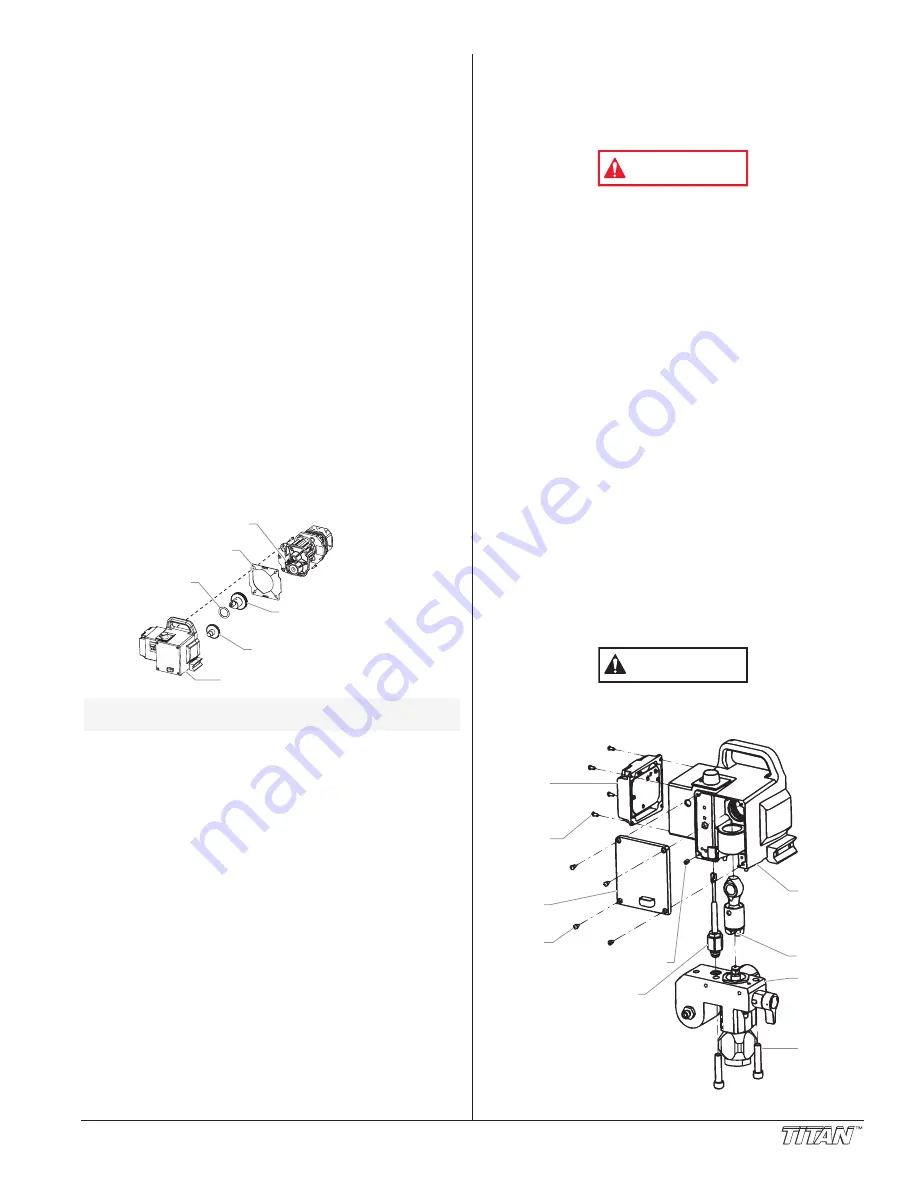
Replacing the Gears
1. Unplug the unit.
2. Loosen and remove the four motor shroud screws.
Remove the motor shroud.
3. Release the baffle tape on the side of the baffle assembly
and slip the baffle assembly off of the motor. Remove the
four baffle spacers.
4. Slide the electronic cover off of the electronic control
assembly on the motor.
