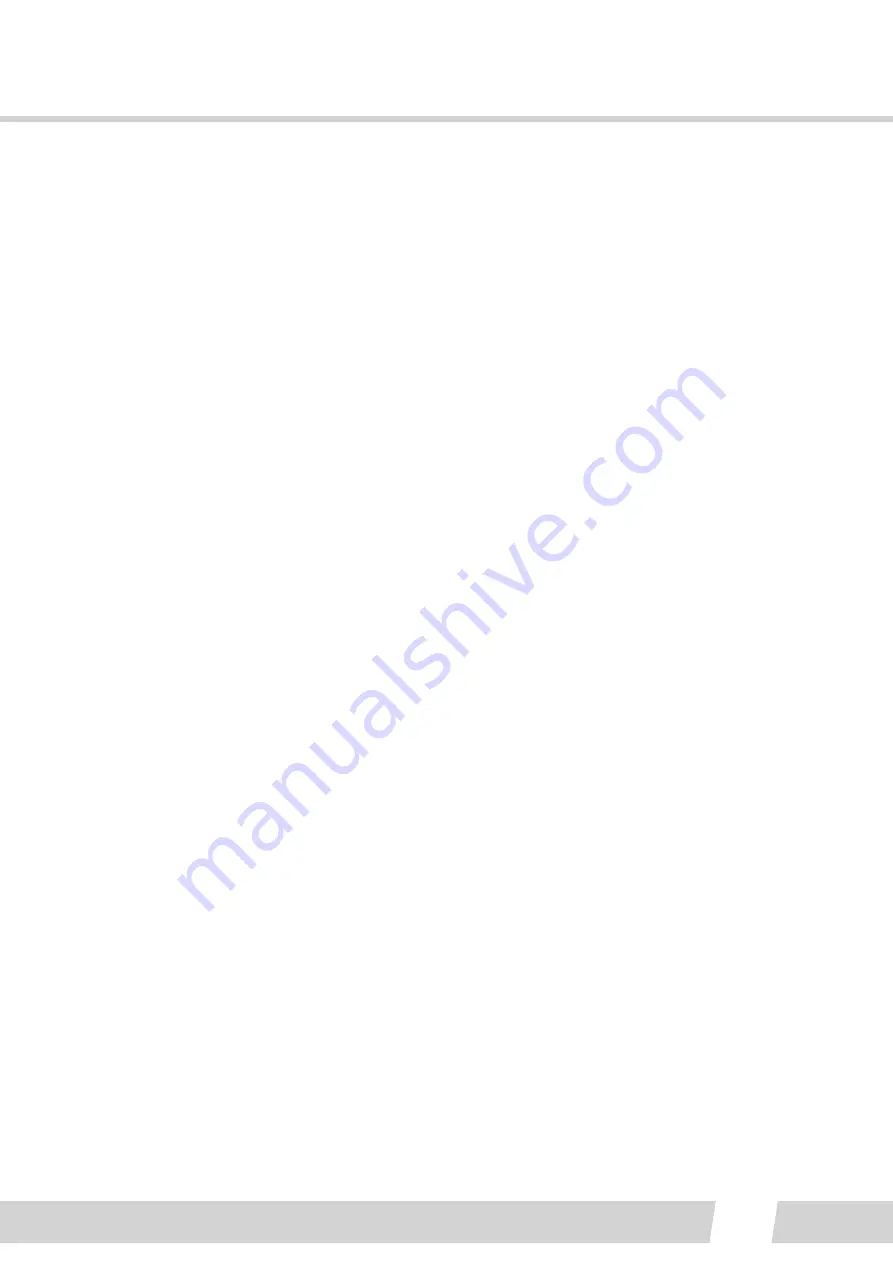
FLANGING MACHINE
11
F-400
on the conditions of use, EN1092-1 standard or standard derived from this can be used
in dimensioning. The main factor, which defines the maximum diameter of the flange, is
deforming capability of material. In practice this capability is expressed as elongation.
This means that the proportion d4/OD should be smaller that the elongation value
of material to be flanged. However, the experimental results show that much higher
elongation values can be achieved thanks to the multidimensional straining scheme.
In hot forming the sealing surface can be changed in quality from smooth to rough by
selecting the appropriate profile for the forming cone.
Flange O.D. ( d4 ) :42.4 < O.D. < 50 d4: EN1092-1
50 < O.D. < 406.4 d4: EN1092-1
3.2 METHODS OF FLANGING
3.2.1 COLD FLANGING
This is definitely the most efficient method due to its simplicity. However, in most cases,
annealing is required for stress relief after forming because, for example, with small pipe
dimensions the relative elongation may be up to 75 %. This is considerably greater than
obtained in tension tests, and results in hard and brittle structure.
Wall thicknesses: 2...5 mm for mild steel, stainless steel and copper alloys, up to 406 mm
(16”) pipes. See chapter 6.3. Cold flanging and flaring of the pipe.