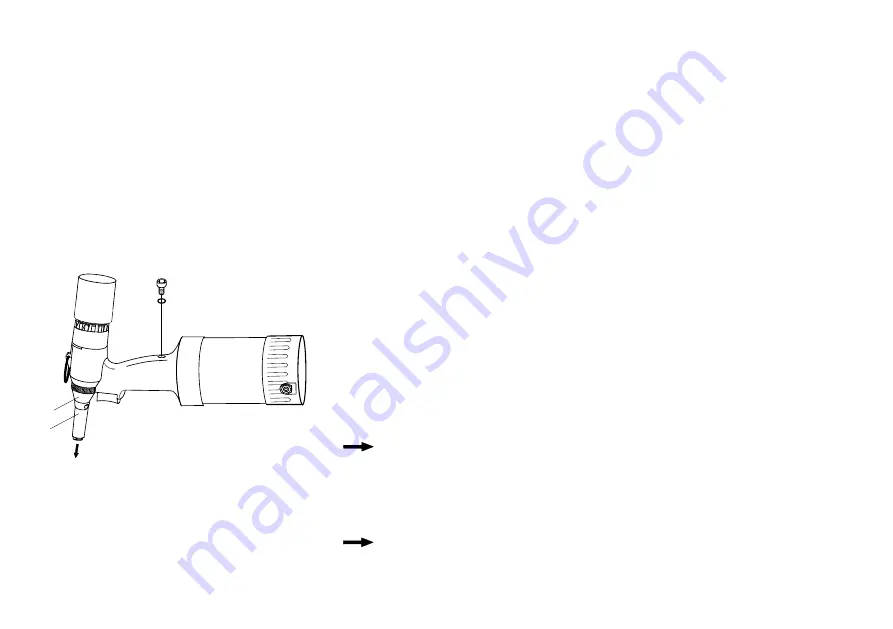
20
Maintaining the riveting tool
Caution
Hazard of injury if handled in an improper manner! Servicing,
maintenance and repairs of the riveting tools must be carried
out professionally. On completing this work, there should not be
any more hazard to the operator, if used as per the regulations.
The operator may only carry out the operations mentioned
here.
Bleeding the hydraulic section, refilling hydraulic oil
It is necessary to bleed the hydraulic system or to refill the hydraulic oil
when:
— oil is leaking from defective O-rings,
— after an oil-change at the time of an overhaul
(either after a maximum of 3 years, or after 2000 working hours).
• Detach the compressed air connection.
Caution
Hazard of injury by means of bruises or cuts in case of
unchecked cutting stroke! Always detach compressed air
supply before unscrewing the nose cap (2).
Note
Unscrew nose cap (2), so that there is no more pressure on the
hydraulic cylinder, else it would not be possible to fill in adequa-
te oil
• Unscrew the knurled nut (12) up to the end stop.
Note
If you clamp the riveting tool into a vice, then insert a soft mate-
rial in-between (Alu/ wood)
H
H
2
12