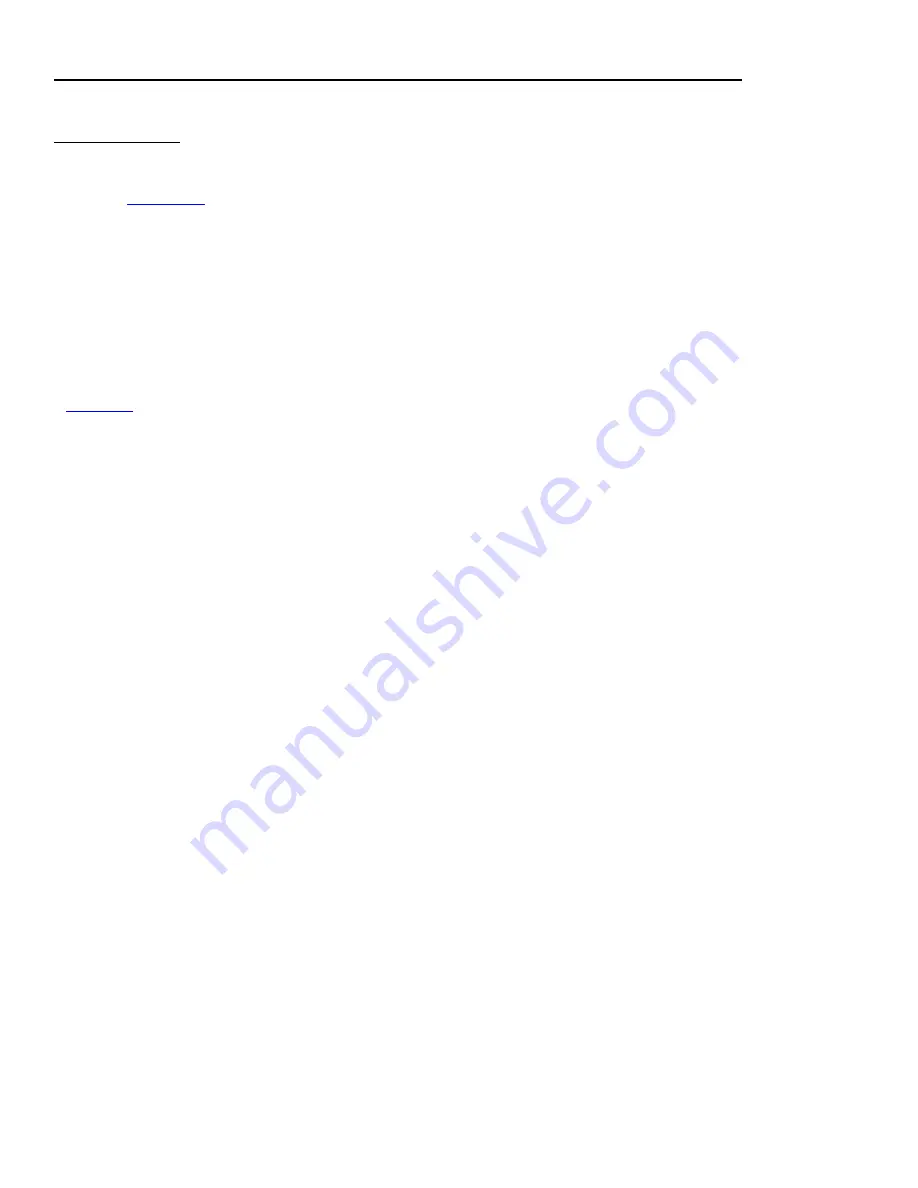
21
Adding your system Parameters into
the InTurn™ Controller
AutoConfigure
The Auto
Configure
feature is included in all Gen2 controllers and is available as a firmware only
upgrade for Gen1 controllers.
The InTurn™ Motor Control, system does internal calculations to set and maintain commanded
speed. The formulas are based on parameters that vary from machine to machine.
The parameters are
* Maximum motor RPM
–
this is the motor itself and not the 4
th
axis spindle.
*
Encoder
resolution.
This need to be in ‘counts’ or ‘steps’ and not ‘lines’
Encoders typically operate in quadrature so the count is 4x the lines.
* Main Drive Ratio
–
this is the belt ration without double reduction (back gear).
* Back Gear Ratio
–
borrowing the term from lathes, ‘Back Gear is the extra
reduction afforded by additional gearing in ‘back’ of the head. For
the 4
th
axis, this is the extra belt and idler setup. If your 4
th
axis does
not have the double reduction setup, enter the Main ration again here.
*Drive Multiplier
–
many drives have step multipliers or ‘electronic gearing’.
If you are using this feature, enter the amount of multiplication. If your Drive has single digit
multipliers, e.g., 2,3,6,10, etc., then simply enter that number. If your drive has separate numerator
and denominator, enter the decimal equivalent of the fraction, e.g., for a numerator of 1250, and a
denominator of 456, you would enter the equivalent of 1250/456 or 2.741.
Providing all parameters to the controller is now very easy and is done on the MACH screen.
Parameters that might be changed frequently have dedicated screen buttons. The screen button
labelled ‘Acceleration Settings’ brings up a screen that collects Accel strings and also has a checkbox
that will take you to the main Parameter input screen.