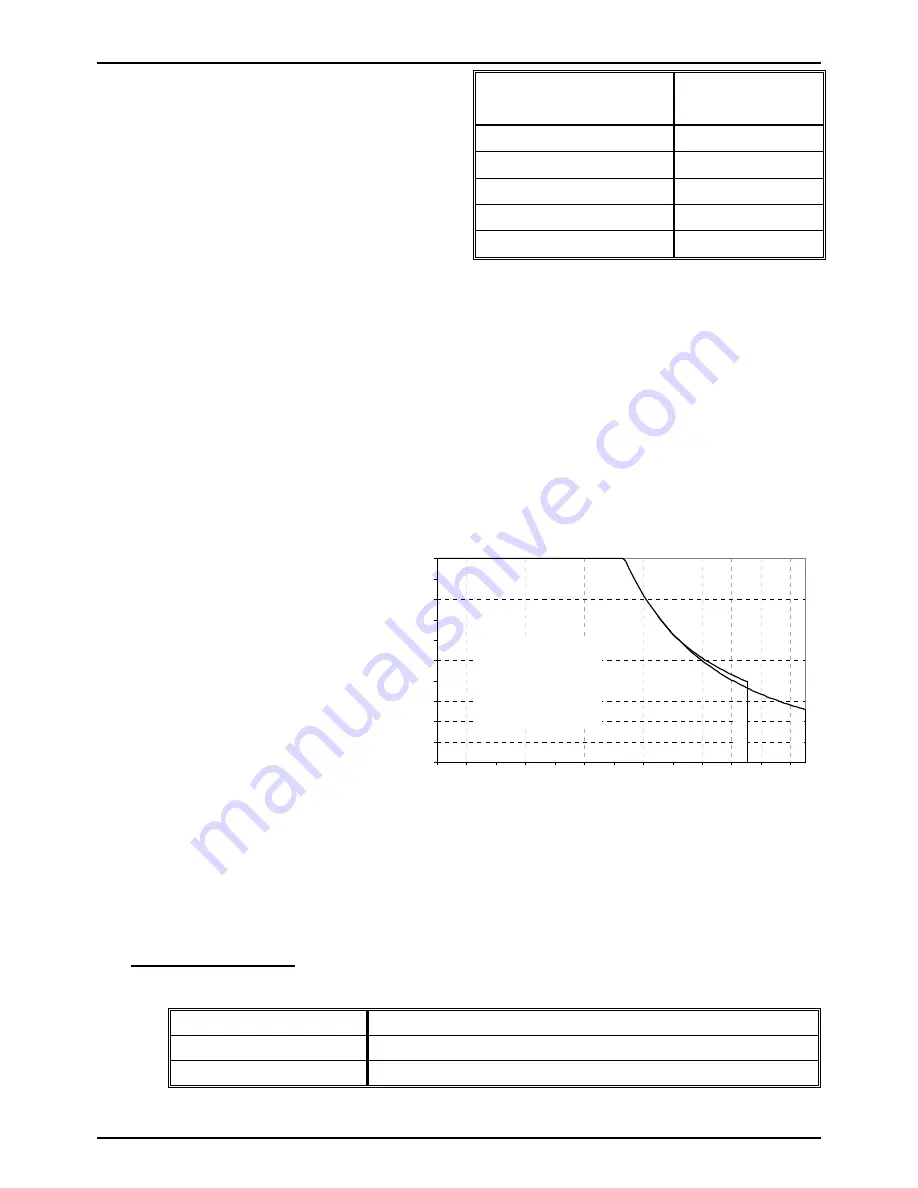
Viking 210GM, 250GM
10
2.3 Welding
Protection
It is recommended to use a welding
helmet, conforming to the local relevant
Standards when electric arc welding.
Use a welding helmet in serviceable
condition with the correct filter lens
fitted as per Table 1.
2.4 User
Responsibility
This equipment will perform as per the
information contained herein when
installed, operated, maintained and
repaired in accordance with the instructions provided. This equipment must be checked
periodically. Defective equipment (including welding leads) should not be used. Parts that are
broken, missing, plainly worn, distorted or contaminated, should be replaced immediately. Should
such repairs or replacements become necessary, it is recommended that such repairs be carried out
by appropriately qualified persons approved by THERMAL DYNAMICS. Advice in this regard
can be obtained by contacting THERMAL DYNAMICS.
This equipment or any of its parts should not be altered from standard specification without prior
written approval of THERMAL DYNAMICS. The user of this equipment shall have the sole
responsibility for any malfunction which results from improper use or unauthorised modification
from standard specification, faulty maintenance, damage or improper repair by anyone other than
appropriately qualified persons approved by THERMAL DYNAMICS.
2.5 Duty
Cycle
The rated duty cycle of a
welding Power Source is the
operating time it may be used
at its rated output current
without exceeding the
temperature limits of the
insulation of the component
parts. To explain the ten minute
duty cycle period the following
example is used. Suppose a
welding Power Source is
designed to operate at 30%
duty cycle, 250 amperes at 26
volts. This means that it has
been designed and built to provide the rated amperage (250A) at the rated load voltage (26V), for
3.0 minutes out of every 10 minute period (30% of 10 minutes is 3.0 minutes). During the other
7.0 minutes of the 10 minute period the Power Source must idle and be allowed to cool. The
thermal cut-out will operate if the duty cycle is exceeded.
3. SPECIFICATIONS
3.1 MIG Torch Specifications
Torch Catelog Number
10-6105
Torch Type
TWECO 250A (Eliminator Consumables)
Torch Cable Length
3.6 metres (12 ft)
Approximate range of
welding current
Filter lens
required for MIG
Up to 150
Shade 10
150-250 Shade
11
250-300 Shade
12
300-350 Shade
13
Over 350
Shade 14
Table 1 - Filter lens size verses welding current
0
10
20
30
40
50
60
70
80
90
100
0
20
40
60
80
100
120
140
160
180
200
220
240
Welding Current (amps)
Duty Cycle (percentage)
250
Vi
ki
ng 210 GM
Vi
ki
ng 250 GM
Safe
Operating
Region
210
Figure 1 - Viking duty cycle curves
Содержание Viking 210GM
Страница 21: ...Viking 210GM 250GM 16 6 WELDING GUIDE VIKING 210GM...
Страница 22: ...Viking 210GM 250GM 17 7 WELDING GUIDE VIKING 250GM...
Страница 40: ...Viking 210GM 250GM 35 14 VIKING 210GM CIRCUIT DIAGRAM...
Страница 41: ...Viking 210GM 250GM 36 15 VIKING 250GM CIRCUIT DIAGRAM...
Страница 42: ...Viking 210GM 250GM 37 16 PRINTED CIRCUIT BOARD CIRCUIT DIAGRAM CAT NO 10 6100...