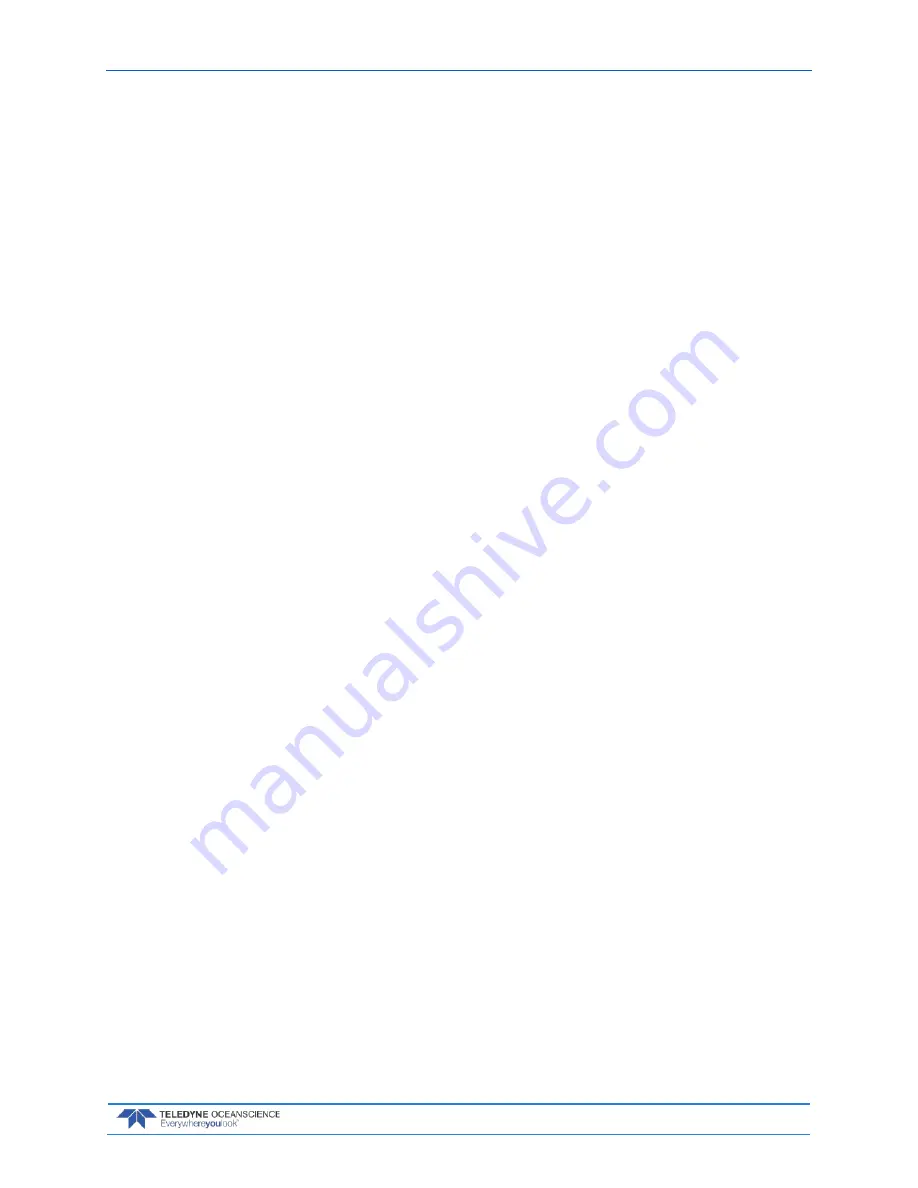
rapidCAST User’s Guide
March 2018
EAR-Controlled Technology Subject to Restrictions Contained on the Cover Page.
Page
63
P R O B L E M
: The Motor Brake does not appear to be engaging/stopping the spool.
I N D I C A T I O N S
: If the Control Module detects that the spool has rotated 10 or more revolutions
even after the brake has been commanded to engage, the following fault will be reported by the Interface
Software:
“EXCESSIVE BRAKE SLIPPAGE DETECTED.”
The Control Module will activate the Buzzer and
Strobe for 30 seconds if this fault is encountered.
D E S C R I P T I O N
: The spool is stopped by an electromagnetically-actuated brake, which functions
like a solenoid. When the brake is unpowered, a spring clamps the brake shut, preventing rotation of the
motor shaft. This ensures that in the event of a power loss, the spool will be stopped and the probe will be
retained. Applying 24V DC power to the brake will energize an electromagnet that separates the brake
pads, which will release the motor shaft and allow it to rotate freely. A solid-state relay inside the Control
Module determines whether 24V DC is applied to the brake.
Corrective action depends on whether the brake slippage is due to a mechanical or electrical fault, with a
mechanical cause being more probable. Mechanical causes are varied and may include anything from a
loose brake/motor set-screw or loose fasteners/couplers anywhere along the drivetrain. An electrical
cause might be the solid state relay’s failure to cut power to the brake (because the relay may have failed
short, and thus continues to conduct power even when it shouldn’t).
When brake slippage is detected, the motor will actively stop the spool and prevent further rotation. The
motor will substitute for the brake, though this should only be treated as an emergency feature and should
not be relied on for normal operation.
R E M E D I E S
:
If the error is encountered while the probe is in the water,
stop the vessel immediately
to alleviate
the strain on the motor caused by drag. Excessive drag may cause the motor to fail due to over-
heating from high current, potentially leading to loss of the probe and damage to the winch.
Recover the probe and bring it on board.
Once the probe is safely stowed, turn the Main Power Switch OFF. Cutting power should cause
the brake to engage. Attempt to move the spool by hand. If the spool can be rotated, this indicates
that the root cause is most likely mechanical. If the spool cannot be rotated, an electrical cause
(faulty relay) is more probable. When attempting to move the spool by hand, apply a fair amount
of force, since the brake is designed to resist large loads. Partial slippage is an indication of a po-
tential mechanical fault.
If a mechanical cause is suspected, remove the winch covers, remove the motor cover, and per-
form a careful inspection of the drivetrain starting from the brake and continuing to the spool.
Tighten any loose couplers/fasteners along the drivetrain, paying particular attention to collars
and set-screws.
If the brake relay is suspected, you may activate the backup brake relay. A secondary relay was
included in the design. The original (suspect) relay must first be disconnected, since a shorted re-
lay will interfere with the operation of the backup relay. Open the Control Module and locate the
Processor Circuit Board. On this circuit board, disconnect the Brake Relay Out connector, which
is located just underneath the ribbon cable. Close the Control Module.
In the Interface Software’s Winch Config tab, set the UseBackupBrakeRelay variable to True.
This will bypass the original suspect relay. Please note that this setting is not retained if the Inter-
face Software is closed. If you Save Workspace while this variable has the desired value, and later
Load Workspace, the variable will be set when loading the stored workspace.
If the brake cannot be repaired yet completing the survey is paramount, the motor can take the
place of the brake as long as survey depths are restricted to 100 meters or less and survey ves-
sels speeds are restricted to 6 knots or less. In all cases, deploying the probe without a function-
ing brake increases the risk of probe loss, especially if the motor becomes damaged during de-
ployment and is unable to hold the probe. The importance of completing the survey versus the
value of the probe should be weighed carefully.