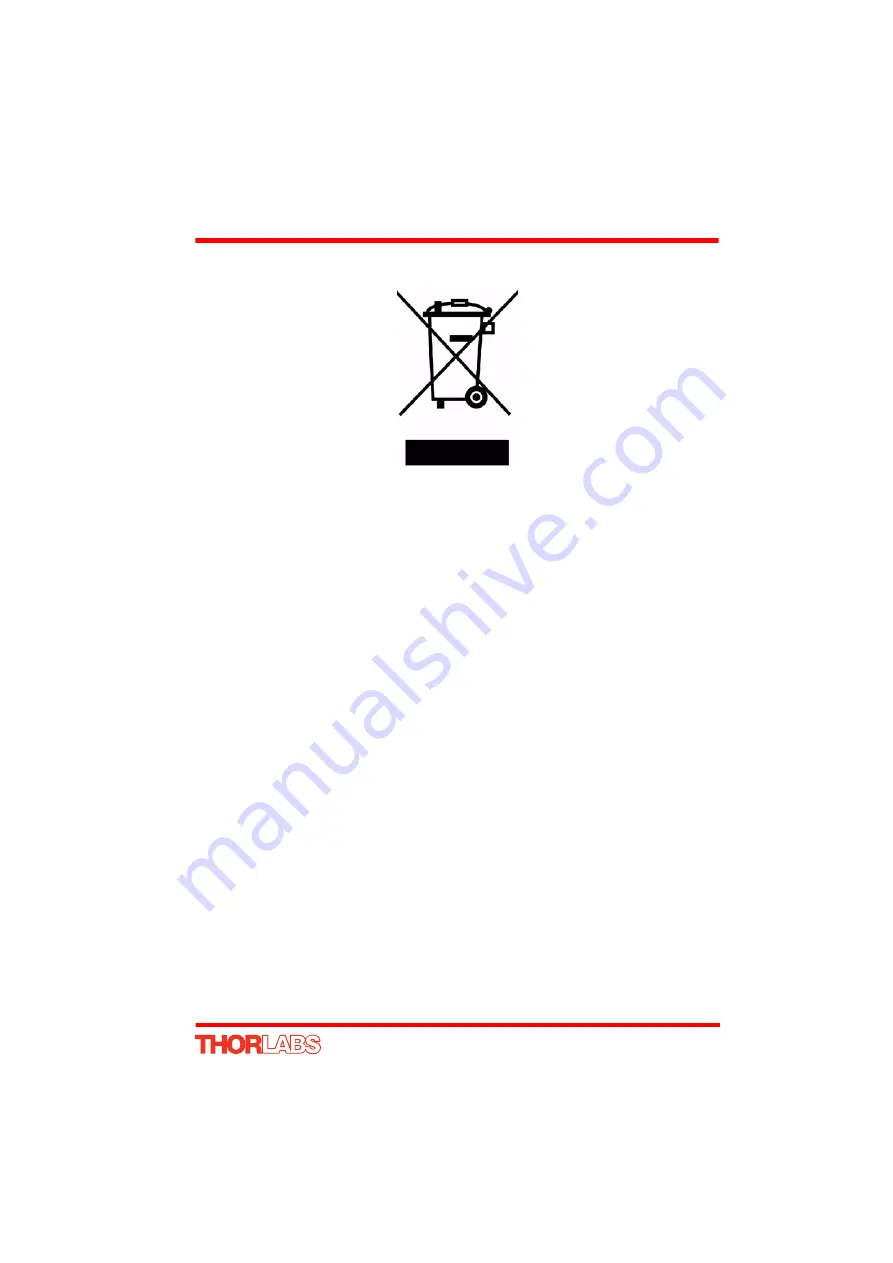
69
Single Channel Stepper Motor Controller
Fig. 7.1 Crossed out "wheelie bin" symbol
As the WEEE directive applies to self contained operational electrical and electronic
products, this "end of life" take back service does not refer to other products, such as
• pure OEM products, that means assemblies to be built into a unit by the user (e. g.
OEM laser driver cards)
• components
• mechanics and optics
• left over parts of units disassembled by the user (PCB's, housings etc.).
If you wish to return a unit for waste recovery, please contact Thorlabs or your nearest
dealer for further information.
G.2.2 Waste treatment on your own responsibility
If you do not return an "end of life" unit to the company, you must hand it to a company
specialized in waste recovery. Do not dispose of the unit in a litter bin or at a public
waste disposal site.
G.2.3 Ecological background
It is we ll known that WEEE p ollutes the environment by re leasing toxic p roducts
during decomposition. The aim of the European RoHS dire ctive is to redu ce the
content of toxic substances in electronic products in the future.
The intent of the W EEE directive is to enforce the recycling of WEEE. A controlled
recycling of end of life pro ducts will thereby avoid negative impacts on the
environment.