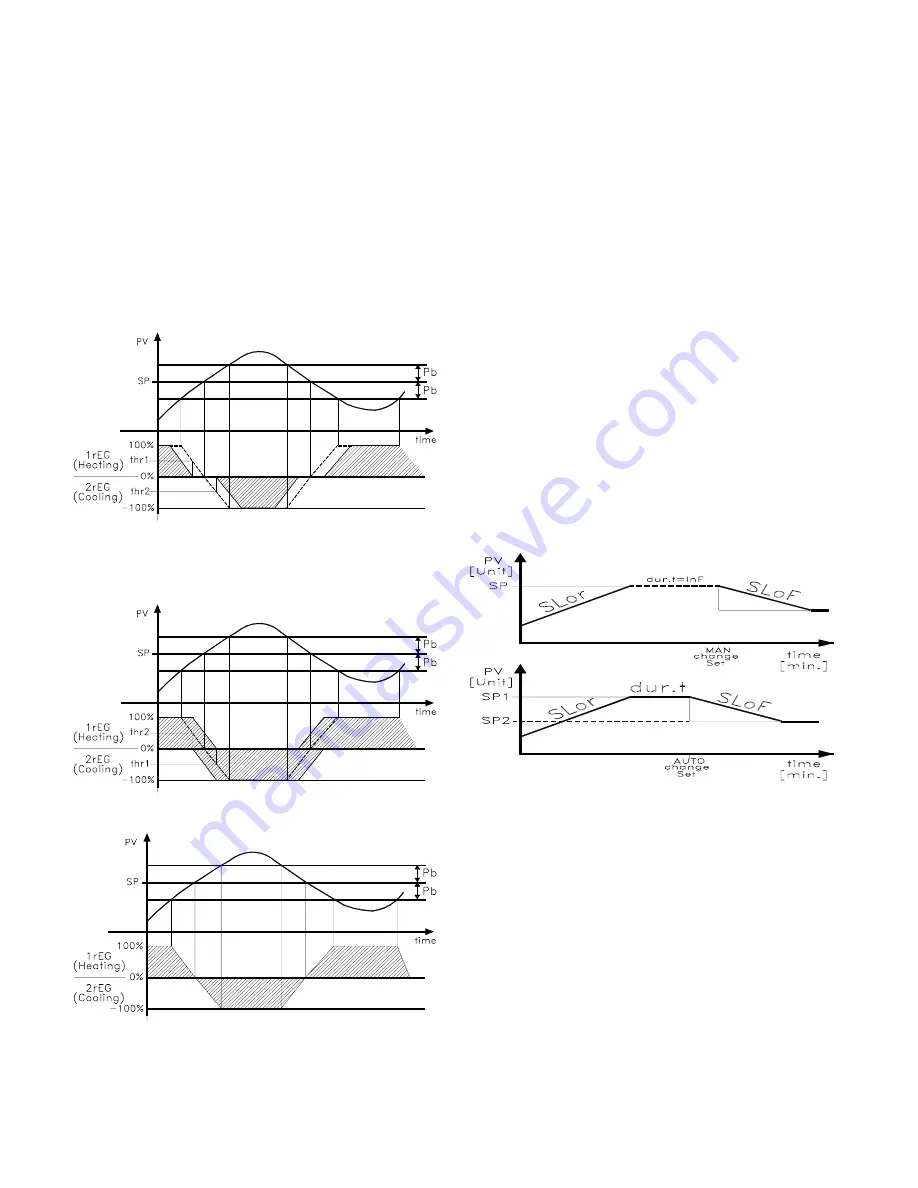
TECNOLOGIC spa - TLK 43
- OPERATING INSTRUCTIONS - Vr.02 - ISTR 06267 - PAG. 9
The use of this function is only possible if the PID control is dual
function and can be used to delay or bring forward the intervention
of the actuators commanded by the instrument.
