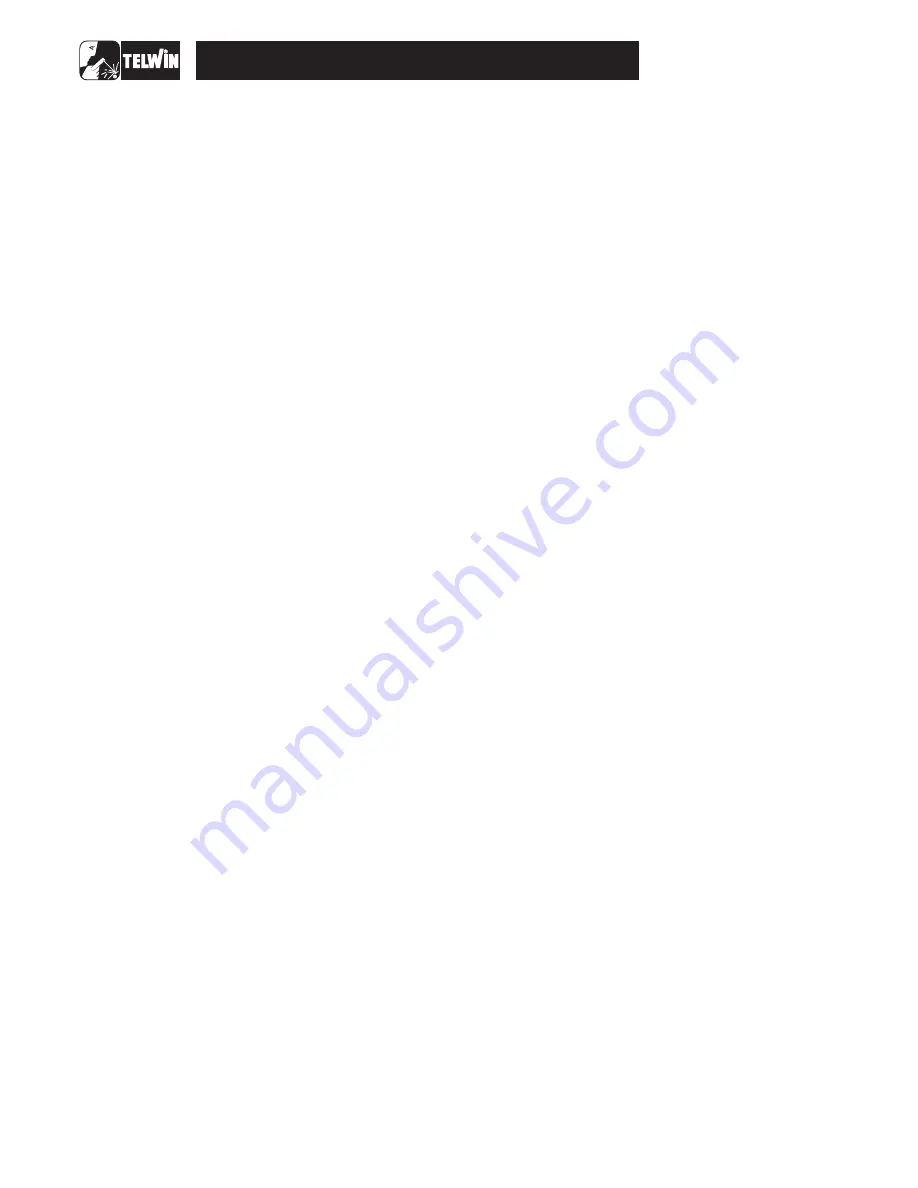
IGBT's Q1, Q2 fig. 4
Primary diodes D14, D20 fig. 4
Secondary diodes D36, D37, D38 fig. 4
Power transformer and filter reactance (fig. 2A)
6.1 Preparation for testing
6.2 Tests for the TECNICA PLASMA 31
(
)
.
(
)
(
)
Probable cause:
-
discontinuation in snubber network,
-
fault in driver circuit
-
poorly functioning thermal contact between IGBT and
dissipator (e.g. loosened attachment screws: check),
-
excessive overheating related to faulty operation
Probable cause:
-
excessive overheating related to faulty operation.
Probable cause:
-
discontinuation in snubber network;
-
poorly functioning thermal contact between IGBT and
dissipator (e.g. loosened attachment screws: check);
-
faulty output connection.
