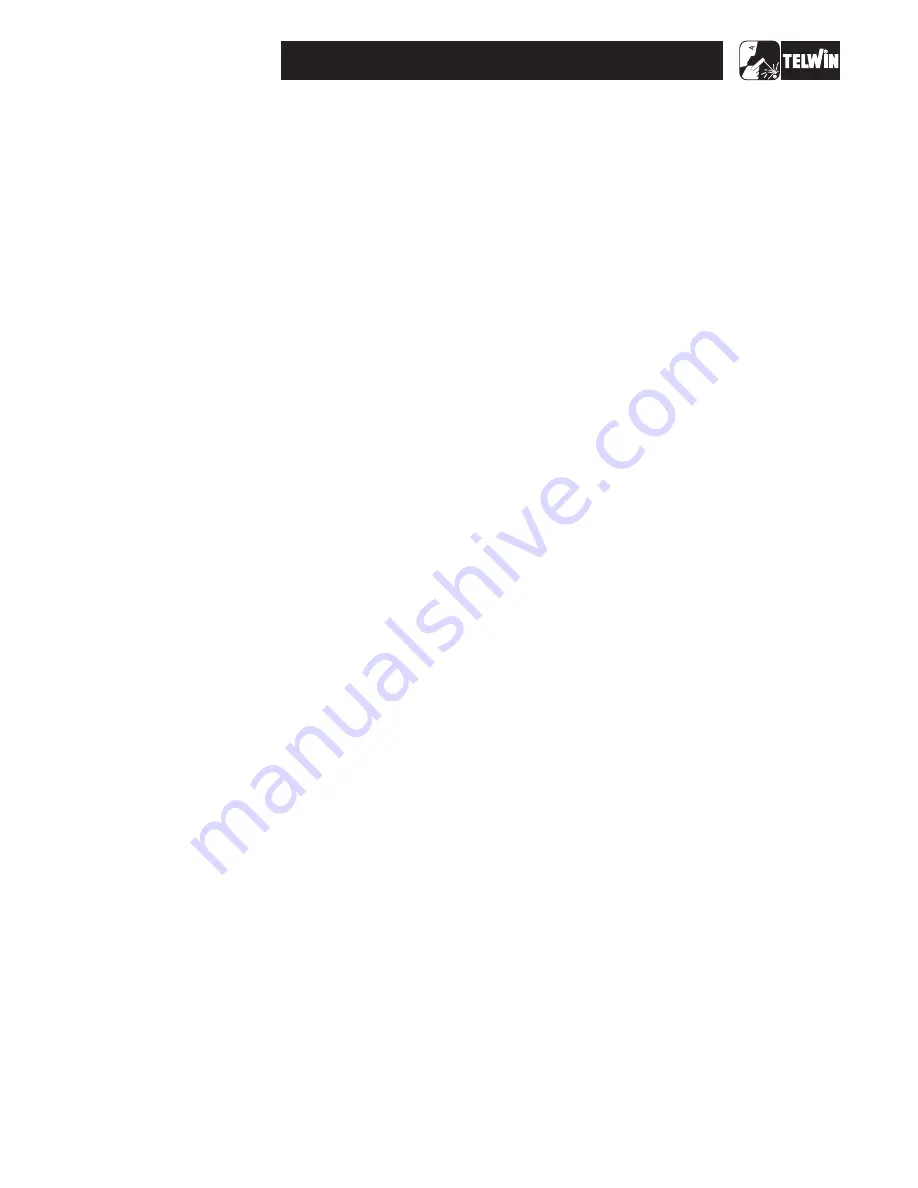
- 3 -
ANALYSIS OF THE BLOCK DIAGRAM
Block 1
Block 2
Block 3
Block 4
Block 5
Block 6
Block 7
Block 8
NOTE: Unless indicated otherwise, it should be assumed that
the components are assembled on the primary board.
Consisting of: C1, L1, C5, C6.
Prevents noise from the machine from being transmitted along
the main power line and vice versa.
Consisting of: K1, R1.
Prevents the formation of high transitory currents that could
damage the main power switch, the rectifier bridge and the
electrolytic capacitors.
When the power source is switched on the relay K1 is de-
energised, capacitors C2, C3, C4 are then charged by R1.
When the capacitors are charged the relay is energised.
Consisting of: D1.
Converts the mains alternating voltage into continuous pulsed
voltage.
Consisting of: C2, C3, C4.
Converts the pulsed voltage from the rectifier bridge into
continuous voltage.
Consisting of: Q1, Q2.
Converts the continuous voltage from the filter into a high
frequency square wave capable of piloting the power
transformer.
Regulates the power according to the required welding
current/voltage.
Consisting of:T2.
The C.T. is used to measure the current circulating in the power
transformer primary and transmit the information to block 14
(primary current reader and limiter).
Consisting of:T3.
Adjusts the voltage and current to values required for the
welding procedure. Also forms galvanic separation of the
primary from the secondary (welding circuit from the power
supply line).
Consisting of: D36, D37, D38 .
D36 converts the current circulating in the transformer to a
single direction, preventing saturation of the nucleus.
D37, D38 recirculate the inductance output current (block 9)
when the IGBT's are not conducting, bypassing the power
transformer (block 7).
EMC Filter
Pre-charge
Rectifier bridge
Filter
Chopper
Current transformer
Power transformer
Secondary diodes
Block 9
Block 10
Block 11
Block 12
Block 13
Block 14
Block 15
Block 16
Block 17
Inductance
Secondary EMC Filter
Flyback power supply
Driver
Primary current reader and limiter
Duty cycle maker
Adder
Alarm Block
Alarm LED
Consisting of: L2.
Levels the secondary board diodes’ output current making it
practically continuous.
Consisting of: C50, C51.
Prevents noise from the power source from being transmitted
through the welding cables and vice versa.
Consisting of:T1, U2.
Uses switching methods to transform and stabilise the voltage
obtained from block 4 (filter) and supplies auxiliary voltage to
power block 12 (driver) and the control board correctly.
Consisting of: ISO2, ISO3.
Takes the signal from block 11 (flyback power supply) and,
controlled by block 14 (duty cycle maker), makes the signal
suitable for piloting block 6 (chopper).
Consisting of: R37, R38 and part of the control section.
Reads the signal from block 6 (current transformer) and scales
it down so it can be processed and compared in blocks 14 and
15.
Consisting of: U2 (control board).
Processes the information from block 15 (adder) and block 13
(primary current reader and limiter) and produces a square
wave with variable duty cycle limiting the primary current to a
maximum pre-set value under all circumstances.
Consisting of: U1C, U1D (control board).
Gathers all the information from block 13 (primary current
reader and limiter), from block 16 (alarms) and from block 18
(current potentiometer), and produces a signal with a suitable
voltage for processing by block 14 (duty cycle maker).
Consisting of: U1A, U1B (control board).
When an alarm is detected the power source output current is
drastically reduced by making direct adjustments to block 14
(duty cycle maker) and directly changing the reference signal
obtained from block 18 (current potentiometer).
Consisting of: D26.
It is switched on by block 16 (alarms) in the event of:
1) Triggering of thermostatic capsule/thermostat on power
transformer.
2) Triggering of thermostatic capsule/thermostat on IGBT
dissipator.
3) Triggering due to undervoltage.
4) Triggering due to overvoltage.
TECNICA PLASMA 18 - 31