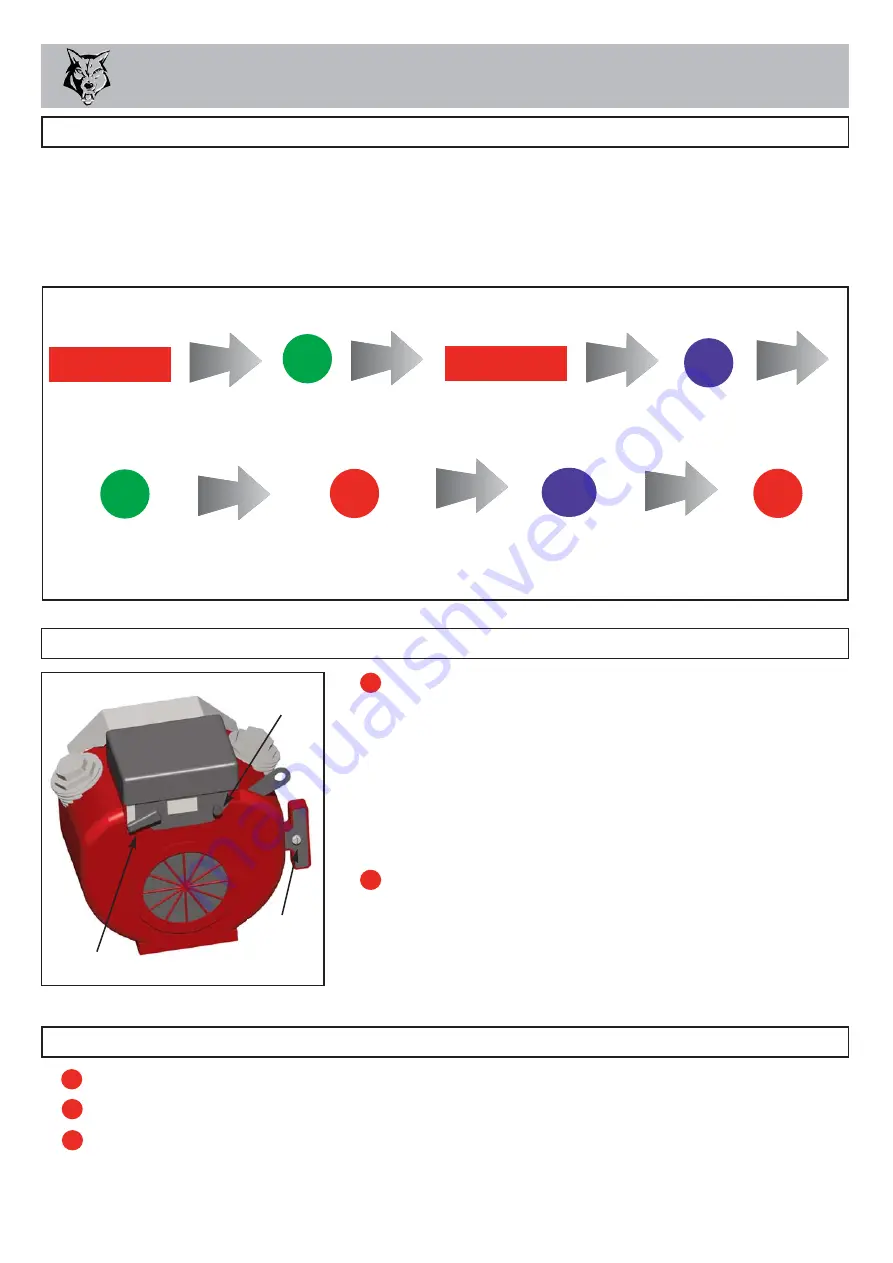
OPERATING INSTRUCTIONS
11
BEFORE USING THE CHIPPER
IT IS ESSENTIAL TO CARRY OUT THE FOLLOWING TESTS
to check safety equipment - this
sequence of tests will only take a few seconds to carry out. We recommend that these tests are
carried out daily. Observing the function as described will confirm that the safety circuits are working
correctly. This is also a good opportunity to remind all operators of the control and emergency stop
systems.
4
7
5
6
8
2
3
PRESS THE GREEN
BUTTON
THE ROLLERS
SHOULD RUN
PRESS THE RED BAR
THE ROLLERS
SHOULD STOP
PRESS THE BLUE BUTTON
THE ROLLERS SHOULD TURN
BACKWARDS ONLY WHILE THE
BUTTON IS PRESSED
PRESS THE GREEN BUT-
TON AGAIN
THE ROLLERS
SHOULD RUN
PRESS THE EMERGENCY
RED BUTTON
THE ROLLERS
SHOULD STOP
PRESS THE BLUE BUT-
TON
THE ROLLERS
SHOULD NOT TURN
PULL TO RESET
THE RED BUTTON
THE MACHINE IS
READY TO USE
1
PRESS THE RED
BAR TO POWER
THE CONTROL
SYSTEM
WITH THE ENGINE RUNNING AT FULL SPEED
STOPPING THE ENGINE
SET
engine to idle position.
ALLOW
to run for at least one full minute.
SWITCH
off and remove ignition key.
For more detailed information refer to the Engine Owner’s Manual
STARTING THE ENGINE
FOR A COLD ENGINE:
Place the throttle control at 1/3 throttle and pull the
choke out.
Insert ignition key into starter switch.
Turn the key to start the engine. Release the key as
soon as the engine starts.
Gradually return the choke to the off position as the
engine starts and warms up. Allow the engine to warm
up for at least one minute before chipping.
FOR A WARM ENGINE:
Follow the instructions for a ‘cold engine’ but return the
choke to the off position as soon as the engine starts.
If engine fails to start after 10 seconds leave for 1
minute and try again.
CHOKE
STARTER
SWITCH
THROTTLE LEVER
Содержание TW 125PH
Страница 23: ...CERTIFICATE OF CONFORMITY 22...
Страница 27: ...ELECTRICAL DETAIL 26...
Страница 29: ...HYDRAULIC LAYOUT 28 HY323 MOTOR MOTOR PUMP TANK HY1422 HY1423 HY1421 HY2750 HY1420 FILTER DCV...
Страница 30: ...blank...