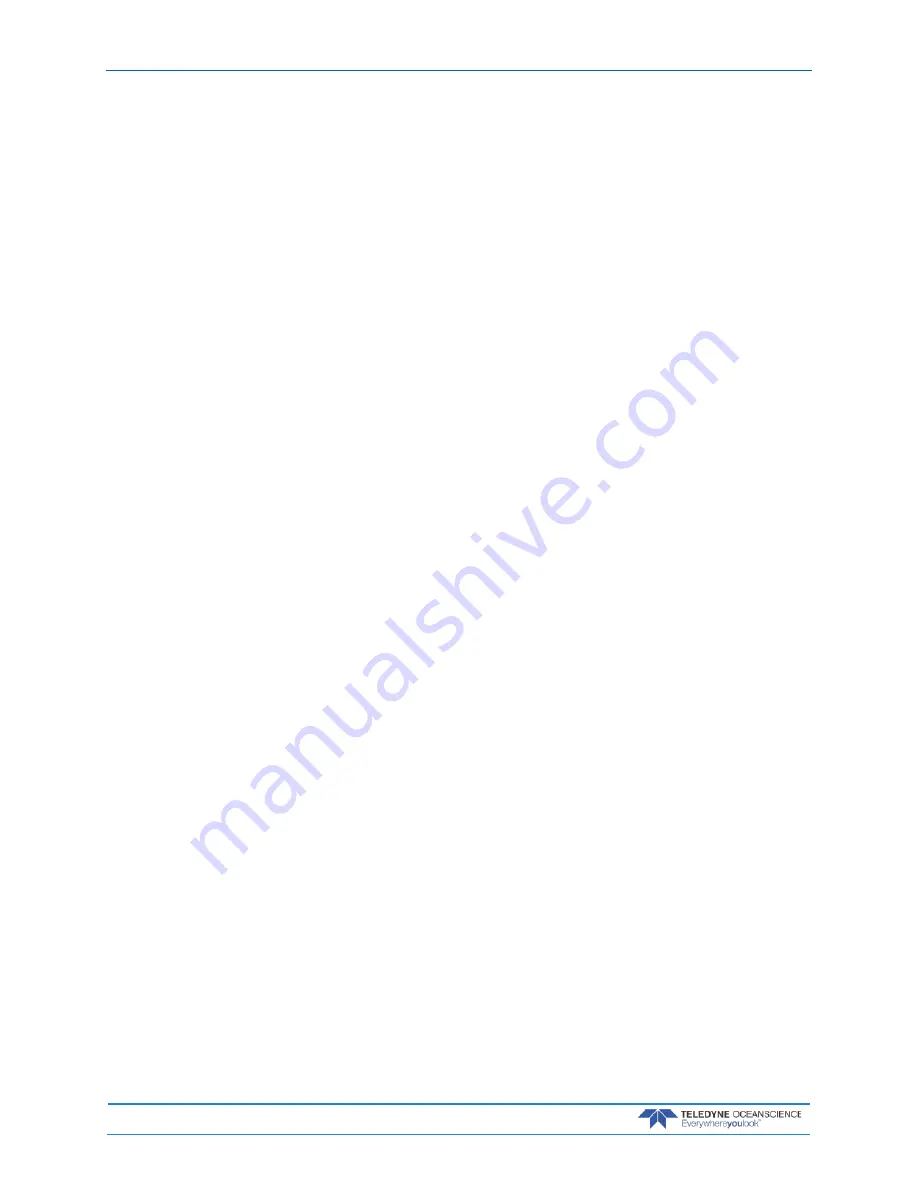
March 2018
rapidCAST User’s Guide
Page
64
EAR-Controlled Technology Subject to Restrictions Contained on the Cover Page.
P R O B L E M
: The Motor Brake is not releasing the spool when commanded to.
I N D I C A T I O N S
: One or more of the following conditions may indicate a brake failure to release:
•
Unpleasant grinding noise when the spool is rotating.
•
The spool appears to be struggling or shaking when rotating.
•
The Interface Software reports unusually high current levels when attempting to move the spool.
•
The Interface Software reports wide speed fluctuations when attempting to move the spool.
D E S C R I P T I O N
: The spool is stopped by an electromagnetically-actuated brake, which functions
like a solenoid. When the brake is unpowered, a spring clamps the brake shut, preventing rotation of the
motor shaft. This ensures that in the event of a power loss, the spool will be stopped and the probe will be
retained. Applying 24V DC power to the brake will energize an electromagnet that separates the brake
pads, which will release the motor shaft and allow it to rotate freely. A solid-state relay inside the Control
Module determines whether 24V DC is applied to the brake.
Failure of the brake to release is indicative of an electrical fault, since it requires electrical energy in order
to generate an electromagnetic force which releases the brake pads. Prime candidates include a malfunc-
tion of the brake relay and its inability to conduct current when needed, or a failure of the brake power
supply.
You may toggle the brake state to test its functionality:
On the Control Module, set the Toggle Switch to Local Control
Set the Brake Switch to Release and back to Brake, repeating this as many times as desired.
You should hear clicks coming from the motor housing, indicating that the brake is engaging and
releasing based on the switch position.
Remember to return the Brake Switch to Brake and the Toggle Switch to PC Control if you
want to use the Interface Software.
R E M E D I E S
:
On the Control Module, verify that the MAIN 24V LED is lit. If this LED is not lit, this indicates
that the power supply for the brake has failed or is not supplying power. Using a Multimeter, ver-
ify the output of the power supply is 24VDC. If there is 24VDC output, then inspect all of the wir-
ing in and out of the power supply. If the power supply has failed, this is a terminal condition. The
brake cannot operate until this power supply is replaced.
Disconnect the Motor Power Cable and inspect the connector for possible damage to the pins and
conductors. Ensure that this cable is properly seated when connected.
If the brake relay is suspected, you may activate the backup brake relay. In the Winch Config tab,
set the UseBackupBrakeRelay variable to True. This will bypass the original suspect relay. Please
note that this setting is not retained if the Interface Software is closed. If you Save Workspace
while this variable has the desired value, and later Load Workspace, the variable will be set when
loading the stored workspace.
If the brake cannot be released despite the above remedies, and the probe is still in the water, fol-
lowing the steps in the next section to remove the brake. Once the brake is removed, recovery us-
ing the motor should be possible.