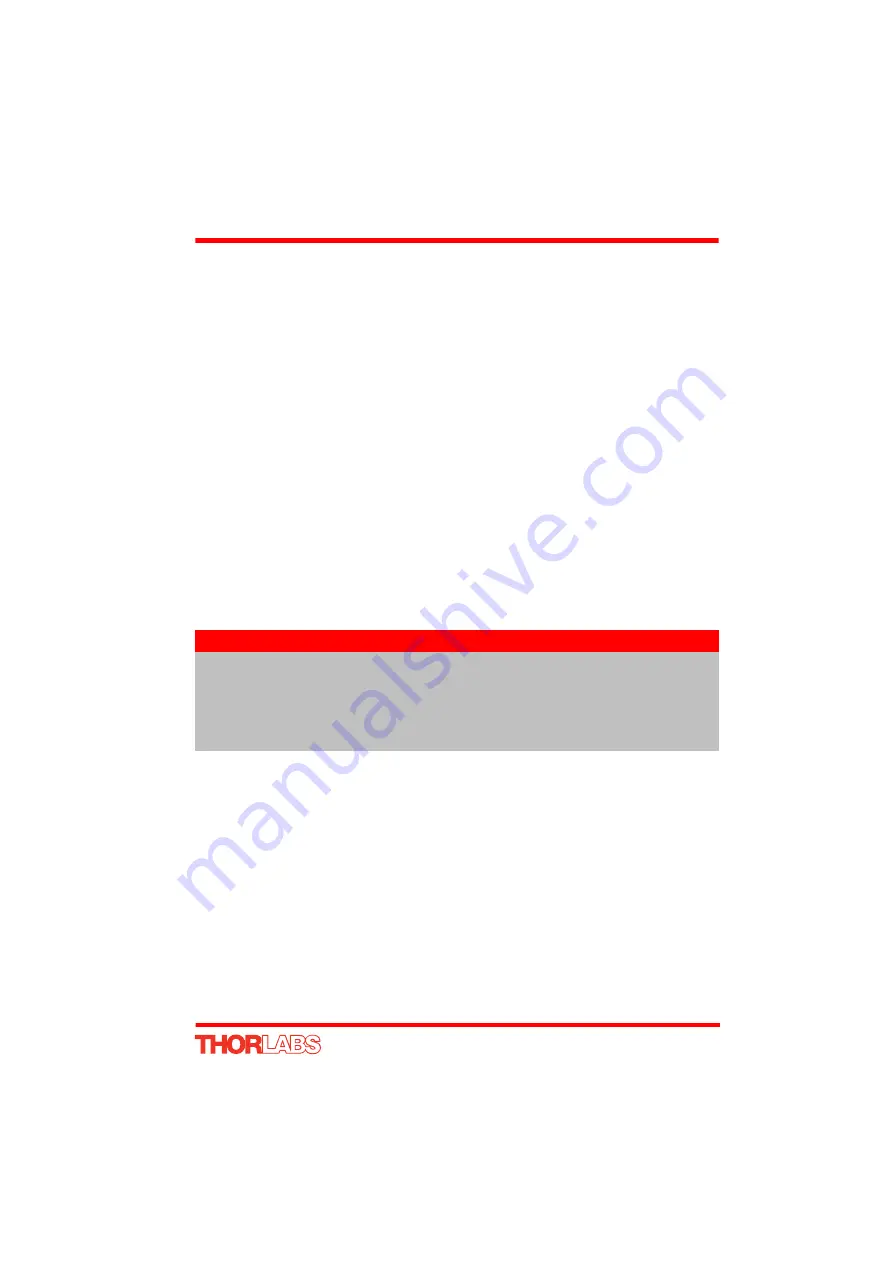
55
K-Cube Brushed DC Servo Motor Driver
Servo Loop (PID) Control Settings
The DC Driver K-Cube implements a full servo control loop for motor velocity and
position control. The loop response to demanded position moves is determined via
Proportional, Integration and Derivative settings. These settings can be altered using
the ‘Servo Loop (PID) Control Settings’ parameters.
Proportional
– This parameter makes a change to the output which is proportional to
the positional error value. A high proportional gain results in a large change in the
output for a given error. It accepts values in the range 0 to 32767.
Integral
– This parameter accelerates the process towards the demanded position,
ensuring that the positional error is eventually reduced to zero. If set too high, the
output can overshoot the demand value. Under a constant torque loading, the static
position error is zero. It accepts values in the range 0 to 32767.
Derivative
– This term provides the ‘damping’ force proportional to the rate of change
of the position error, thereby decreasing the overshoot which may be caused by the
integral term. However, the differential term also slows down system response.
It accepts values in the range 0 to 32767.
Integral Limit
– This term sets a maximum limit for the integration term to prevent an
excessive build up over time of the restoring force. It accepts values in the range 0 to
32767.
Note
The default values programmed into the APT software will give
acceptable motor performance in most cases. These PID parameters are
set according to the stage or actuator type associated with the driver
using the APTConfig utility (see APTConfig helpfile or the handbook
supplied with the unit). However, under extreme loading conditions it may
be necessary to alter these factory default values.