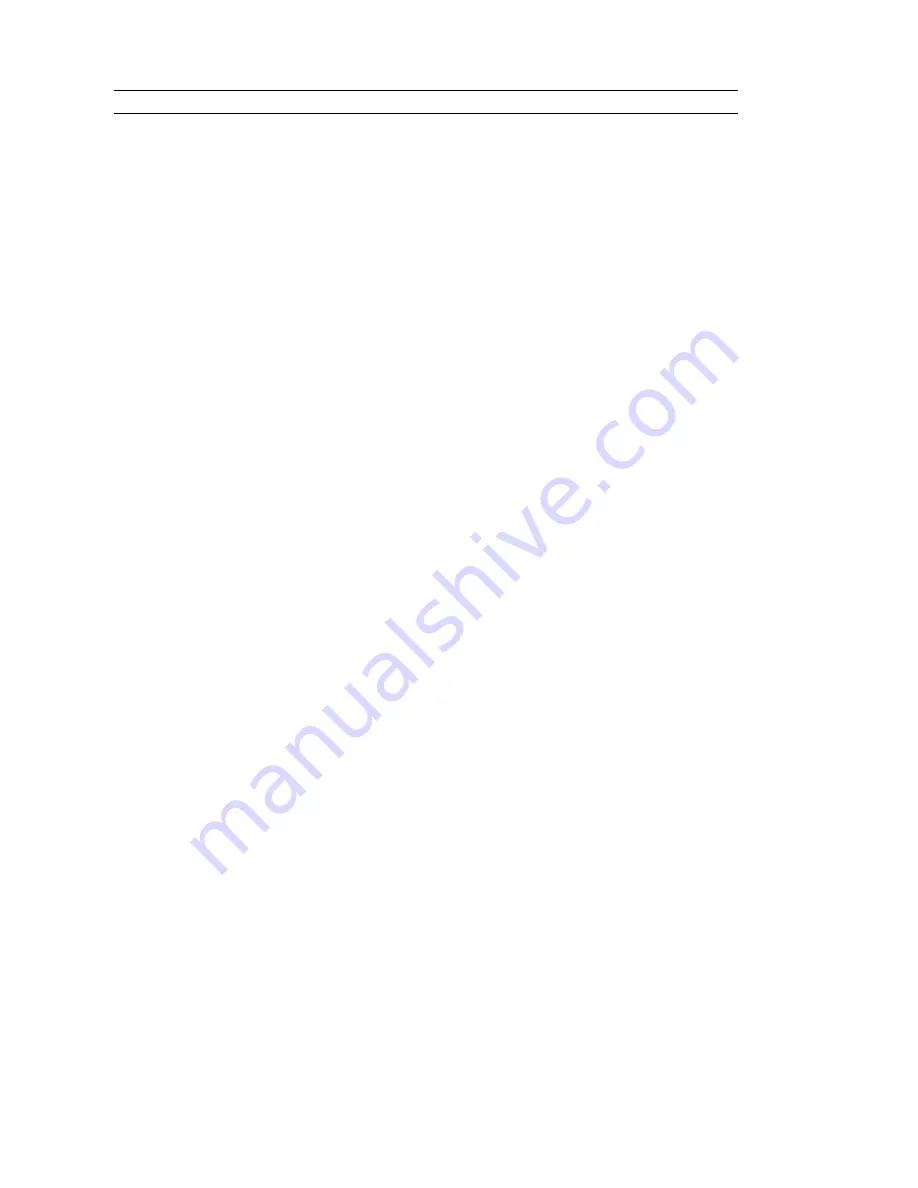
Troubleshooting Guide
Problem
Possible Cause and Solution
Excessive vibration.
Out of balance, or large work piece. Reduce lathe speed to the lowest
speed possible and turn the work piece to a true circle.
Work piece is not held in the center. Check work piece mounting and
correct.
Work piece is not secure or held tight enough. Check work piece
mounting and correct.
Lathe incorrectly bolted to stand or bench. Refer to this manual for
lathe stand recommendations.
Stand or bench not well constructed, too light, or standing incorrectly on
the floor. Make sure the stand is solidly constructed. Use sand bags to
weigh down the stand.
Over tensioning of belt is a primary cause of vibration. The drive belt is
running badly, over tensioned, or damaged. Apply a spray-on belt
dressing on the belt grooves, readjust belt tension, or replace the belt.
Motor pulley is not in correct alignment with the headstock pulley.
Loosen the motor pulley set screw and align the pulleys.
Headstock is loose. Tighten the Headstock Lockpin.
Headstock pulley or motor pulley is loose. Check that the pulley set
screws are tight.
The headstock guard is loose or rattling. Check that the guard screws
are tight.
Movement in motor mount plate. Check that the nyloc nuts on the
headstock studs are tight, and that the Teebar is tight.
Motor vibrates. Many single phase motors due to their design produce
minor noise or vibrations; these usually cannot be altered.
Faceplate or chuck
running out of true.
Dirt build up on the rear of the faceplates or chuck. Clean off all build
up and dirt. Faceplates and chucks must mount securely against the
inner bearing ring surface of the spindle.
Turning tools not
sliding smoothly
across Toolrest.
Damaged surface on toolrest face caused by sharp edged tools. File
the toolrest using a fine smooth file and polish with extra fine
sandpaper. Also remove the sharp edges from the corners of turning
tools.
Spur drive center or
live center not holding
into the spindle taper
or quill taper when
turning.
Small end of Morse taper is damaged due to dropping or hitting. File or
polish away any damage. Check that inside of tapers have not been
scored.
Grease or oil inside of Morse tapers. Wipe clean the inside of the
tapers.
Insufficient pressure when installing the center. Use a quick, firm action
by hand to install a taper. Do not knock in using any solid object.
L
Note: Can't find the answer in this Trouble Shooting guide?
Visit the Lathe Support Section on our website - this is packed with Frequently Asked Questions.
Or
Contact Us (details are at the front of this manual)
92-0106-017
23