It is important to check that all the connections are in good
condition and the connectors are inserted and/or attached
correctly. To do this, take the cables between finger and
thumb (as close as possible to the fastons or connectors) and
pull outwards gently: the cables should not come away from
the fastons or connectors. N.B. If the power cables are not
tight enough this could cause dangerous overheating.
In particular, on the
(
) it is necessary to
check the power wiring:
-
the connection of the power supply cable to the fastons at
the main switch and to the earth faston (J3) on the power
board;
-
the connections from the power board to the main switch
(J1, J2);
-
the connections to the solenoid valve (J6, J7);
-
the connections from the torch button to the power board
(J13, J14);
-
the connection from the torch (pilot arc) to the power board
(J11);
-
the connections of the thermostat to the power
transformer (ST2);
-
the fan connections (V1+, V1-).
Make sure the earth cable (out+) and torch connection (out-)
are fastened to the power board correctly (
).
A) With the multimeter set in
mode check the
following components (junction voltages not less than 0.2V):
-
rectifier bridge D1 (
);
-
IGBT's Q1, Q2 (absence of short circuits between
collector-gate and between emitter-collector
);
-
secondary board diodes D36, D37, D38 between anode
and cathode (
). The secondary diodes can be
checked without removing the power board: with one prod
on the secondary board dissipator diodes and the other in
sequence on the two power transformer outlets;
-
viper U2 (absence of short circuits between pin 3 - pin 4
and between pin 4 pin 2,
)
B) With the multimeter set in ohm mode check the following
components:
-
resistor R1: 47ohm (pre-charge
).
-
resistors R21,R27: 22ohm (primary snubber
).
-
resistor R45: 10ohm (secondary snubber
).
-
IGBT thermostat continuity test: clean the resin from the
bump contacts of ST1 and measure the resistance
between the two bump contacts, it should be approx. 0
ohm (
);
-
thermostat continuity test on the power transformer: clean
the resin from the bump contacts of ST2 and measure the
resistance between the two bump contacts, it should be
approx. 0 ohm (
).
Before proceeding with faultfinding, we should
remind you that during these tests the power source is
powered and therefore the operator is exposed to the danger
of electric shock.
The tests described below can be used to check the operation
of the power and control parts of the power source.
A) Do not connect the compressed air supply to the power
source.
B) Set up the oscilloscope with voltage probe x100
connected between the case of U2 (probe) and connector J9
(earth) near ISO1 on the power board (fig. 3).
C) Set up the multimeter in DC mode and connect the prods
to the OUT+ and OUT- bump contacts.
D) Position the potentiometer R42 on maximum (turn
clockwise as far as it will go).
E) Connect the power supply cable to a single-phase variac
with variable output 0-300 Vac.
During tests the operator must avoid contact with
the metal parts of the torch because of the presence of
dangerous, high voltage.
A) Switch on the variac (initially set to the value 0 V), switch
off the main switch on the power source and increase the
variac voltage gradually to 230 Vac and make sure:
-
the green power supply LED D2 lights up (
);
-
the fan for the power transformer starts up correctly;
-
the pre-charge relay K1 commutes (
);
-
for voltages close to the rated power supply value (230Vac
±15%) the power source is not in alarm status (yellow LED
D26 off).
if the power source stays in alarm status
permanently, there could be a fault in the plasma control
board (in any case, proceed to make the other tests)
B) Make sure that, when the torch button is pressed, relay K2
and the solenoid valve commute. If not use the multimeter in
Acvolt mode to check the voltage over fastons J6 and J7,
which should be 230Vac. If the voltage is correct then the
solenoid valve is faulty. If the voltage is zero or is not 230Vac,
check the performance of relay K2. Alternatively, replace the
plasma control board.
Make sure that when the torch button is pressed the
waveform displayed on the oscilloscope resembles
.
all the suggested loadless tests, with the torch button
pressed, should not last longer than 8 seconds each. If
necessary press and release the torch button more than
once.
4.0 Checking the power and signal wiring
5.0 Electrical measurements with the machine
switched off
6.0 Electrical measurements with the machine
in operation
power board fig. 2A
Other checks:
fig. 2B
diode testing
fig. 3
fig. 4
fig. 4
fig. 3 .
fig. 3
fig. 3
fig. 3
fig. 2B
fig. 2B
WARNING!
WARNING!
fig. 3
fig. 3
N.B.
C)
fig. A
N.B.
- 12 -
TECNICA PLASMA 18 - 31