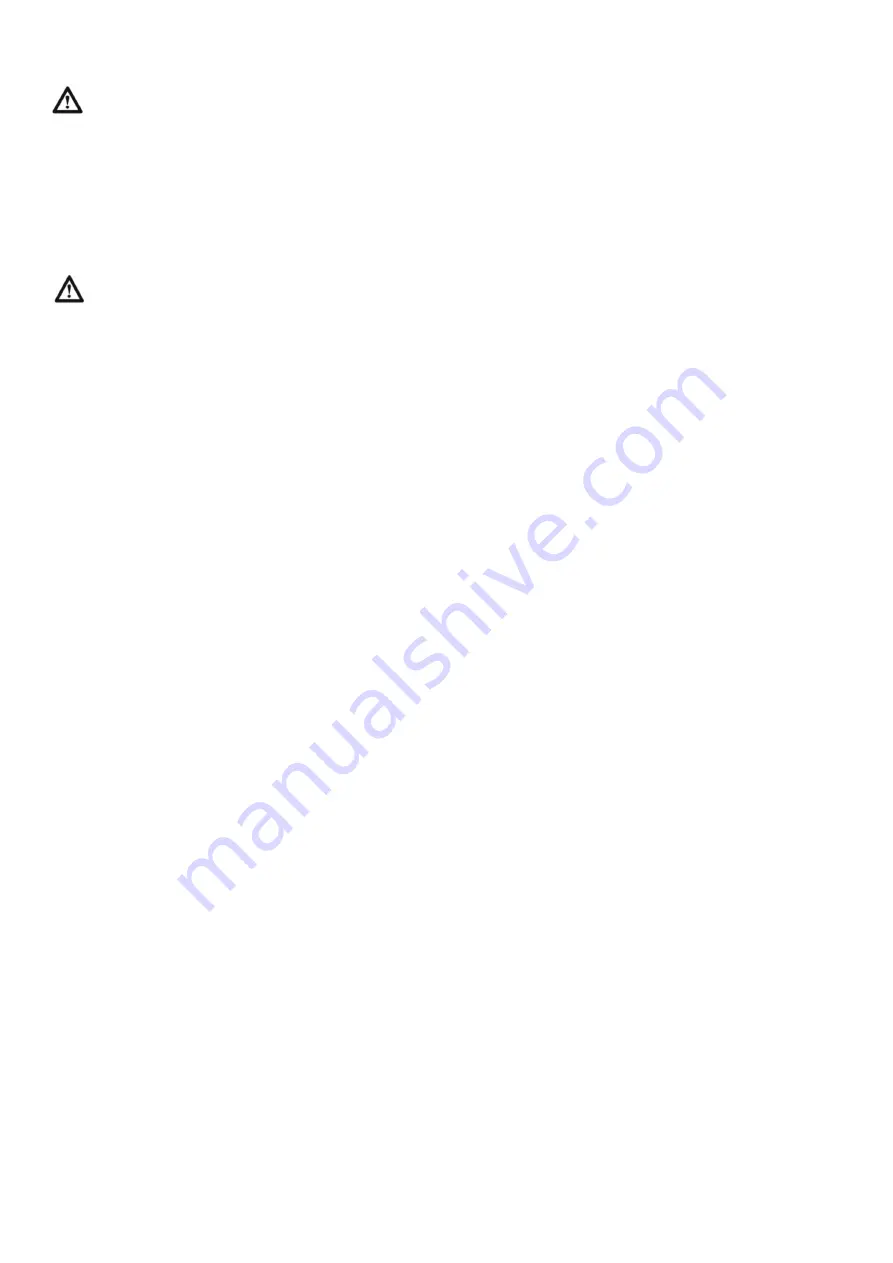
WARNING:
When
inflating
tyres
don’t
use
‘unrestricted’ airlines (without a gauge or pressure
control device) or valve connectors that require the
operator to hold them in place when inflating tyres. Tyres
can explode if they are not inflated safely. Use airline
hoses long enough to allow the operator to stay outside the
likely explosion path during inflation. Wheel cages and
similar devices can help reduce the risk of injury.
If in doubt seek help from professional service personnel.
