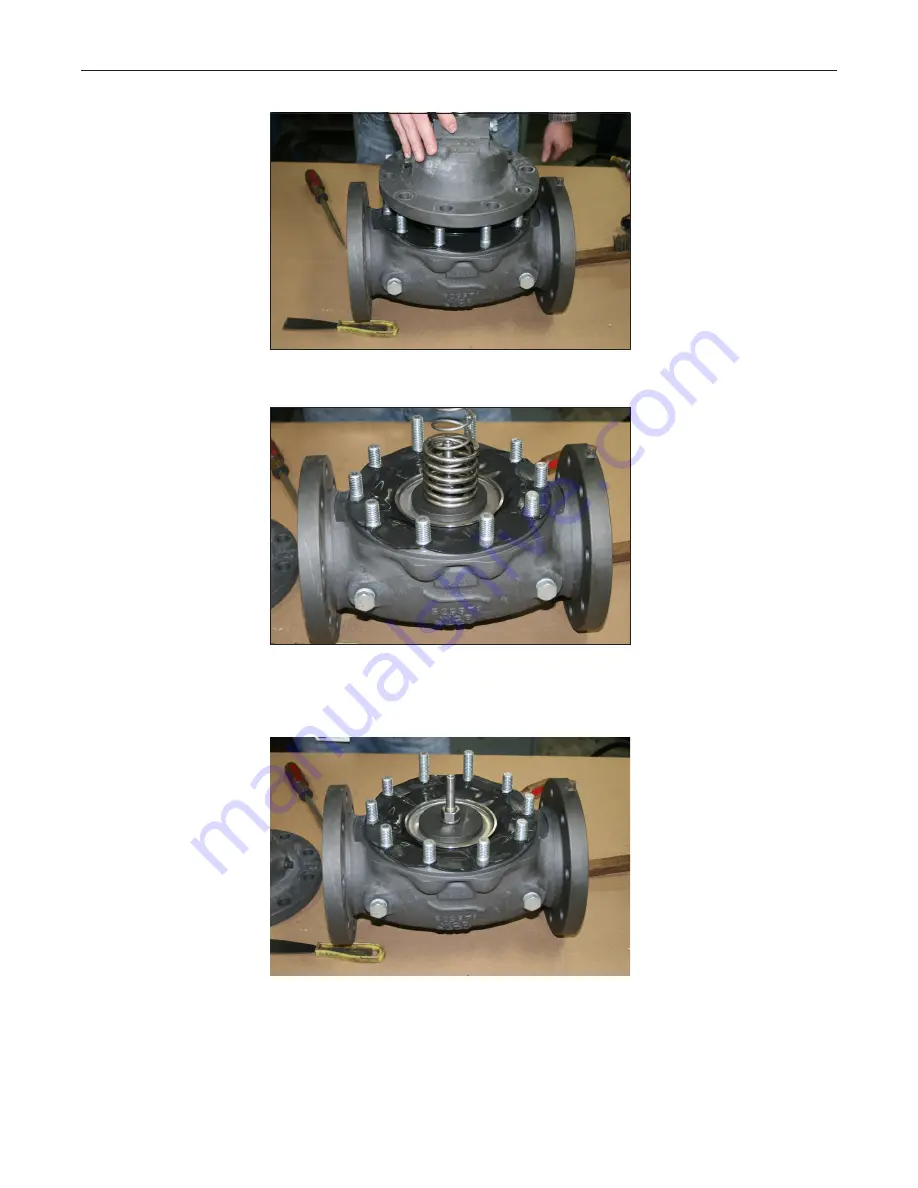
Page 12 • MN03010 ║ Issue/Rev. 0.4 (6/17)
Model 210 Valve (I / O / S) Manual
Service and Maintenance
Figure 7
– Cover Removal
Figure 8
– Cover Removal
Remove the spring(s) from the valve stem.
Figure 9
– Cover Spring Removal
Remove the stem assembly from the valve body. On the underside of the stem, note
that the stem may have a flat machined surface. This flat surface is dependent on
valve size. Some valve sizes have a nut where this flat would be (Figures 10 and 11).
Secure this flat surface or the lower stem nut in a vice as shown in Figure 12.