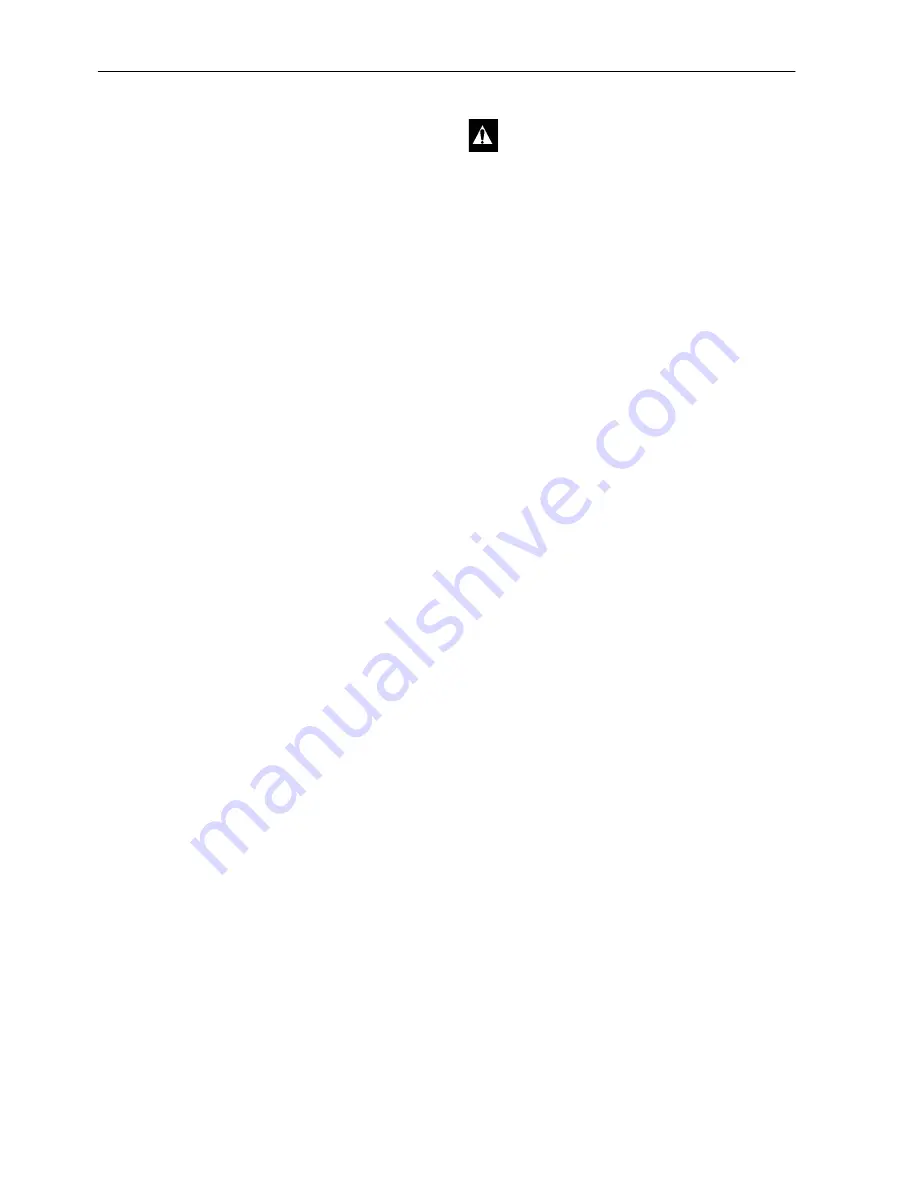
Engine Maintenance
108
Injection Pump Installation
1. Replace the shim set if it has been damaged
during the pump removal. New shims are
supplied in sets. Select a set with the same
thickness as that removed from the pump.
NOTE: Do not put gasket sealer on the shim
set or the pump until the injection pump
timing has been checked. The shim set may
have to be replaced with one of a different
thickness.
2. Center the rack in the pump body and insert
the pump into the timing gear cover. The rack
pin must be aligned with the governor arm as
the pump is being inserted.
3. Install the clip that fastens the rack pin to the
governor arm.
4. Install the washers and nuts. Torque the nuts
to 18 to 20 ft-in (24 to 27 N•m).
5. Install the injection lines and the fuel lines.
Timing the Injection Pump to the
Engine
There are two different types of timing procedures
used on this engine. One procedure involves
checking to make sure the cylinders are timed
correctly to each other. The second procedure
times the injection pump correctly to the engine.