5. Loosen and remove the four heat sink assembly mounting
screws. Pull back the heat sink assembly to access and
disconnect the two wires coming from the motor.
6. At the electronic control assembly:
a. Disconnect the white wire coming from the power cord
and the white wire coming from the ON/OFF switch.
b. Disconnect the three wires coming from the
potentiometer and the phone jack-style connector
coming from the transducer.
c. Disconnect the seven wires coming from the indicator
lights assembly.
7. Loosen and remove the four motor mounting screws.
8. Pull the motor out of the gear box housing.
9. Inspect the rotor gear on the end of the motor for damage
or excessive wear. If this gear is completely worn out,
replace the motor.
10. Remove and inspect the 2nd stage gear assembly for
damage or excessive wear. Replace, if necessary.
11. Remove and inspect the crankshaft/gear assembly for
damage or excessive wear. If damaged or worn, replace
the crankshaft/gear assembly.
12. Install the motor into the gear box housing. Make sure the
housing gasket is positioned properly and the thrust
washer is in place.
13. Secure the motor with the four motor mounting screws.
14. Reconnect the wires to the electronic control assembly
(refer to the electrical schematic in the Parts List section
of this manual).
15. Connect the two motor wires to the heat sink assembly.
16. Position the electronic cover over the electronic control
assembly.
17. Position the heat sink assembly on the gear box housing
and secure in position with the four heat sink assembly
mounting screws
18. Slip the baffle assembly around the motor. Secure the
baffle assembly with the baffle tape. Slip the four baffle
spacers into position between the rear bell of the motor
and the baffle assembly.
19. Slide the motor shroud over the motor. Make sure the
housing gasket is positioned properly.
20. Secure the motor shroud with the four motor shroud
screws.
NOTE: Clean and refill the gear box cavity up to the rear
face of each gear with Lubriplate (P/N 314-171).
Crankshaft/Gear Assembly
2nd Stage Gear Assembly
Gear Box Housing
Housing Gasket
Rotor Gear
Thrust Washer
Replacing the Transducer
1. Loosen and remove the four front cover screws. Remove
the front cover.
2. Stop the sprayer at the bottom of its stroke so that the
piston is in its lowest position. Turn off and unplug the
sprayer.
Before proceeding, follow the Pressure Relief Procedure
outlined previously in this manual. Additionally, follow all
other warnings to reduce the risk of an injection injury,
injury from moving parts or electric shock. Always unplug
the sprayer before servicing!
3. Tilt the pump back for easy access to the fluid section.
4. Using a 3/8” hex wrench, loosen and remove the two
pump block mounting screws.
5. Pull the pump block down approximately 1/2” from the
gear box housing to clear the transducer.
6. Slide the pump block and piston rod forward until the
piston rod is out of the T-slot on the slider assembly.
7. Loosen and remove the four heat sink assembly mounting
screws.
8. Pull back the heat sink assembly for access to the
transducer wire plug-in.
9. Follow the wire from the transducer to the heat sink
assembly and unplug the transducer wire from the heat
sink assembly.
10. Using an 1/8” hex wrench, loosen and remove the set
screw from the bottom of the gear box housing.
11. Slide the transducer assembly out of the bottom of the
gear box housing.
12. Install the new transducer assembly into the gear box
housing.
13. Thread the set screw into the gear box housing and
tighten securely.
14. Plug the transducer wire into the heat sink assembly
where the old transducer wire was located.
15. Reassemble the pump by reversing steps 1–8.
Make sure the transducer is aligned properly with the hole
in the pump block during reassembly. Improper alignment
may cause damage to the transducer gasket.
T-Slot
Gear Box
Housing
Pump
Block
Pump
Block
Mounting
Screw
Front
Cover
Heat Sink
Assembly
Mounting
Screw
Heat Sink
Assembly
Front
Cover
Screw
Set Screw
Transducer
Assembly
CAUTION
WARNING
© Titan Tool Inc. All rights reserved.
9