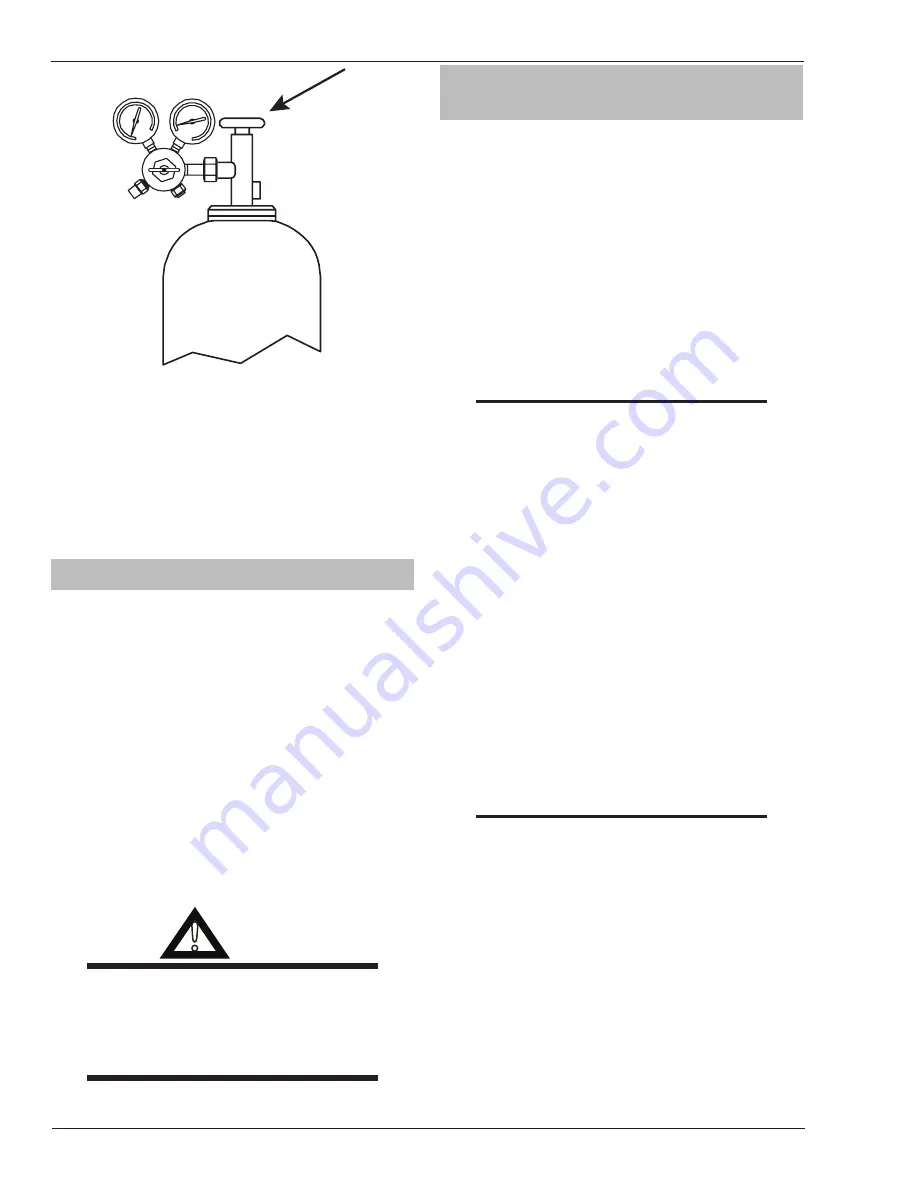
THERMAL ARC 161STL, 201TS
OPERATION
Operation
4-12
Manual 0-5148
Art # A-09828
Figure 4-10: Open Cylinder Valve
3. On all cylinders, except acetylene, open the valve
completely to seal the valve packing. On gaugeless
regulators, the indicator will register the cylinder
contents open.
4. Attach the desired downstream equipment.
4.08 Leak Testing the System
Leak test the system before putting into operation.