If the cylinders are not timed correctly to each
other, it is of no value to time the injection pump
to the engine because at least one of the cylinders
would be out of time. The individual plungers in
the injection pump are timed to each other by the
use of spacers in the pump plunger base. It is
unlikely that an injection pump would change
individual cylinder timing unless it had been
through some type of repair process, but if all
other possible problems with a rough running
engine have been checked, and especially if the
engine’s injection pump has been replaced or
repaired recently, it may be worthwhile to check
the individual cylinder timing. Because the
possibility of incorrect individual cylinder timing
is so minimal, the procedure for timing the pump
to the engine will be covered first. The procedure
for individual cylinder timing is very similar to
timing the injection pump so it will be covered
last.
NOTE: The timing marks for each of the three
cylinders are stamped on the flywheel 120
degrees apart. Top dead center marks are
identified by the number of the cylinder stamped
next to them. Injection timing marks are
unmarked. To find the timing marks, open the
curbside door and look under the air cleaner.
The index timing mark is stamped on the side of
the starter plate that faces the flywheel. It is
located 0.39 in. (10 mm) below the center of the
round notch in the edge of the starter plate.
Locate the index timing mark by feeling the back
side or the starter plate. To make it easier to
align the timing marks, file a V-notch in the edge
of the starter plate in line with the index timing
mark. Later units may already have the V-notch
in the edge of the starter plate.
1. Rotate the engine in the direction of rotation
(clockwise as viewed from the water pump
end) until the number 1 cylinder (closest to
flywheel) is at approximately top dead center
of the compression stroke. The valve cover
should be removed to identify the
compression stroke. Both rocker arms of the
number 1 cylinder will be loose.
2. Remove the injection line from the number 1
injector and the injection pump. Remove the
delivery valve holder, delivery valve and
spring. Care must be taken to prevent dirt
from entering the fuel injection system.
Replace the delivery valve holder and the
delivery valve.
3. Install a drip tube on the delivery valve holder.
CAUTION: The cylinders on the engine
are numbered from the flywheel end to the
water pump end. The number 1 cylinder is
next to the flywheel. The number 2
cylinder is the center cylinder. The
number 3 cylinder is next to the water
pump. The timing marks on the flywheel
match this numbering system.
Содержание 914970
Страница 3: ...3...
Страница 10: ...Table of Contents 10...
Страница 27: ...Unit Description 27 Unit Photographs Figure 1 Roadside View Figure 2 Curbside View PUB122 PUB123...
Страница 40: ...Operating Instructions 40...
Страница 82: ...Electronic Controls 82...
Страница 92: ...Electrical Maintenance 92...
Страница 124: ...Refrigeration Maintenance 124...
Страница 140: ...Hilliard Clutch Maintenance 140...
Страница 160: ...Refrigeration Diagrams 160...
Страница 163: ...Index 163 W wiring 85 wiring diagrams 165...
Страница 164: ...Index 164...
Страница 166: ...Wiring and Schematic Diagrams Index 166...
Страница 167: ...167 Cab Control RD Wiring Diagram...
Страница 168: ...168 RD w o Thermostat Cab Control Schematic...
Страница 169: ...169 RD Cab Box Wiring Diagram...
Страница 170: ...170 RD Cab Control w Thermostat Schematic Diagram...
Страница 171: ...171 RD 50 STD 3 Phase Wiring Diagram Page 1 of 2...
Страница 172: ...172 RD 50 STD 3 Phase Wiring Diagram Page 2 of 2...
Страница 173: ...173 RD 50 STD 3 Phase Schematic Diagram Page 1 of 2...
Страница 174: ...174 RD 50 STD 3 Phase Schematic Diagram Page 2 of 2...
Страница 175: ...175 RD 30 STD Wiring Diagram Page 1 of 2...
Страница 176: ...176 RD 30 STD Wiring Diagram Page 2 of 2...
Страница 177: ...177 RD 30 STD Schematic Diagram Page 1 of 2...
Страница 178: ...178 RD 30 STD Schematic Diagram Page 2 of 2...
Страница 179: ...179 RD 30 C S Wiring Diagram Page 1 of 2...
Страница 180: ...180 RD 30 C S Wiring Diagram Page 2 of 2...
Страница 181: ...181 RD w CYCLE SENTRY Schematic Diagram Page 1 of 2...
Страница 182: ...182 RD w CYCLE SENTRY Schematic Diagram Page 2 of 2...
Страница 183: ...183 RD 50 C S 3 Phase Wiring Diagram Page 1 of 2...
Страница 184: ...184 RD 50 C S 3 Phase Wiring Diagram Page 2 of 2...
Страница 185: ...185 RD w CYCLE SENTRY Schematic Diagram Page 1 of 2...
Страница 186: ...186 RD w CYCLE SENTRY Schematic Diagram Page 2 of 2...