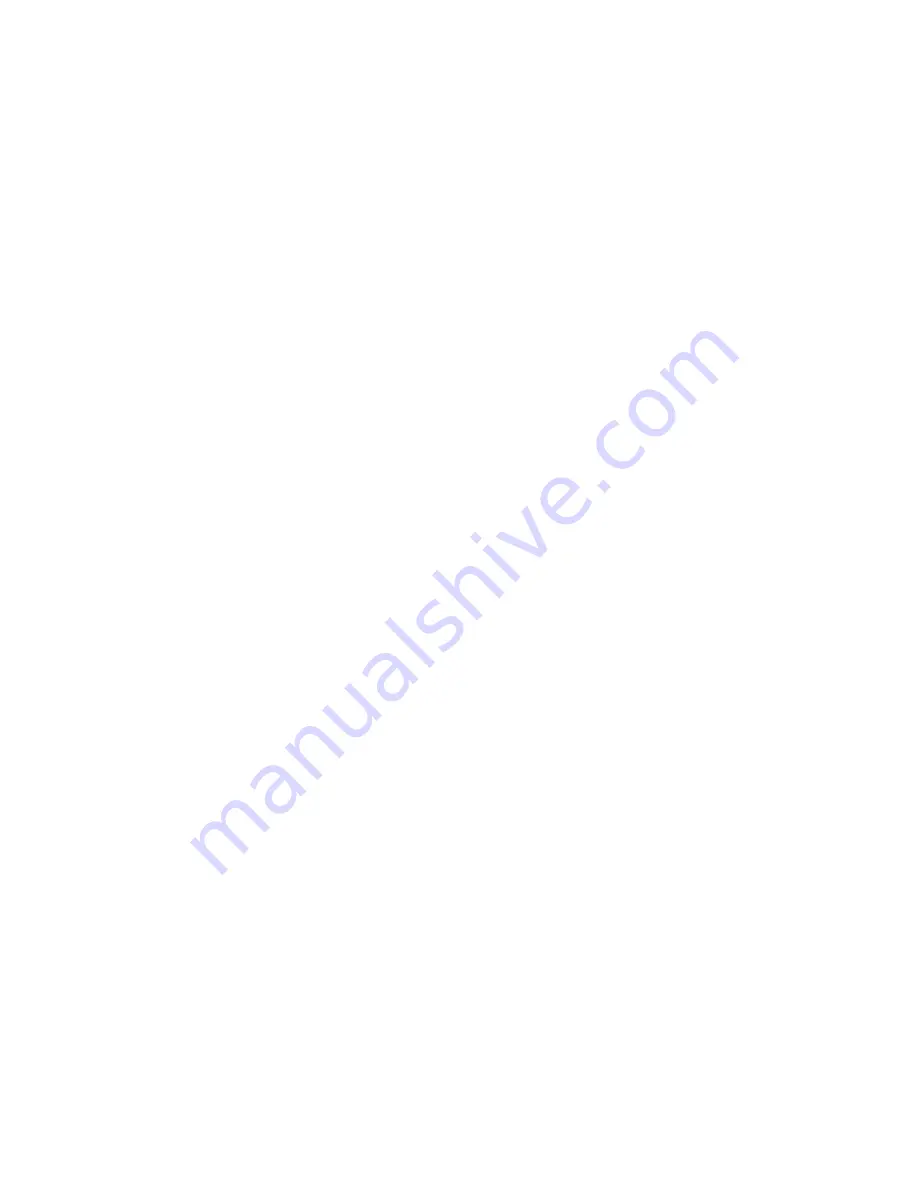
It is extremely important to design and size the suction
system to minimize pressure losses and to be sure
that the pump will not be “starved” for fluid during
operation. NPSH problems are a result of improper
suction systems.
If suction pipe length is short, pipe diameter can be
the same size as the pump suction port diameter. If
suction piping is long, the size should be one or two
sizes larger than pump suction port, depending on
piping length. Use the largest pipe size practical on
suction piping and keep piping short and free from
elbows, tees or other sources of pressure drop.
If elbows, tees or valves must be used, locate them
from 10 to 15 pipe diameters upstream from suc-
tion. When reducing to pump suction port diameter,
use eccentric reducers with eccentric side down to
avoid air pockets.
When operating under conditions where pump prime
can be lost during off cycles, a foot valve should be
provided in the suction line to avoid the necessity of
priming each time the pump is started. This valve
should be of the flapper type rather than the multiple
spring type and of ample size to avoid undue friction
loss in the suction line.
When foot valves are used, or when there are other
possibilities of fluid hammer, it is important to close
the discharge valve before shutting down the pump.
When it is necessary to connect two or more pumps
to the same suction line, provide gate valves so that
any pump can be isolated from the line. Install gate
valves with stems horizontal to avoid air pockets.
Globe valves should be avoided, particularly where
NPSH is critical.
If discharge pipe length is normal, pipe diameter
can be the same size as the pump discharge port
diameter. If discharge piping is of considerable
length, use larger diameter pipe (one or two sizes
larger).
If the pump is to discharge into a closed system or
an elevated tank, place a gate valve or check valve in
the discharge line close to the pump. The pump can
then be opened for inspection without fluid loss or
damage to the immediate area.
Page 5
2-2.3. Piping Data
Observe the standards of the Hydraulic Institute when
sizing and making up suction and discharge piping.
Follow these procedures:
1. Remove burrs and sharp edges when making
up joints.
2. When using flanged joints, be sure inside diam-
eters match properly. When gasketing flanged
joints, DO NOT cut flow hole smaller than flange
opening.
3. Use pipe hangers or supports at necessary in-
tervals.
4. Provide for pipe expansion when required by fluid
temperature.
5. When welding joints, avoid possibility of welding
shot entering the suction or discharge line, and
thereby entering the pump.
Do not weld pipe
while connected to pump.
6. When starting up a new system, it is recom-
mended to place a temporary 3/16" mesh screen
at or near suction port of pump to catch welding
shot, scale or other foreign matter. Refer to Sec-
tion 3-1, Page 9.
7. Do not spring piping when making up any con-
nections.
8. Make suction piping as straight as possible,
avoiding unnecessary elbows. Where necessary,
use 45 degree or long-sweep 90 degree fittings.
9. Make suction piping short, direct, and never
smaller in diameter than suction opening of
pump. Suction piping should be equal to or larger
than pump suction port, depending on pipe
length.
10. Insure that all joints in suction piping are airtight.
11. When installing valves and other fittings, posi-
tion them to avoid formation of air pockets.
12. Permanently mounted suction filters are not rec-
ommended.
Содержание DynaPump LE Series
Страница 2: ...This page intentionally blank...
Страница 6: ...This page intentionally blank...
Страница 10: ...This page intentionally blank...
Страница 16: ...This page intentionally blank...
Страница 21: ...Figure 4 2 g Gap Figure 4 1 Bearing Wear Page 13...
Страница 23: ...APPENDIX...
Страница 27: ...A 4...
Страница 28: ...A 5...
Страница 29: ...A 6...
Страница 30: ...A 7...