница 246: ...Groundsmaster 4100 D Cutting Deck Page 8 20 This page is intentionally blank...
Страница 248: ...Groundsmaster 4100 D Electrical Diagrams Page 9 2 This page is intentionally blank...
Страница 250: ...Page 9 4 Glow Plug Circuit Power Current Control Current Indication Current Logic Direction Groundsmaster 4100 D...
Страница 251: ...Page 9 5 Crank Circuit Power Current Control Current Indication Current Logic Direction Groundsmaster 4100 D...
Страница 252: ...Page 9 6 Run Transport Circuit Power Current Control Current Indication Current Logic Direction Groundsmaster 4100 D...
Страница 255: ...Page 9 9 Groundsmaster 4100 D Main Wire Harness...
Страница 257: ...Page 9 11 Groundsmaster 4100 D Engine Wire Harness D4 D2 D6...
Страница 259: ...Page 9 13 Groundsmaster 4100 D Front Wire Harness D7 D8 D5...
Страница 261: ...Page 9 15 Groundsmaster 4100 D Cutting Deck Wire Harnesses...
Страница 262: ......