Using this function it is therefore possible to optimise the
intervention of the two actuators in such a way that their actions do
not overlap or so that they overlap so that they obtain the mix of the
two actions of the actuators.
Basically, this means setting two power offsets (one for direct action
and one for reverse action) that set the beginning of the intervention
of the actuator commanded by the output.
The parameters that can be set for this function contained in the
block
“
]
rEG”,
are:
“thr1”
: Power threshold at which output 1rEG begins to operate.
“thr2”
: Power threshold at which output 2rEG begins to operate.
Basically, if one wishes to bring forward the reverse action (1rEG)
and delay the direct action (2rEG) it is necessary to set positive
values on parameter “thr1” and negative values on parameter “thr2”.
In this way, the area within which the two outputs are not activated
at the same time is increased.
Vice versa if one wishes to extend the reverse action (1rEG) and
bring forward the direct action (2rEG) it is necessary to set negative
values on parameter “thr1” and positive values on parameter “thr2”.
In this way, the area within which the two outputs are activated at
the same time is increased.
The split range function is deactivated by setting the respective
parameters =0.
note
: In order to simplify the explanation of the example graphs a
dual action control that is only proportional (and therefore with “dEr”
and “Int” = OFF) with “Prat” = 1.0 and “rS” = 0.0 was considered.
4.12 - REACHING OF THE SET POINT AT CONTROLLED SPEED
AND AUTOMATIC SWITCHING BETWEEN TWO SET POINTS
(RISE RAMP, FALL RAMP AND DWELL TIME)
All the parameters referring to the ramps functioning are contained
in the group
“
]
rEG”.
It is possible to reach the set point in a predetermined time (in any
case longer than the time the plant would naturally need). This could
be useful in those processes (heating or chemical treatments, etc.)
where the set point has to be reached gradually, in a predetermined
time.
Once the instrument has reached the first Set Point (SP1) it is
possible to have automatic switching to the second Set Point (SP2)
after a set time, thus obtaining a simple automatic thermic cycle.
These functions are available for all the programmable controls (PID
single and double action, ON/OFF and Neutral Zone ON/OFF).
The function is determined by the following parameters :
"SLor"
- Gradient of rise ramp (Process value < Set point)
expressed in unit/minute
"SLoF"
- Gradient of fall ramp (Process value > Set point)
expressed in unit/minute.
"dur.t"
– Dwell time of Set Point SP1 before automatic switching to
Set Point 2 SP2 (expressed in hrs. and min.).
The functions are deactivated when the relative parameters are =
InF.
When the Set Point value is changed or at switch on, the instrument
automatically determines which of the two values “SLor” or “SLoF” it
has to use.
Note:
In case of PID control, if Auto-tuning is desired whilst the
ramp function is active, this will not be carried out until the tuning
cycle has been completed.
It is therefore recommended that Auto-tuning be started avoiding
activating the ramp function and, once the tuning is finished,
deactivate Auto-tuning (“Auto” = OFF), program the desired ramps
and, if it automatic tuning is desired, enable the Self-tuning function.
Examples with starts from values lower than SP and with decreasing
of SP.
4.13 - SOFT-START FUNCTION
All the parameters referring to the Soft -Start functioning are
contained in the group
“
]
rEG”.
The Soft-Start function only works through PID control and allows
the limitation of control power when the instrument is switched on,
for a programmable period of time.
This is useful when the actuator, driven by the instrument, may be
damaged excess power supplied when the application is not yet in
the normal rating. (ex. for certain heating elements).
The function depends on the following parameters :
“St.P”
– Soft-Start power
“Sst”
– Soft-Start time (expressed in hh.mm)
The possible function modes are the following :
1)
If both parameters are programmed with values other than OFF,
when switched on the instrument gives an output power as
programmed on par. “St.P” for the time programmed on par. “SSt”.
Practically, the instrument works in manual condition and switches
to automatic control at the elapsing of time “SSt”.