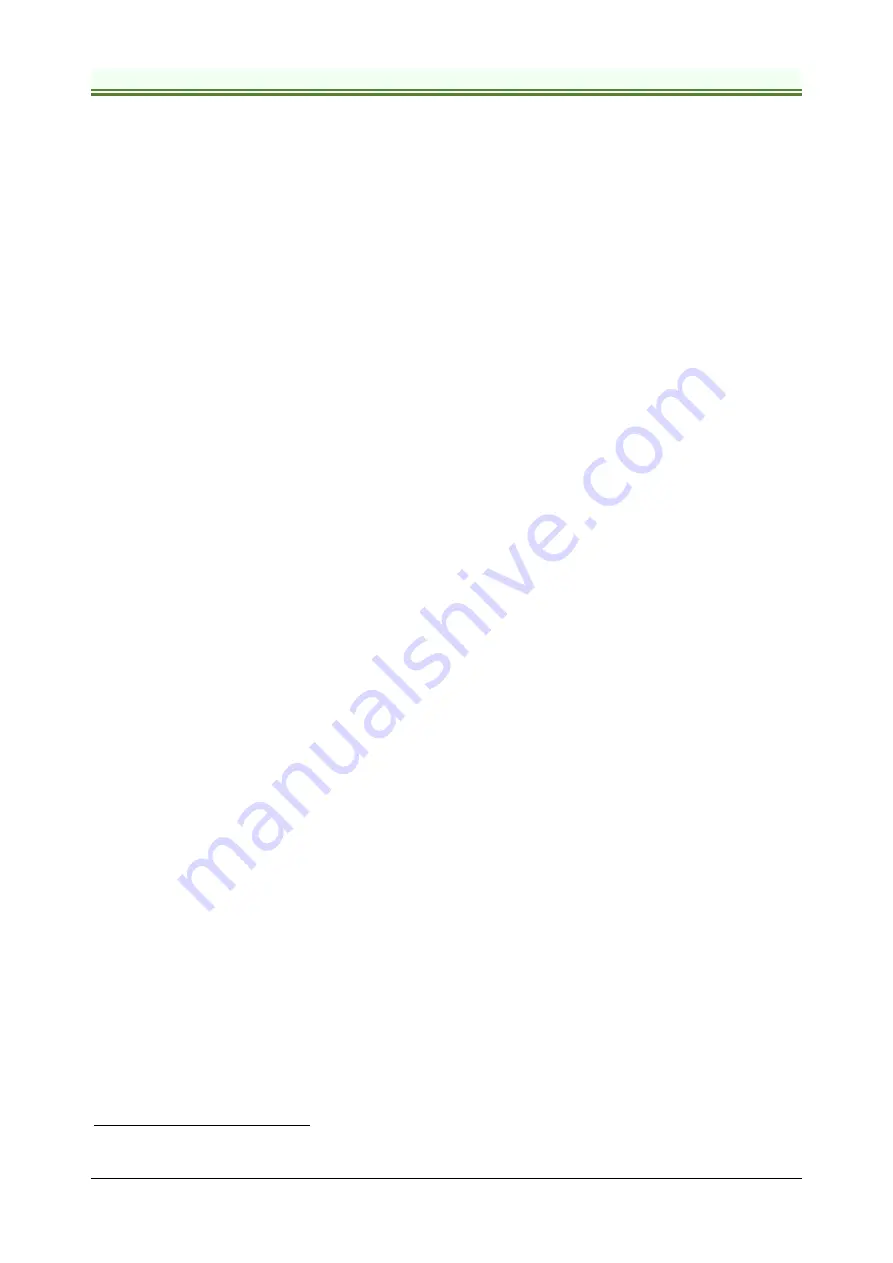
Technosoft 2017
9
iPOS4808 BX-CAT-STO Technical Reference
2.2
Product Features
•
Fully digital servo drive suitable for the control of rotary or linear brushless, DC brush, and step motors
•
Very compact design
•
Sinusoidal (FOC) or trapezoidal (Hall-based) control of brushless motors
•
Open or closed-loop control of 2 and 3-phase steppers
•
STO: 2 safe torque-off inputs, safety integrity level (SIL3/Cat3/PLe) acc. to EN61800-5-1;-2/ EN61508-3;-4/
EN ISO 13849-1. When left not connected will disable the motor outputs. This provides a dual redundant
hardware protection that cannot be overdriven by the software or other hardware components.
•
Various modes of operation, including: cyclic synchronous torque, velocity or position control(CST, CSV or
CSP); position or velocity profiles, external analogue reference or sent via a communication bus
•
Technosoft Motion Language (TML) instruction set for the definition and execution of motion sequences
•
Standalone operation with stored motion sequences
•
Communication:
•
RS-232 serial up to 115kbits/s
•
Dual 100Mbps EtherCAT® interfaces, for use in daisy-chaining topologies
•
Digital and analog I/Os:
•
6 digital inputs: 5-36 V, programmable polarity: sourcing/NPN or sinking/PNP: 2 Limit switches and 4
general-purpose
•
5 digital outputs: 5-36 V, with 0.5 A, sinking/NPN open-collector (Ready, Error and 3 general-purpose)
•
NTC/PTC analogue Motor Temperature sensor input
•
Electro-Mechanical brake support: software configurable digital output to control motor brake
•
Feedback devices (dual-loop support)
1
st
feedback devices supported:
•
Incremental encoder interface (single ended or differential
•
Analog sin/cos encoder interface (differential 1V
PP
)
•
Linear Hall sensors interface
•
Pulse & direction interface (single ended) for external (master) digital reference
2
nd
feedback devices supported:
•
Incremental encoder interface (differential only)
•
Pulse & direction interface (differential only) for external (master) digital reference
•
BiSS-C / SSI encoder interface
Separate feedback devices supported:
•
Digital Hall sensor interface (single-ended and open collector)
•
2 analogue inputs: 12 bit, 0-5V: Reference and Feedback (for Tacho) or general purpose
•
Various motion programming modes:
•
Position profiles with trapezoidal or S-curve speed shape
•
Position, Velocity, Time (PVT) 3
rd
order interpolation
•
Position, Time (PT) 1
st
order interpolation
•
Cyclic Synchronous Position (CSP)
•
Cyclic Synchronous Velocity (CSV)
•
Cyclic Synchronous Torque (CST)
•
Electronic gearing and camming
•
35 Homing modes
•
127 h/w selectable addresses
•
EtherCAT® with CAN application protocol over EtherCAT (CoE) for CAT drives
•
16K
×
16 internal SRAM memory for data acquisition
•
16K
×
16 E
2
ROM to store TML motion programs, cam tables and other user data
•
PWM switching frequency up to 100kHz
•
Motor supply: 12-50V
•
Logic supply: 9-36V.
•
STO supply: 18-40V
1
Available only on P027.314.E221
2
Available only on P027.314.E721