1. Be sure that there is a valve in the downstream
equipment to turn off the gas flow.
2. With the cylinder valve open, adjust the regulator
to deliver the maximum required delivery flow
rate.
3. Close the cylinder valve. Watch to see if the high
pressure or contents gauge drops, if it does you
have a leak in the connection between the regula-
tor and the cylinder.
4. Once leak testing has been performed and there
are no leaks in the system, slowly open the cylin-
der valve and proceed.
!
WARNING
If a leak has been detected anywhere in the
system, dis continue use and have the system
repaired. DO NOT use leaking equipment. Do
not attempt to repair a leaking system while
the system is under pressure.
4.09 Lift Start TIG with the Thermal Arc
161STL
Make sure that you have the appropriate shielding gas
set up, attach the shielding gas hose from the torch to a
flow meter regulator on the cylinder. In this case we will
be using Argon set at a flow rate of around 20 CFH. You
will need to use a TIG torch that has a gas valve, and is
properly adjusted. (Tungsten, Collet, Collet body, nozzle,
and back cap).
1. Attach the TIG torch lead to the (-) terminal of the
power supply.
2. Attach the work lead with ground camp to the (+)
terminal of the power source, and your work piece.
NOTE
About tungsten selection for this power
supply, a 2% Thoriated tungsten is generally
used for DC straight polarity welding. Point
the tungsten by grinding a taper on it about
2½ times the diameter of the tungsten used
and grind a slight flat on the end, this will help
stabilize the arc.
To TIG weld with the Thermal Arc 161STL you will need to:
1. Open the torch valve and adjust the argon flow
and close the valve.
2. Turn on the power supply. The switch is located
on the rear panel.
3. Set the weld process to lift TIG. Set the anticipated
amperage needed for the weld on the panel and
turn on the torch valve, touch the tungsten to the
work, as you lift the tungsten off the work, the arc
will start.
NOTE
An alternate method is to set the edge of the
gas cup on the work piece. Rotate the torch so
the tungsten comes in contact with the work.
Roll the torch back to lift the tungsten off the
work and the arc will start.
Содержание 161 STL
Страница 6: ......
Страница 16: ...THERMAL ARC 161STL 201ts INTRODUCTION Introduction 2 2 Manual 0 5148 Notes...
Страница 28: ...THERMAL ARC 161STL 201ts SAFETY AND INSTALLATION Safety and Installation 3 12 Manual 0 5148 Notes...
Страница 42: ...THERMAL ARC 161Stl 201ts THEORY OF OPERATION Theory of Operation 5 2 Manual 0 5148 Notes...
Страница 56: ...THERMAL ARC 161Stl 201TS troubleshooting Troubleshooting 6 14 Manual 0 5148 6 11 161STL Connector Diagram...
Страница 72: ...THERMAL ARC 161Stl 201ts disassembly procedure Disassembly Procedure 7 14 Manual 0 5148 Notes...
Страница 75: ...ASSEMBLY PROCEDURE THERMAL ARC 161stl 201TS Manual 0 5148 8 3 Assembly Procedures 6 7 Art A 10183 8 Art A 09883...
Страница 81: ...ASSEMBLY PROCEDURE THERMAL ARC 161stl 201TS Manual 0 5148 8 9 Assembly Procedures 11 Art A 10190...
Страница 83: ...ASSEMBLY PROCEDURE THERMAL ARC 161stl 201TS Manual 0 5148 8 11 Assembly Procedures 2 Art A 10192...
Страница 84: ...THERMAL ARC 161Stl 201ts ASSEMBLY PROCEDURES Assembly Procedures 8 12 Manual 0 5148 Notes...
Страница 90: ...THERMAL ARC 161Stl 201TS replacement parts Replacement Parts 9 6 Manual 0 5148 Notes...
Страница 92: ...THERMAL ARC 161Stl 201TS accessories Accessories 10 2 Manual 0 5148 Notes...
Страница 95: ......