13.17 Hub Caps
IMPORTANT:
To avoid contamination of the wheel
bearings make sure hub caps are always fitted.
Where hub caps are retained with screws they should be
checked that they are tight every 4 months.
13.18 Wheel Bearings
With use the wheel bearings will wear, the rate of wear will
depend on the working conditions. The load applied,
speed of use and the level of maintenance will all affect the
life of the bearings.
Bearing clearances in the hub should be checked
After the first month
Every 6 months or after 500 hours use.
To check the wheel bearings :
Lift the wheel off the ground.
Turn in both directions slowly to check for any rough
points or friction.
Turn it at high speed to check for unusual noises,
such as grating or knocking.
If the bearing is damaged or worn, the bearing and seals
should all be replaced.
To check the wheel bearing clearance, raise the axle until
the wheel is no longer resting on the ground (ensure that
the vehicle cannot move). Release the brake, grip the
wheel at the top and the bottom and check the clearance
by trying to tilt it. The clearance can also be detected by
using a lever between the wheel and the ground.
If you can feel any clearance, adjust the wheel bearing as
follows:
Lift the axle until the wheel is no longer resting on the
ground.
Large wheels should be removed so that the clearance is
easier to feel and to make it easier to adjust the bearings.
Remove the hubcap.
Remove the cotter pin or hair
-
pin clip from the spindle.
Tighten the castle nut to take up the internal clearance (the
conical roller bearings should then be firmly held between
the hub seating, the pressure ring, spindle and castle nut).
Slacken the castle nut until there is no longer any friction
between the castle nut and the outer bearing and the hole
for the pin is aligned with a notch in the castle nut.
Tap the hub gently using a mallet to shake down the
assembly.
Check that the hub rotates more freely.
Always err on the side of too free rather than too tight.
When the hub has been adjusted, fit a new split cotter pin
or re
-
fit the hair
-
pin clip.
Refit the hubcap.
Refit the wheel following the instructions in paragraphs
13.14 (Wheel changing) and 13.15 (Wheel nuts).
13.19 Lubrication of wheel bearings
Under normal conditions the wheel bearings should be
greased:
Annually or every 1000 working hours
When the brakes are maintained. (where fitted)
Use only lithium soap grease (recommended grease type
MR180 / 2), never mix with different grease as it will result
in a reduced life of the bearings.
All components of the axle involved in the operation (hub,
spindle, crown nut, elastic pin, cap) must be completely
degreased before reassembling the system.
The greasing of the bearings must be performed in a clean
environment
using
suitable
equipment
to
avoid
contamination that can lead to premature wear of the
bearings, of the seals and the turned shaft.
During disassembly of the drums for greasing, check also
the state of the brake shoes and of the return springs.
To dismantle the wheel bearings:
1. Working on a hard level surface make sure the vehicle
on which you are working is prevented from moving.
2. Slacken the wheel nuts and lift the axle until the wheel
clears the ground.
3. Remove the wheel.
4. Release the brakes (making sure the machine cannot
move).
5. Remove the hub cap.
6. Remove the elastic pin from the castle nut and remove
the castle nut.
7. Remove the drum/hub assembly using a hub puller if
necessary. The outer ring, the grease retaining plates
inside the hub (depending on the model), the small bearing
cone and cage come out with the hub. Check these parts.
The bearing cups and grease retaining plates can be left
inside the hub for cleaning
8 Remove the large bearing cage and cone from the
spindle using a bearing puller if necessary.
9. Check the oil seal between the spindle and the large
bearing (or the wheel bearing seal depending on the
model), and replace these parts if necessary. A puller may
be required to remove the wheel bearing seal. Note the
orientation of the oil seal for reassembly.
10. Check the contact surfaces on the spindle for the
bearing and seal and the threaded end of the spindle and
remove any bumps or asperities.
11. Check the hub surfaces in the same way.
12. Check the bearing face of the castle nut.
Clean and degrease all parts with a suitable cleaning fluid.
26
Содержание Tomahawk 7100
Страница 1: ...30417 10100 11 19 30970 10345 31725 11338 10056 3694 TMKBXOP1119A...
Страница 38: ...NOTES 35...
Страница 39: ...36 NOTES...
Страница 40: ......