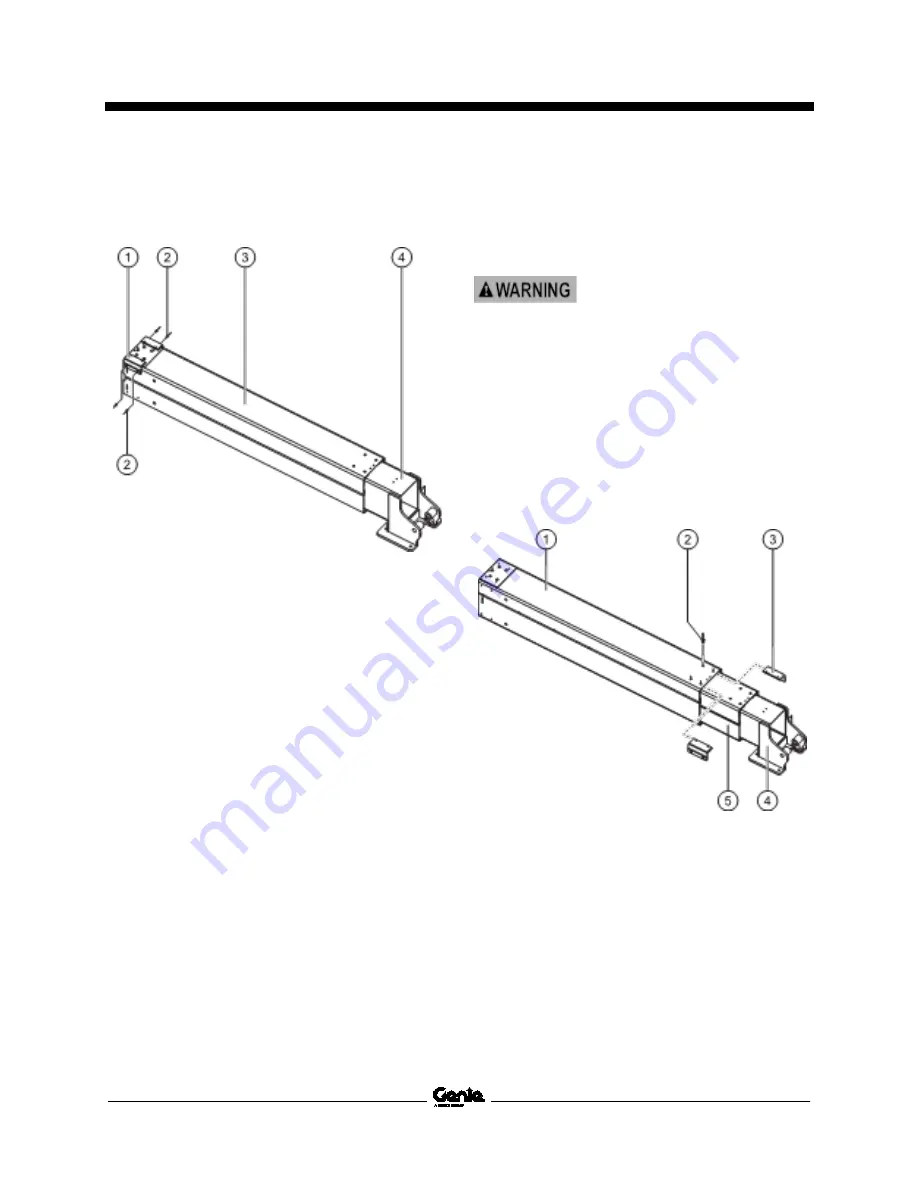
Service Manual
February 2022
Mast Components
66
GRC
™
Part No. 1314708GT
11 Using the appropriate rivets, install the upper
corner wear pads, to the upper half of the
number 2 mast.
Illustration 4
1 wear pads
2 rivet
3 mast number 2
4 mast number 1
12 Attach a lifting strap from an overhead
supporting device to the number 3 mast and
carefully slide the number 3 mast onto the
number 2 mast, with the cylinder mount
brackets facing the work table.
Crushing hazard. The mast
section could become
unbalanced and fall if not
properly supported.
Note: During installation, the lifting strap will need
to be adjusted for proper balancing.
13 Slide the lower, inner corner wear pads
between the number 3 mast and the number
2 mast. Align the holes on the wear pads to
the rivet holes on the lower half of the number
3 mast and secure into place using the
appropriate rivets.
Illustration 5
1 mast number 3
2 rivet
3 wear pads
4 mast number 1
5 mast number 2
Содержание Genie GRC-12
Страница 110: ...Service Manual February 2022 Wiring Diagram Ground and Platform Controls 98 GRC Part No 1314708GT...
Страница 113: ...February 2022 Service Manual 101 Electrical Schematic GRC Options...
Страница 115: ...February 2022 Service Manual 103 Electrical Schematic GRC from GRC11 1000 to GRC11 1078...
Страница 118: ...Service Manual February 2022 106 Electrical Schematic GRC from GRC11 1000 to GRC11 1078...
Страница 119: ...February 2022 Service Manual 107 Electrical Schematic GRC from GRC11 1079 to GRC14 1780...
Страница 122: ...Service Manual February 2022 110 Electrical Schematic GRC from GRC11 1079 to GRC14 1780...
Страница 123: ...February 2022 Service Manual 111 Electrical Schematic GRC from GRC14 1781 to GRC15 2343...
Страница 126: ...Service Manual February 2022 114 Electrical Schematic GRC from GRC15 2344 to GRC16P 2481...
Страница 127: ...February 2022 Service Manual 115 Electrical Schematic GRC from GRC16P 2482 to GRC16P 2562...
Страница 130: ...Service Manual February 2022 118 Electrical Schematic GRC from GRC16P 2563 to GRCP 5999...
Страница 131: ...February 2022 Service Manual 119 Hydraulic Schematic GRC from GRC11 1000 to GRC12 1168...
Страница 135: ......