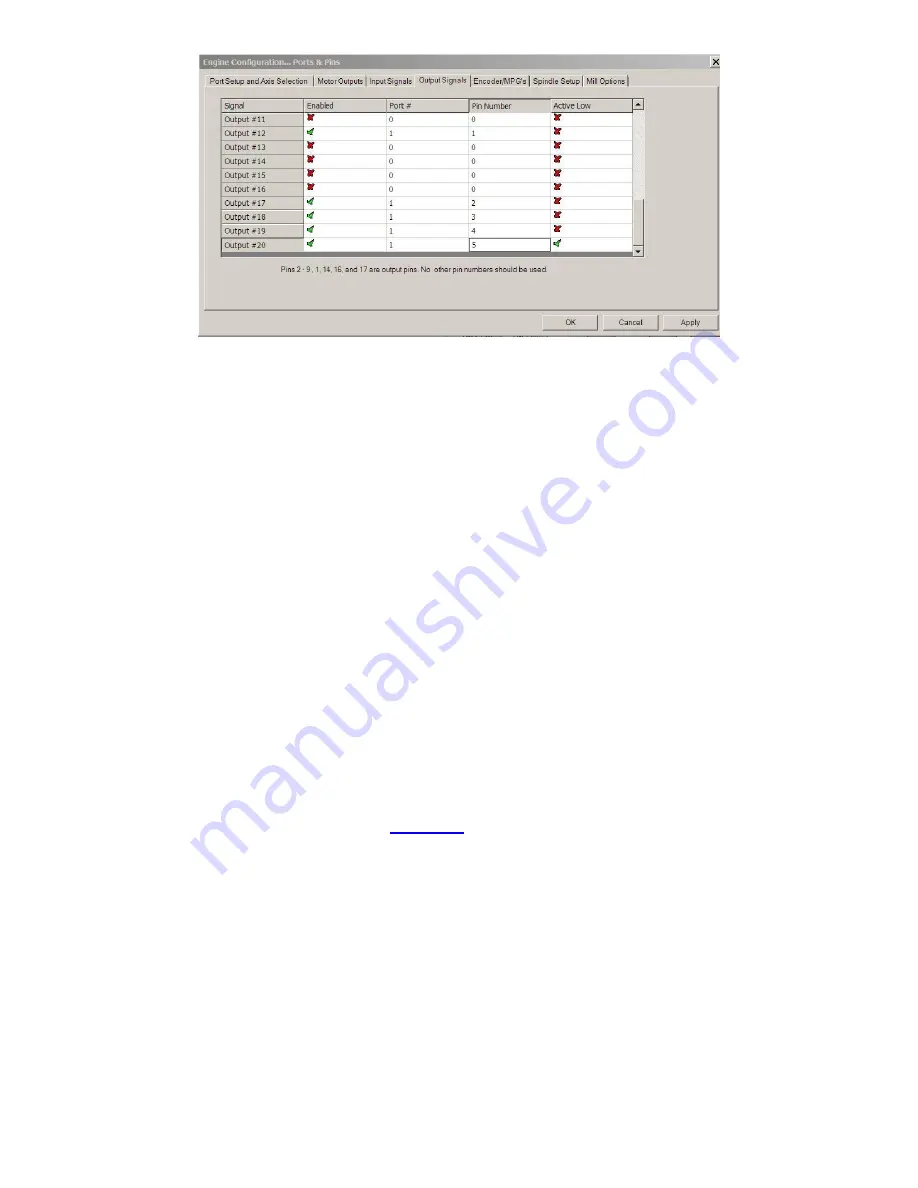
16
A major difference betwe
en the mill spindle and the InTurn™ spindle is that the InTurn™ has a heavy
spindle with a heavy mounting flange and can have an even heavier chuck or faceplate and heavier
yet workpiece.
This mass takes time to accelerate from a dead stop and MACH has no mechanism to account for
this. The result can be a cutting tool advancing into the workpiece far ahead of the workpiece
reaching its target speed. This is most prevalent in running G-
code where the InTurn™ spindle is
being switched on and off via embedded macros. The consequence of a timing error like this is
generally not good.
The InTurn™ Motor Control System is specifically designed for the features and needs of the unique
Mill/Turn capabilities the InTurn™ brings with it. The controller’s spindle control macros work with the
Controller which in turn controls MACH in order to coordinate the movement of the cutting tools with
the spindle readiness.
This feature is accomplished by the controller preventing MACH from moving any axis until the
InTurn™ spindle has reached the commanded speed. The communication with MACH requires an
‘INPUT’, but the previous hard wire connection for this signal has been moved to the ModBus, so all
that is needed is configuring the input a certain way and the rest is handled by the Controller.
MACH has a typ
e of signal that is termed ‘
emulated
’ and this must be selected for the INPUT being
discussed or it will not function.
In the ‘Ports & Pins’ configuration panel:
*click to activate INPUT4
*leave the pin numbers at zero.
*click
the ‘emulated’ column
*make sure you click on the ‘APPLY’ button before closing this window.