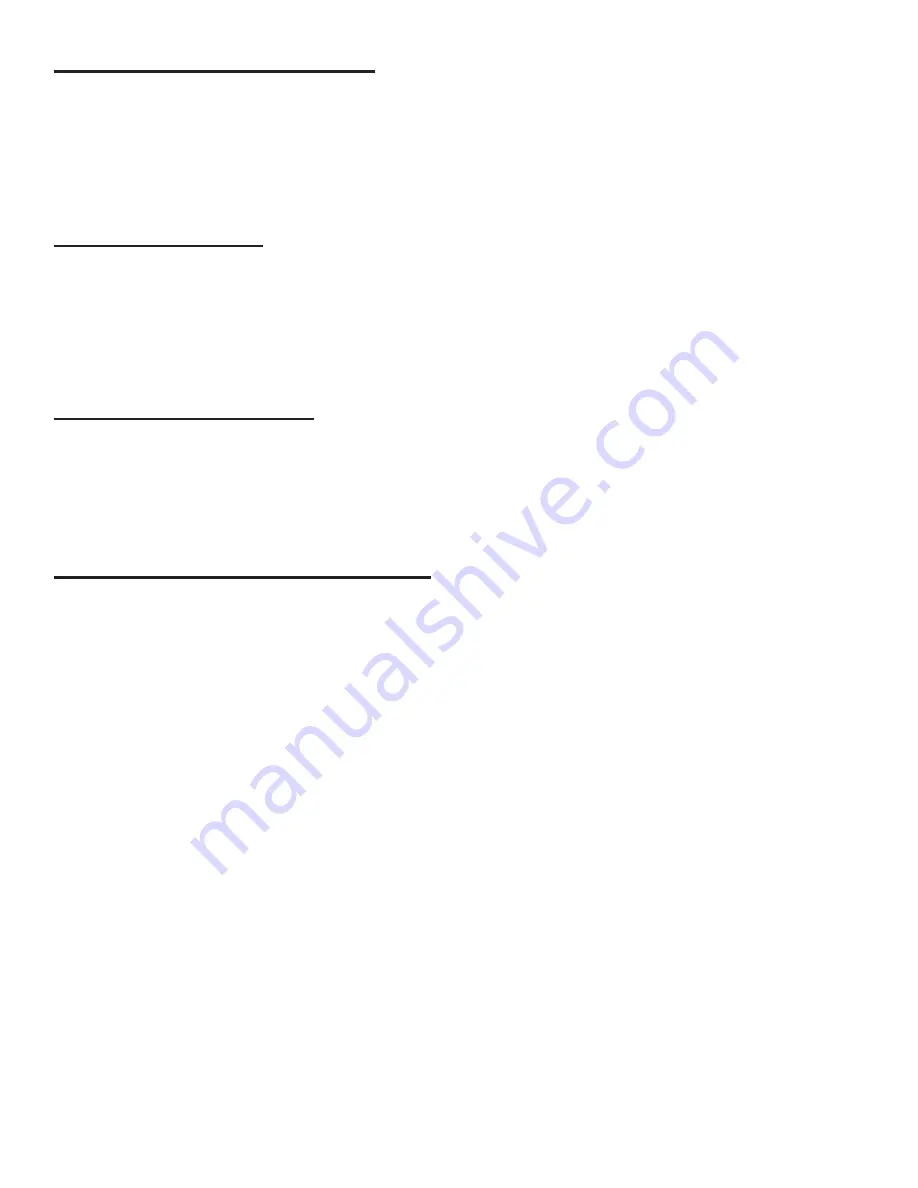
Page 11
Section 5.0: Heat Exchanger Cleaning
The Heater’s heat exchanger and capillary sensor may become clogged/coated with mineral deposits
over time and require cleaning with de-scaling solvents. Cleaning solution must be compatible with
copper alloys, EPDM, Stainless Steel, PTFE, and Buna-N O-rings. (
Recommended manufacturer:
Armstrong’s Clean-In-Place Scale Removal System
)
Unit can be cleaned while installed or disconnected at the unions and cleaned at another location.
Cleaning the unit while installed requires additional fittings (
See Appendix #6
). Tee fittings should be
installed on the water inlet supply line upstream from the inlet union and on the tepid water outlet line
downstream of the outlet union. Four locking ball valves will be needed to isolate the unit from the
plant water supply during cleaning. The first ball valve should be installed upstream of the inlet tee,
the second installed on the leg of the inlet tee, the third installed downstream of the outlet tee, and
the last installed on the leg of the outlet tee where the cleaning system will be connected.
NOTE: Inlet and outlet layout may differ, depending on station version.
Pump solution into normal flow direction, check valves will prevent reverse flow. Cleaning
solution must remain below 80°F. The cleaning time needed depends on local water conditions and
frequency of cleaning. After the solution is drained, flush unit with potable water for 15 minutes to
prevent contamination. If the unit was cleaned while installed, complete the flush before opening the
isolation ball valves. Close the two ball valves on the legs of the tee and open the downstream ball
valve first. Activate the shower/eyewash then open the upstream ball valve and allow the system to
run for several minutes. Open the steam supply valve and check the water outlet temperatures.
Section 4.5: V5 Tempering Valve
V5 Tempering Valve Test
1.
If section 2.2 indicates V5 valve failure, decommission unit and replace V5 valve.
V5 Tempering Valve Replacement
Follow instructions provided with replacement part from ThermOmegaTech®
Section 4.6: V6 Valve
V6 Valve Test
1.
If section 2.2 indicates V6 valve failure, decommission unit and replace V6 valve.
V6 Valve Replacement
Follow instructions provided with replacement part from ThermOmegaTech®
Section 4.7: TV/HAT 155°F
TV/HAT 155°F Valve Test
1.
If section 2.2 indicates TV/HAT 155°F failure, decommission unit and replace TV/HAT155°F valve.
TV/HAT 155°F Valve Replacement
Follow instructions provided with replacement part from ThermOmegaTech®
Содержание THERM-O-MIX STATION
Страница 13: ...Page 12 Appendix 1 Station Schematic...
Страница 14: ...Appendix 2 Station Operating Logic Flow Chart Page 13...
Страница 15: ...Page 14 Appendix 3 Typical Installation Schematic...
Страница 16: ...Appendix 4 Labeled Station Line Drawing Page 15...
Страница 17: ...Page 16 Appendix 5 Hoses and Hose Fittings Line Drawing...