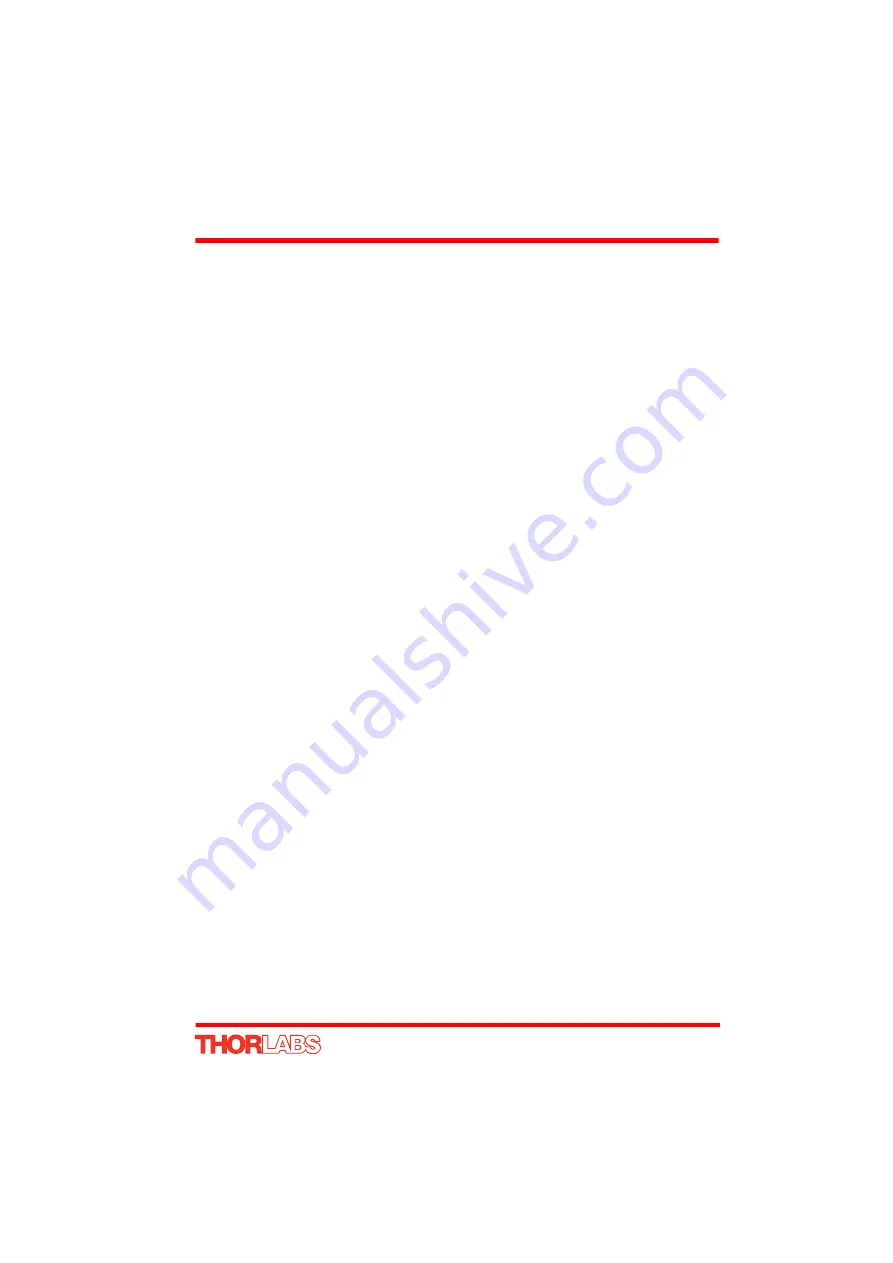
5
Single Channel Stepper Motor Controller
set using velocity profile parameters. The inclusion of a ‘Bow Index’ parameter within
these settings enables the choice of trapezoidal or S-curve velocity profiles.
Similarly, home seq uences have a full set of associated parameters that can be
adjusted for a particul ar stage or actuat or. For simplicity of opera tion, the apt™
software incorporates pre-configured settings for each of the Thorlabs stages and
actuators, while still exposing all parameters individually for use with other stepper
motor driven systems.
For convenience and ease of use, adjustment of many key parameters is possible
through direct interaction with the graphical panel. For example a move to the next
position can be initiated by clicking directly on the position display and entering a new
value (see the tutorial in Chapter 4 for further details). Furthermore, all such settings
and parameters are also accessible through the ActiveX® programmable interfaces
for automated alignment sequences.
The apt™ stepper unit also supports encoder feedback through dedicated quadrature
encoded pulse (QEP) inputs, one for each channel of operation. Through conversion
routines, the apt™ software is able to use this feedback signal to generate encoder
position for access either through the GUI or via programmable interfaces for custom
closed loop algorithms. A “buil t in” algorithm can be en abled to all ow the stepp er
system to reach and maintain an encoded position through an iterative move
sequence. Please see th e handbook supplied with your linear encoded stage for
further details.
In the remainder of this handbook, the Tutorial section (Chapter 4) provides a good
initial understanding on using the unit, and the reference sections (Chapter 5) covers
all operating modes and parameters in detail.
2.2
APT PC Software Overview
2.2.1
Introduction
As a member of the APT range of controllers, the BSC201 stepper controller shares
many of the associated software benefits. This includes USB connectivity (allowing
multiple units to be used together on a single PC), fully featured Graphical User
Interface (GUI) panels, and extensive software f unction libraries for custom
application development.
The APT software suite supplied with all APT con trollers, including the BSC201
stepper controller, provides a flexible and powerful PC based control system both for
users of the equipment, and software programmers aiming to automate its operation.
For users, the APTUser (see Section 2.2.2.) and APTConfig (see Section 2.2.3.)
utilities allow full control of all settings and operating modes enabling complete ‘out-
of-box’ operation without the need to d evelop any further cu stom software. Both
utilities are built on top of a sophisticated, multi-threaded ActiveX ‘engine’ (called the
APT server) which provides all of the necessary APT system software services such
as generation of GUI pan els, communications handling for multiple USB units, and
logging of all system activity to assist in hardware trouble shooting. It is this APT
server ‘engine’ that is used by software developers to allow the creation of advanced