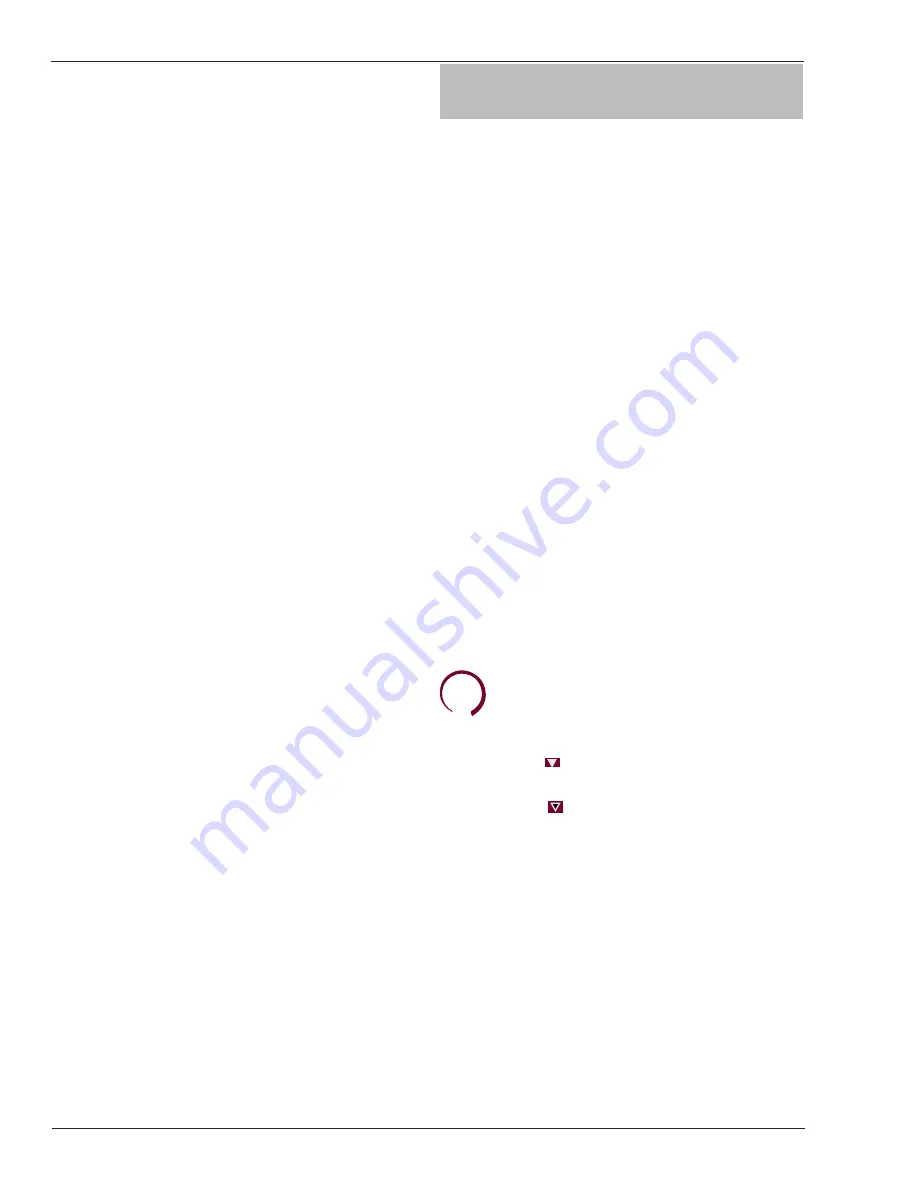
THERMAL ARC 161STL, 201TS
OPERATION
Operation
4-10
Manual 0-5148
3. Connect the TIG torch as follows:
a) Place the power cable into the negative output ter-
minal. It is essential that the male plug is inserted
and turned fully clockwise until connector locks
in place to achieve reliable electrical connection;
b) Place the 8 pin plug into the 8 pin socket. To make
connections, align keyway, insert plug, and rotate
threaded collar fully clockwise.
c) Place the TIG torch gas hose to the gas outlet
and tighten with a wrench. Caution: DO NOT over
tighten.
4. Using a secured Argon cylinder, slowly crack open then
close the cylinder valve while standing off to the side
of the valve. This will remove any debris that may be
around the valve & regulator seat area.
5. Install the regulator (for details of VICTOR regulator,
please refer to 3.09 ) and tighten with a wrench.
