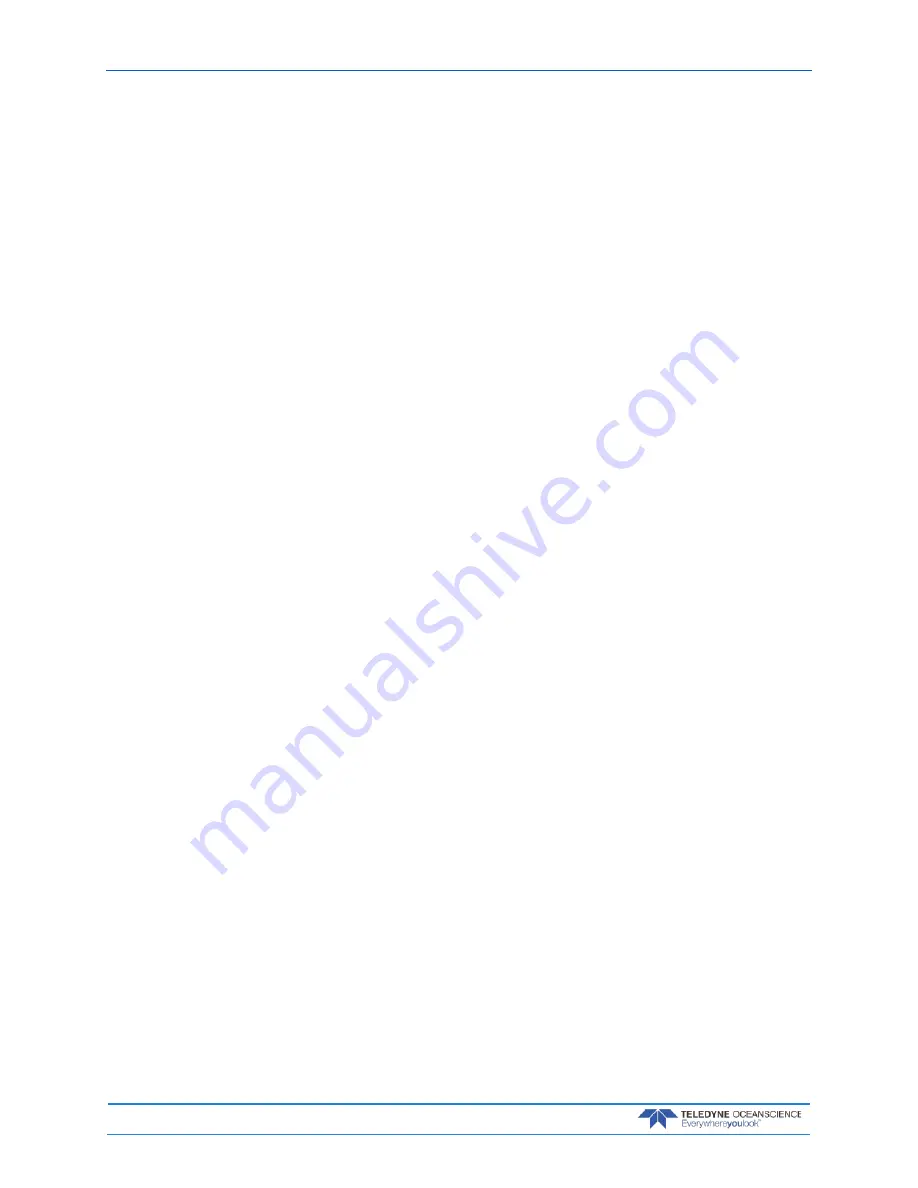
March 2018
rapidCAST User’s Guide
Page
68
EAR-Controlled Technology Subject to Restrictions Contained on the Cover Page.
P R O B L E M
: The Spool Encoder is malfunctioning.
I N D I C A T I O N S
: Any of the following may indicate a problem with the spool encoder:
•
Erratic spool motion during tension-controlled payout or when moving between points. Erratic
motion may include instantaneous unexpected speed changes or brief stoppages.
•
Inconsistent or non-existent position count feedback. Feedback on the winch’s current position
may freeze or skip counts during motion.
•
Inability of the winch to maintain a reasonably constant speed for extended periods, despite being
commanded to do so.
D E S C R I P T I O N
: Feedback on the spool’s position and speed is provided by an incremental optical
encoder with a resolution of 10,000 counts per spool revolution. By virtue of its extremely high resolution,
the spool encoder is a precision sensor whose performance can be degraded by moisture ingress, foreign
contaminants, mechanical misalignment, or extreme shocks or vibration. In addition to mechanical dis-
turbances, sensor feedback from the encoder can also be corrupted by electrical noise when high levels of
electromagnetic interference are present. The spool encoder is a critical component of the motion control
system, and degradation in its performance will interfere with the ability to control the spool’s motion re-
liably and predictably.
R E M E D I E S
:
1. If the probe is in the water, retrieve the probe and stow it on the vessel. Once the probe has been
stowed, on the Control Module turn the Motor Driver Switch OFF. Verify that the Activity LED
becomes dim, which confirms that the motor driver has been successfully deactivated. Turn the
Brake Switch to Release. Move the Control Source Toggle Switch to Local Control.
Detach the line from the probe. Secure all line onto the spool, and use adhesive tape or other fas-
tener to fix the end of the line to the spool so that the line cannot snag any objects. The goal is to
allow the spool to rotate freely.
2. Confirm that the spool encoder is indeed malfunctioning. Other sources of erratic motion may be
mechanical in nature such as loose couplers or mechanical obstructions. To rule out mechanical
sources of error, rotate the spool by hand and feel for any mechanical grittiness, looseness, or ob-
structions. If manual rotation of the spool feels smooth, this clears the mechanical system and
makes the spool encoder suspect. Set the Control Source Toggle Switch to PC Control and set all
power switches to their normal (up) positions at the end of this test in order to use the Interface
Software.
3. As additional confirmation that the spool encoder may be damaged, use the Interface Software to
command the spool to rotate without relying on feedback from the encoder. To deactivate the en-
coder, in the Interface Software Maintenance tab, click the Open Loop button and confirm that
the Mode setting on the dashboard indicates OpenLoop. This step deactivates feedback from the
encoder.
Afterward, in the Winch Config tab, locate the OpenLoopVelocityScaled setting. Entering a value
here will command the spool to rotate without encoder feedback. A positive value will cause the
spool to rotate out. A negative value will cause the spool to rotate in. A value of 0 will stop the
spool. The values do not correspond to RPM but correspond to percentages. For example: a value
of 1000 (interpreted as 100.0%) will make the spool rotate out at its maximum speed; a value of -
1000 (interpreted as -100.0%) will make it rotate in at maximum speed; a value of -637 will make
the spool rotate in at 63.7% of its maximum speed; and a value of 50 will make it rotate out at
5.0% of its maximum speed.
Test and observe spool motion for different values of OpenLoopVelocityScaled. If spool motion is
smooth and predictable when the encoder has been deactivated, this confirms that the spool en-
coder is at fault.
4. Damage to the Spool Encoder is terminal. It must be replaced before the winch can be safely oper-
ated.