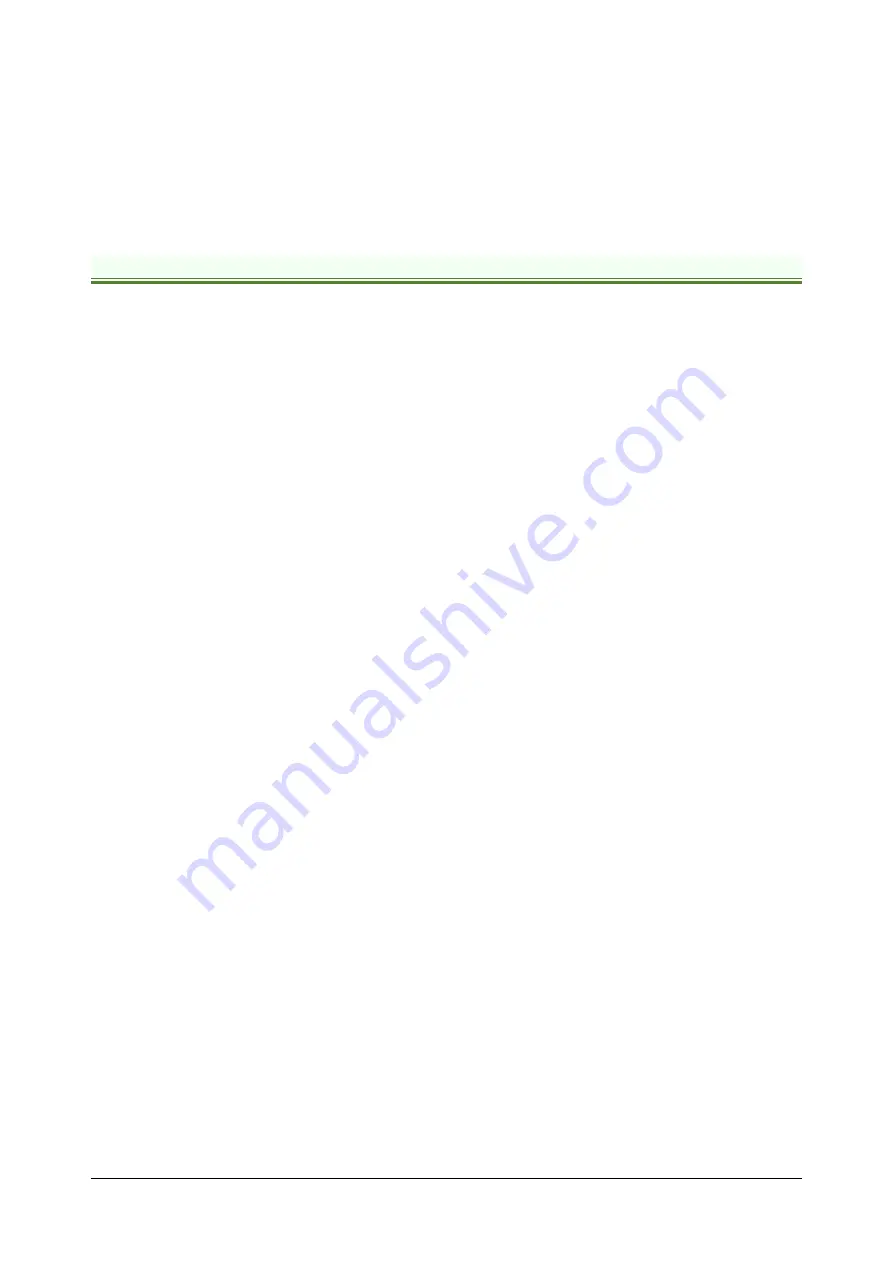
Technosoft 2018
10
iMOT Intelligent Motors Line Technical Reference
EasyMotion Studio
platform includes EasySetUp for the system setup, and a
Motion Wizard
for the motion
programming. The Motion Wizard provides a simple, graphical way of creating motion programs and automatically
generates all the TML instructions. Beside the setup and motion wizards, EasyMotion Studio contain also various tools
for on-line monitoring and troubleshooting of the iMOT performance. EasyMotion Studio is usually the choice when it
comes to the CAN versions of the iMOT that are going to be used in TMLCAN mode. However, it can also be used with
the CANopen protocol, if the user wants to call TML functions stored in the drive EEPROM or to use the camming mode.
With camming mode, EasyMotion Studio offers the possibility to quickly download and test a cam profile and also to
create a
.sw
file with the cam data. The .sw file can be afterwards stored in a master and downloaded to the drive,
wherever needed.
A demo version of EasyMotion Studio (with EasySetUp part fully functional) can be
downloaded free of charge from Technosoft web page.
2.2 Product Features
•
Fully digital intelligent servo or stepper motor with embedded motion controller, drive and single turn absolute
position sensor
•
Very compact design
•
2 control options for stepper model: closed loop stepless servo / open loop microstepping (with steploss
detection)
•
Various modes of operation, including: torque, speed or position control; position or speed profiles, Cyclic
Synchronous Position (CSP) for CANopen mode, external reference mode analogue or sent via a
communication bus
•
Technosoft Motion Language (TML) instruction set for the definition and execution of motion sequences
•
Standalone operation with stored motion sequences
•
Communication:
•
RS-232 serial up to 115kbits/s
•
CAN-bus 2.0B up to 1Mbit/s (for CAN drives)
•
EtherCAT up to 100Mbit/s (for EtherCAT motors)
•
Digital and analog I/Os:
•
4 digital inputs: 5-24V, programmable polarity: sourcing/NPN or sinking/PNP (5 digital inputs for the
iMOT23xS models)
•
2 digital outputs: 5-24V, with 0.5A capacity, sinking/NPN open-collector
•
1 analogue input: 12 bits resolution, 0 … 5Vdc range
•
Electro-Mechanical brake support: software configurable digital output to control motor brake
•
Feedback device:
•
Integrated absolute single-turn position sensor offering a resolution of 4096 counts/rev
•
Various motion programming modes:
•
Position profiles with trapezoidal or S-curve speed shape
•
Position, Velocity, Time (PVT) 3
rd
order interpolation
•
Position, Time (PT) 1
st
order interpolation
•
Cyclic Synchronous Position (CSP) for CANopen/EtherCAT mode
•
Electronic gearing and camming
•
35 Homing modes
•
16 h/w selectable addresses depending on model, otherwise 127/255 software selectable addresses
(CANopen / TMLCAN)
•
Two CAN operation modes selectable by HW pin (only for CAN motors):
•
CANopen
– conforming with
CiA 301 v4.2,
CiA
WD 305 v2.2.13
and
CiA DSP 402
v3.0
•
TMLCAN
– intelligent drive conforming with Technosoft protocol for exchanging TML commands via
CAN-bus
•
2.5K
×
16 internal SRAM memory for data acquisition
•
4K
×
16 E
2
ROM to store TML motion programs, cam tables and other user data
•
Motor supply: 12-48V
•
Logic supply: 15-36V.
•
Operating ambient temperature: 0-40
°
C (over 40
°
C with derating)
•
Protections:
•
Short-circuit between motor phases or between motor phases and ground
•
Over and under-voltage
•
Over-current and I
2
t
•
Over-temperature
•
Communication error
•
Control error