6. Connect one end of the supplied gas hose to the outlet
of the Argon regulator and tighten with a wrench. Cau-
tion: DO NOT over tighten.
7. Connect the other end of the supplied gas hose to the
gas inlet fitting on the rear panel of the welder and
tighten with a wrench. Caution: DO NOT over tighten.
8. Open the Argon Cylinder Valve to the fully open posi-
tion.
9. Connect the ground (work) clamp to your work
piece.
10. Set the DOWN SLOPE control knob to the desire weld
current ramp down time. Refer to Section 4.01.
11. Set the weld current control knob to the desired
amperage.
12. The tungsten must be ground to a blunt point in or-
der to achieve optimum welding results. It is critical
to grind the tungsten electrode in the direction the
grinding wheel is turning.
13. Install the tungsten with approximately 1/8” to ¼”
sticking out from the gas cup, ensuring you have
correct sized collet.
14. Tighten the back cap then open the valve on the torch.
15. Plug the power cable into the appropriate outlet, and
turn the switch to the “ON” position. The power L.E.D.
light should illuminate. Set the “Process Selection
Switch” to HF TIG
16. You are now ready to begin HF TIG Welding.
4.06 Welding Current Control
Explanation
15 Amp Outlet
The mains power 15 Amp circuit breaker or fuse should
not trip at this Weld Current value when STICK welding.
The environmental conditions that may cause the mains
power 15 Amp circuit breaker or fuse to trip are:
a) High ambient temperature
b) Worn parts in circuit breaker
c) Using an extension cable
d) Low line mains power voltage
20 Amp Outlet
The mains power 20 Amp circuit breaker or fuse should
not trip at this Weld Current value when STICK welding.
The environmental conditions that may cause the mains
power 20 Amp circuit breaker or fuse to trip are:
a) High ambient temperature
b) Worn parts in circuit breaker
c) Using an extension cable
d) Low line mains power voltage
Output Scale for 115V
The inside number scale identifies the available
output weld current for STICK or LIFT TIG weld modes.
STICK Mode:
Identifies the STICK weld point for 15
Amp outlet.
Identifies the STICK weld point for 20
Amp outlet.
Exceeding these points will cause nui-
sance tripping of the circuit breaker or
fuse.
LIFT TIG Mode/HF TIG Mode: A 15 Amp outlet is ca-
pable of supplying enough input power
for all TIG (GTAW) output weld current
values.
Nuisance tripping should not occur on a 15 Amp outlet.
Output Scale for 208/230V
The outside number scale identifies the available output
weld current for STICK or LIFT TIG /HF TIG weld modes.
Содержание 161 STL
Страница 6: ......
Страница 16: ...THERMAL ARC 161STL 201ts INTRODUCTION Introduction 2 2 Manual 0 5148 Notes...
Страница 28: ...THERMAL ARC 161STL 201ts SAFETY AND INSTALLATION Safety and Installation 3 12 Manual 0 5148 Notes...
Страница 42: ...THERMAL ARC 161Stl 201ts THEORY OF OPERATION Theory of Operation 5 2 Manual 0 5148 Notes...
Страница 56: ...THERMAL ARC 161Stl 201TS troubleshooting Troubleshooting 6 14 Manual 0 5148 6 11 161STL Connector Diagram...
Страница 72: ...THERMAL ARC 161Stl 201ts disassembly procedure Disassembly Procedure 7 14 Manual 0 5148 Notes...
Страница 75: ...ASSEMBLY PROCEDURE THERMAL ARC 161stl 201TS Manual 0 5148 8 3 Assembly Procedures 6 7 Art A 10183 8 Art A 09883...
Страница 81: ...ASSEMBLY PROCEDURE THERMAL ARC 161stl 201TS Manual 0 5148 8 9 Assembly Procedures 11 Art A 10190...
Страница 83: ...ASSEMBLY PROCEDURE THERMAL ARC 161stl 201TS Manual 0 5148 8 11 Assembly Procedures 2 Art A 10192...
Страница 84: ...THERMAL ARC 161Stl 201ts ASSEMBLY PROCEDURES Assembly Procedures 8 12 Manual 0 5148 Notes...
Страница 90: ...THERMAL ARC 161Stl 201TS replacement parts Replacement Parts 9 6 Manual 0 5148 Notes...
Страница 92: ...THERMAL ARC 161Stl 201TS accessories Accessories 10 2 Manual 0 5148 Notes...
Страница 95: ......