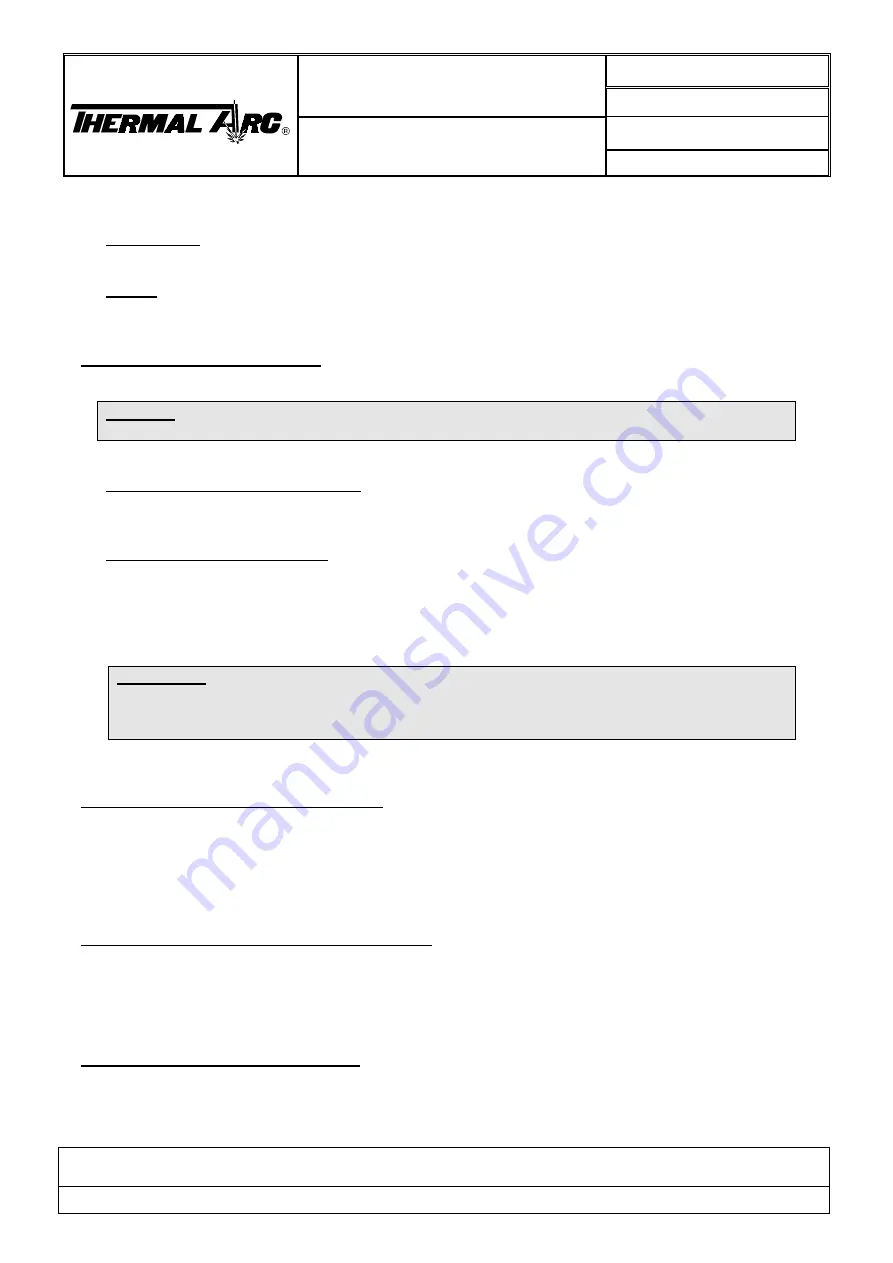
Notice NOT 034
THERMAL ARC 180 AC/DC
Rev : 00
Date : 03/12/02
USING
USER’S MANUAL
Page
2
1/36
PAE ignition
Put the tungsten electrode in direct contact with the workpiece. Push on the trigger.
Raise the torch slowly. The arc strikes. The welding cycle will then be the same as described above.
NOTE
:
This type of ignition is especially useful when welding in surroundings sensitive to radioelectric
disturbances (next to computers or digital controlled equipments).
12.4.
USING REMOTE CONTROL
CAUTION
:
Do not connect at the same time
remote control to socket
B1
and torch with
potentiometer to socket
F1
.
Using remote control RC01 or RC04
The unit recognises the remote control as soon as you plug it in female socket
B1
.
Using torch with potentiometer
The generator is equiped to work with all torches with potentiometer of 10k
Ω
. The connection is
centralised on the female socket
F1
as described in
chapter 9
.
The unit recognises the torch with remote control as soon as you plug it in female socket
F1
.
IMPORTANT :
using the potentiometer of remote control or torch, you can adjust the welding current
from 3A to the current selected with the main potentiometer
F9
of the power source. This value is
displayed on
F5
when the potentiometer of the remote control is on “maximum”.
This allow you to set the welding current with fine adjustment directly on the remote control.
12.5.
CONNECTION OF A COOLING UNIT
Connect directly the cooling unit to the female socket
B3
.
Use a water cooled torch. Connect the water plug to the cooling unit according to the water circulation.
The machine starts the cooling unit automatically when necessary. Lack of water or water circuit
blocked create a default.
12.6.
READING PARAMETERS WHEN WELDING
When welding, digital display
F5
shows welding current in Amps measured by the machine.
It is possible to read the welding voltage when pressing the setting key
F6
. The value is displayed in
Volts (indicator
F18
goes out and
F19
illuminates).
12.7.
VENTILATION IN TIG WELDING
Fan allows the cooling of electronic components.
In TIG welding, ventilation doesn’t start systematically.
Содержание 180 AC
Страница 1: ...THERMAL ARC 180 AC DC USER S MANUAL ...
Страница 34: ...21 WIRING DIAGRAM ...