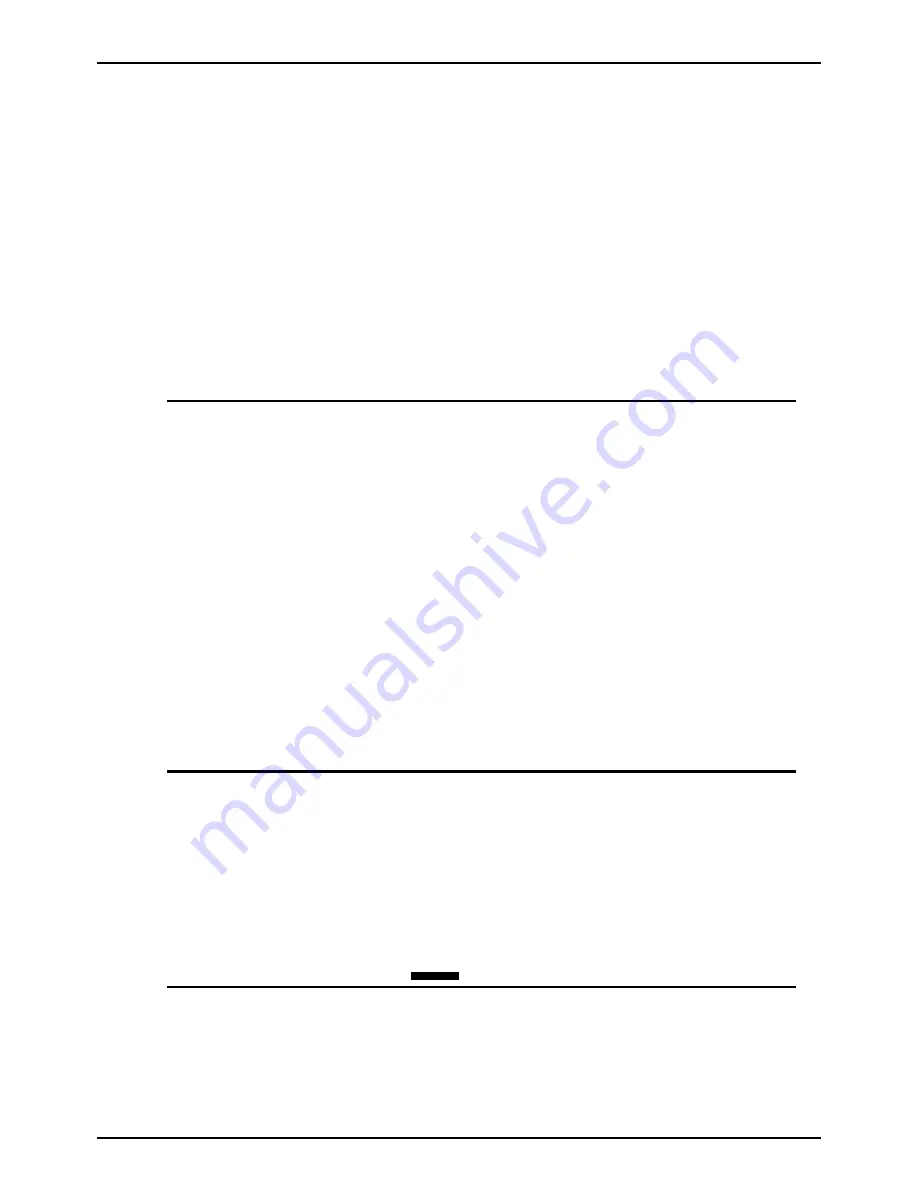
Viking 210GM, 250GM
20
8.10 Spot Timer (Compact Models Only)
With the
MODE SELECTOR
switch is switched to the
SPOT
position, the
SPOT TIME
knob
controls the duration of a single spot weld.
With the
MODE SELECTOR
switch is switched to the
STITCH
position, the
SPOT TIME
knob
controls the welding or 'ON' time whilst stitch welding.
8.11 Dwell Timer (Compact Models Only)
The
DWELL TIME
knob controls the interval or 'OFF' time whilst stitch welding.
8.12 Mode Selector
Switch (Compact Models Only)
The Mode Selector switch selects the method of welding mode.
a)
SPOT
This mode of welding is used to weld two plates together at a desired
location by melting the top & bottom plates together to form a nugget
between them. The spot time period is set by the
SPOT TIME
control
knob. Refer to NOTE 2.
NOTE 2
A spot nozzle should be used on the MIG torch to obtain consistent spot welds.
b)
CONTINUOUS
This mode of welding is used to weld two or more components together
with a continuous weld.
c)
STITCH
This mode of welding is used to weld two or more components together
with a stitch weld. The
SPOT TIME
knob controls the welding or 'ON'
time whilst the
DWELL TIME
knob controls the interval or 'OFF' time
for stitch welding.
8.13 Wirefeeder Drive Roller Pressure Adjustment (Compact Models Only)
The moveable roller applies pressure to the grooved roller via screw adjustable spring pressure.
The adjustable spring screw should be adjusted to a minimum pressure that will provide
satisfactory wire feed without slippage. If slipping occurs, and inspection of the wire contact tip
reveals no wear, distortion or burn-back jam, the conduit liner should be checked for kinks and
clogging by
metal flakes and swarf. If this is not the cause of slipping, the feedroll pressure can be
increased by rotating the adjustable spring screw clockwise. The use of excessive pressure may
cause rapid wear of the feed roller, motor shaft and motor bearings.
NOTE 3
Genuine TWECO contact tips and liners should be used. Many non-genuine liners use inferior materials
which can cause wire feed problems.
8.14 Wire Reel Brake (Compact Models Only)
The wire reel hub incorporates a friction brake which is adjusted during manufacture for optimum
braking. If it is considered necessary, adjustment can be made by turning
the large nut inside the
open end of the wire reel hub. Clockwise rotation will tighten the brake. Correct adjustment will
result in the reel circumference continuing no further than 20mm (0.75”)after release of the Torch
trigger switch. The wire should be slack without becoming dislodged from the reel.
CAUTION 4
Excessive tension on the brake will cause rapid wear of mechanical wire feed parts, overheating of electrical
componentry and possibly an increased incidence of wire Burnback into the contact tip.
Содержание Viking 210GM
Страница 21: ...Viking 210GM 250GM 16 6 WELDING GUIDE VIKING 210GM...
Страница 22: ...Viking 210GM 250GM 17 7 WELDING GUIDE VIKING 250GM...
Страница 40: ...Viking 210GM 250GM 35 14 VIKING 210GM CIRCUIT DIAGRAM...
Страница 41: ...Viking 210GM 250GM 36 15 VIKING 250GM CIRCUIT DIAGRAM...
Страница 42: ...Viking 210GM 250GM 37 16 PRINTED CIRCUIT BOARD CIRCUIT DIAGRAM CAT NO 10 6100...