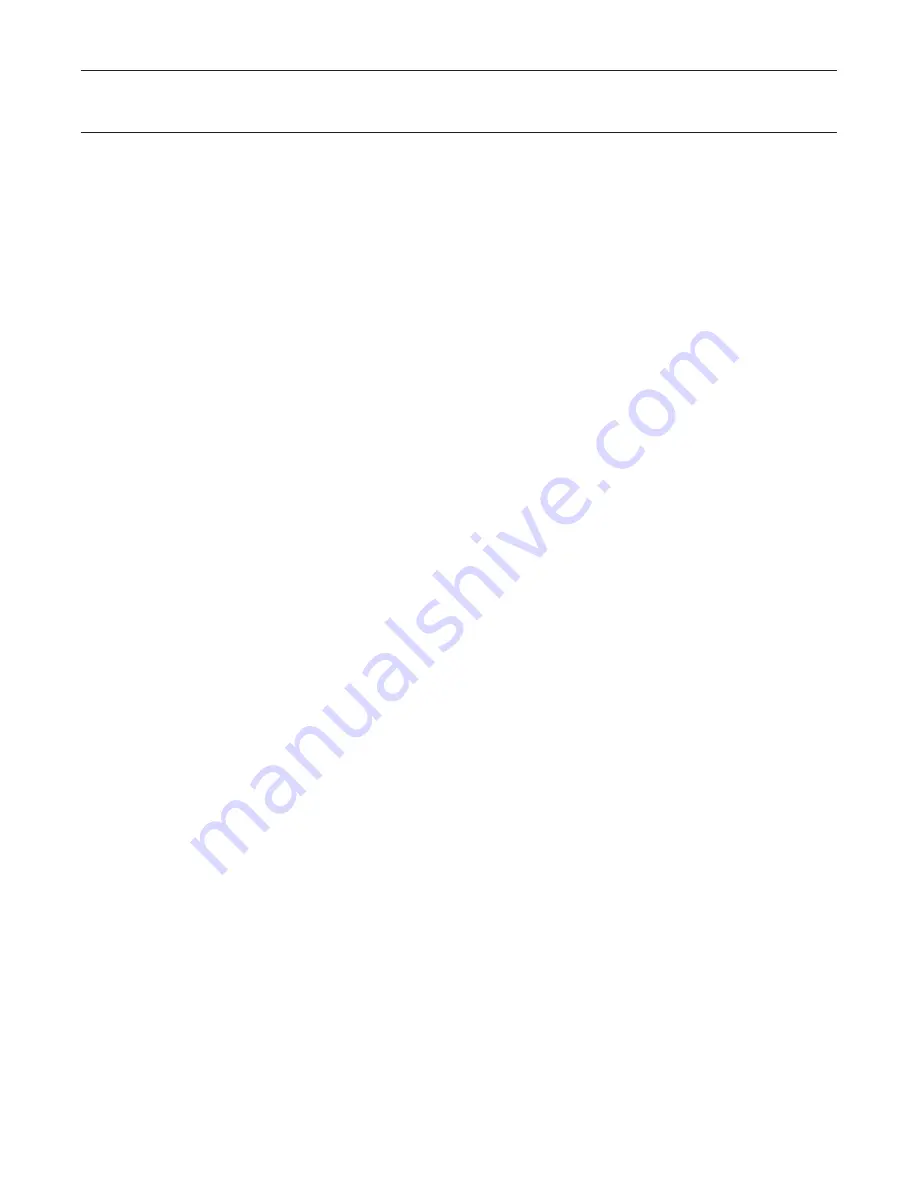
Issue/Rev. 0.4 (6/17) ║ MN03010 • Page 9
Model 210 Valve (I / O / S) Manual
Service and Maintenance
4 – Service and Maintenance
The intent of this section is to illustrate proper service and provide maintenance
interval guidelines of Smith Meter
®
210 digital control valves.
4.1
Service / Maintenance Intervals
The preset or device that is controlling the solenoids may be equipped with a means
to count the number of solenoid actuations. In the event that this is possible, the
following is a maintenance schedule for both upstream and downstream solenoid:
• At 250,000 actuations, inspect and replace components as needed
• At 500,000 actuations, rebuild the solenoids
• At 750,000 actuations, inspect and replace components as needed
• At 1,000,000 actuations, replace the solenoids
Inside the main valve, the elastomers (diaphragm, stem O-rings and poppet seal)
should be visibly inspected for cracks, breakout and deterioration every 3 to 5 years
under normal load rack conditions. This guideline can be used as a starting point
for elastomer inspection; however, it is essential for every customer to determine a
unique maintenance plan based on experience as every application and installation
will vary.
4.2
Recommended Spare Components
Reference the appropriate valve parts list for recommended spare parts.
4.3
Tools Required:
• Open ended wrenches
• Standard sockets
• Crescent wrench
• Manual torque wrench
• Pry bar
• Two flat headed screwdriver
Caution!
Prior to any service, ensure that the line has been completely drained and power
has been removed from the solenoids. Use proper protective equipment (i.e. safety
glasses, gloves, etc.) while servicing the equipment.
4.4
Document Sequence
This document will follow a sequential flow of a description of the action, followed by
a picture of the action.
4.5
210 Valve Service
It is highly recommended to service the valve while in the horizontal plane. If the
valve is in the vertical plane, this could cause misalignment of some of the compo-
nents if proper care is not taken. If the valve is removed from piping, place on a flat
surface and use wedges to ensure the valve does not roll while servicing. If the valve
is not removed from the piping, some of these steps may difficult to accomplish.
Disconnect all wiring to solenoids. Remove tubing from valve and set aside. The tub-
ing can be reused if in good condition. Remove solenoids by turning the solenoid and
fitting assembly in the counter clockwise direction – this will remove the pipe nipple
from the junction box.