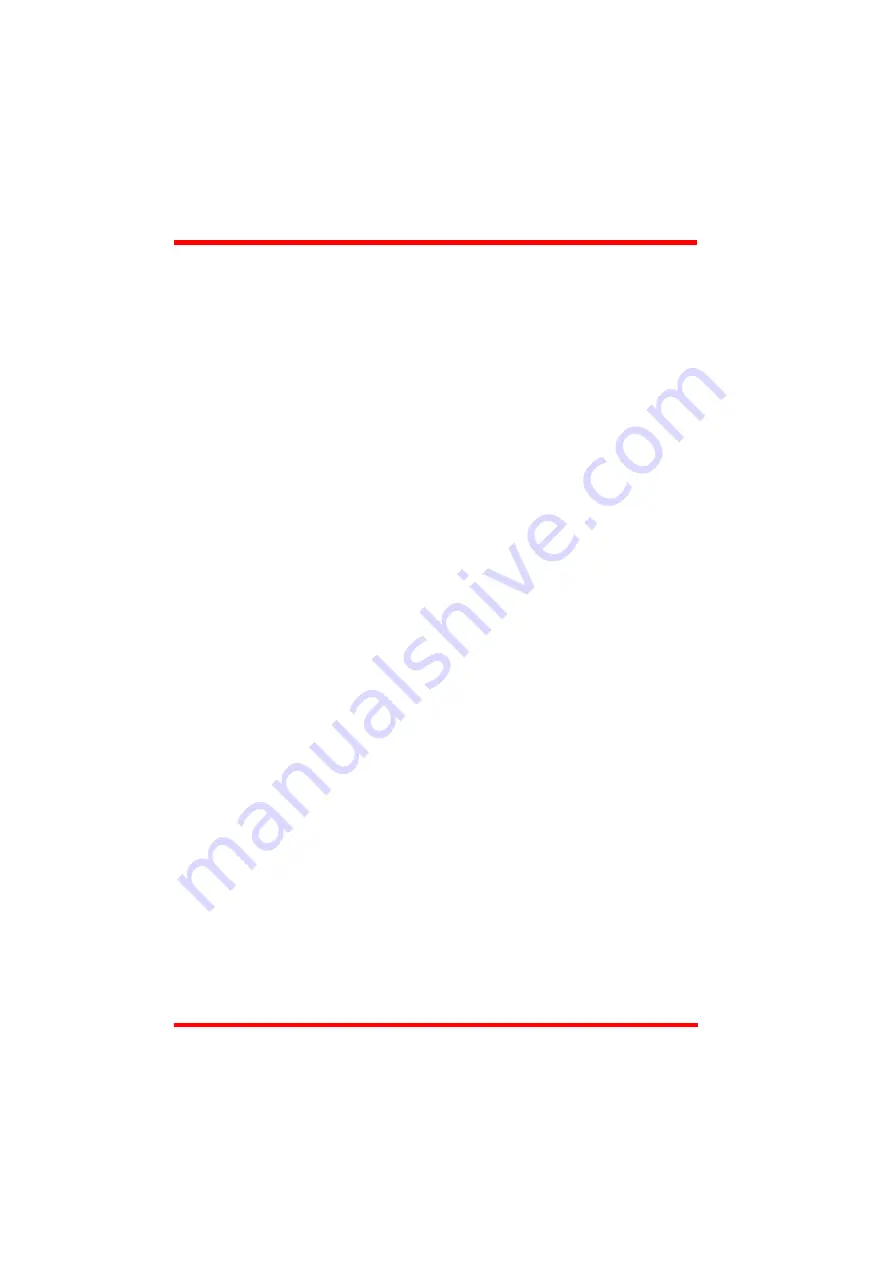
44
HA0165T Rev 4K Sept 2017
Chapter 6
a value of 5.0 corresponding to one half the range of piezo motion - see Section
D.2.2. for further details and helpful hints on setting the correct circle size.
If the Diameter Mode is set to '
LUT
', the circle diameter is adjusted automatically,
using a tabl e of ran ge dependent diameter values set in the LUT TIA Range
parameters. This setting enables a look up table (LUT) of circle diameter values
(in NanoTrak units, 0 to 5) to be specified as a function of input range.
When automatic LUT diameter adjustm ent mode is enabled, the system uses
values in this LUT to modify circle diameter in relation to the input range currently
selected.
This LUT diameter adjustment mode allows appropriate circle diameters to be
applied on an application specific basis. Typically, the circle diameter LUT will be
configured to generate a reducing circle diameter for an increasing range setting.
This fits an assumption that higher input signal readings correspond to a smaller
Full Width Half Maximum (FWHM) of the feedback signal peak being tracked, and
so a smaller circle diameter is required to prevent NanoTrak instability.
Phase Compensations
- the feedback loop scenario in a typical NanoTrak application
can involve the operation of various electronic and electromechanical components
(e.g. power meters and piezo actuators) that could introduce phase shifts around the
loop and thereby effect the system stability. These phase shifts can be cancelled by
setting a 'Phase Compensation' factor.
Horizontal
- the phase compensation for the horizontal component of the circle
path.
Vertical
- the phase compensation for the vertical component of the circle path.
The values can be specified in the range -180.0 to 180.0 degrees and typically are set
equal to each other.
Loop Gain
- the gain setting is used to ensure that the DC level of the input (feedback
loop) signal lies within the dynamic range of the input. Increasing this value can lead
to a more responsive NanoTrak behavior as the signal variation around the circular
path is e nhanced. However, for a p articular set up, if this val ue is too high, then
unstable NanoTrak operation (indicated by a fluctuating circle) can result.
The gain value can be specified in the range 100 to 10,000 - see Section D.2.2. for
further details and helpful hints on setting the loop gain.
Track Threshold -
the track th reshold is se t in Amps, and is depe ndent upon the
application. Typically, the value is set to lie above the ‘noise floor’ of the particular
optical arrangement. When the input signal level exceeds this value, the tracking LED
is lit on the GUI panel. However, this is no guarantee that tracking is taking place. If
the threshold value is set inappropriately, e.g. if the tracking threshold is set to below
the noise floor, then the GUI will show a lit tracking LED even though no tracking is
taking place.
The threshold setting can be obtained by calling the GetTrackThreshold method.