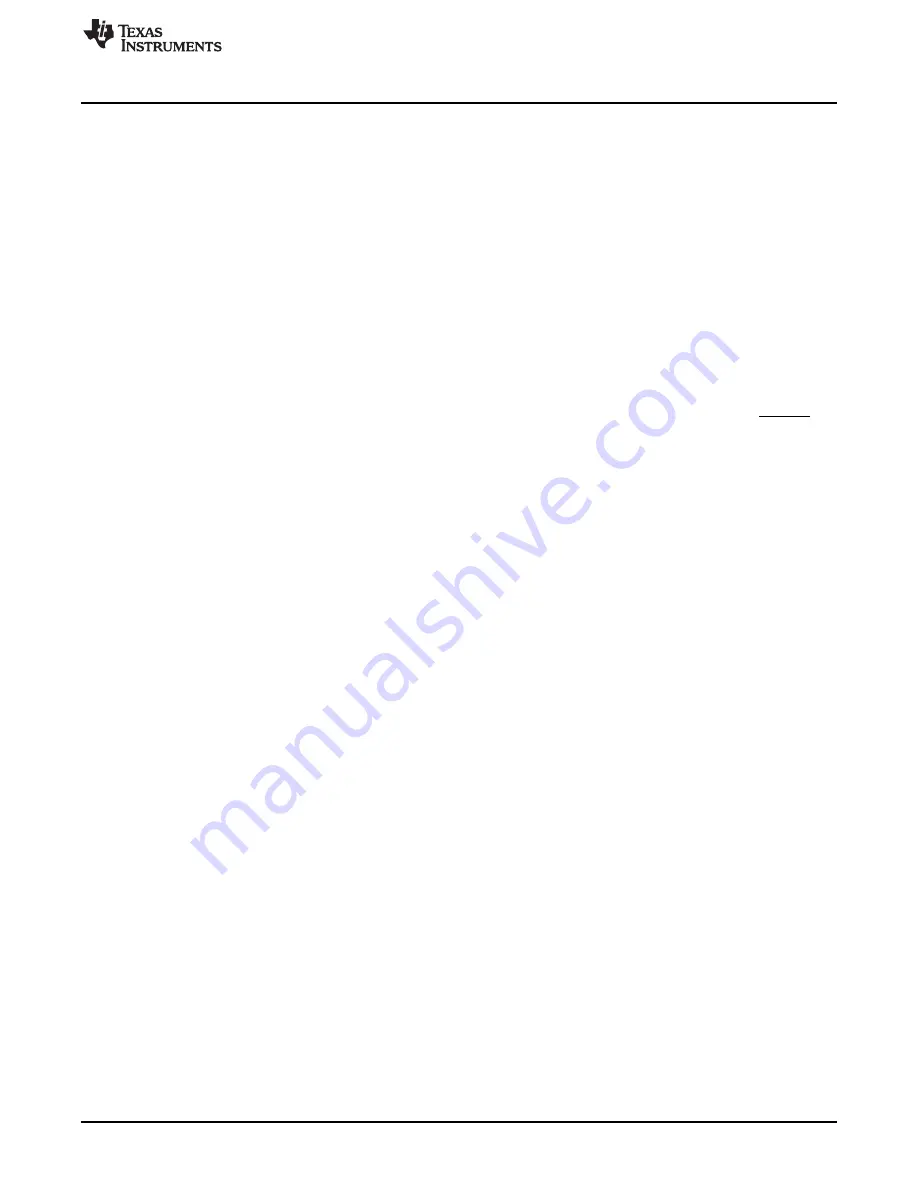
Getting Started
Design inputs are keyed in on the left side following steps 1 though 5.
1. Enter the general operating conditions in step 1 of the design tool. These inputs help set bounds on
the startup time and application voltage ranges.
2. Step 2 allows the user to tailor the MOSFET protection features to be specific to the target application.
Current limit is pin-configurable and software-configurable, and circuit breaker is software-configurable.
If the CL switch is used to set the current limit, ensure the GUI selection matches the pin-configurable
CL bit setting on the board. By clicking on the MOSFET SOA Profile button, the user can select SOA
data from several popular MOSFETs or enter the SOA data for the desired MOSFET. The resistor
R
PWR
can then be calculated to keep Q
1
or Q
3
, or both, within its SOA profile.
3. Step 3 allows the user to select the undervoltage lockout (UVLO) and overvoltage lockout (OVLO)
values, and power good (PGD) thresholds. Note that with the correct values for R8, R9, R13, R14, and
R3 and R7 installed, the LM5066I indicates a fault condition when the input or output voltages, or both,
are outside of their programmed range.
4. Step 4 allows the user to set the fault time-out period and the fault response. The fault time-out should
be set to be below the MOSFET SOA data for a given time. For example, if a design is done to adhere
to the 10 ms pulsed MOSFET SOA data, the desired fault time-out must be less than 10 ms. The fault
time-out time entered sets the value for C
T
. It also sets the insertion delay and fault retry delay. The
initial power-up retry behavior is also selected in this design step. Make sure to change the RETRY
switch to match the design tool schematic when changing the default retry setting.
5. In step 5, the user enters the desired PMBus address. Note changing the PMBus address of the
device in step 5 does not change the device address, but shows how the address pins of the device
need to be configured to achieve a desired address. After the ADR pin switches are configured for a
particular address, power to the device needs to be cycled and the GUI restarted in order for the new
address to take effect.
When invalid or incorrect inputs are given to the design tool, text associated with the faulty input turns red.
Positioning the mouse cursor over the red text gives additional information about any design conflict.
Component and parametric results are shown to the right as well as the LM5066I safe operational area
(SOA) chart. The SOA chart shows the minimum, typical, and maximum SOA protection areas for a given
design. For a robust design, the SOA of the MOSFET used should be above the max protection SOA line
for all operating areas.
After a design is complete, the design should be saved by selecting the File menu, then Save. After the
hardware is modified to match the design, the GUI should be restarted and the hardware configuration file
loaded right after the device is detected and placed. If the values in the design tool are different than the
values on the board, erroneous telemetry and fault data are reported by the GUI. To return to the block
view of the device, press the Home button located at the far left in the menu bar.
The design tool is also useful to calculate the PMBus coefficients. With the correct value for current sense
resistor (R2), the tool calculates the correct coefficients to scale the raw telemetry data. The coefficients
can be viewed by selecting View from the main menu bar, and then selecting the PMBus Coefficient
Editor. When the PMBus Coefficient Editor is opened, press the Get All button to show the currently used
coefficients.
If desired, the results presented by the design tool can be calculated by hand using the equations
provided in the data sheet. However, note the design tool calculates parameters factoring in worst-case
tolerances, while the equations in the data sheet are based on typical thresholds.
17
SNVU444 – May 2014
LM5066IEVM-626 Evaluation Module (EVM)
Copyright © 2014, Texas Instruments Incorporated