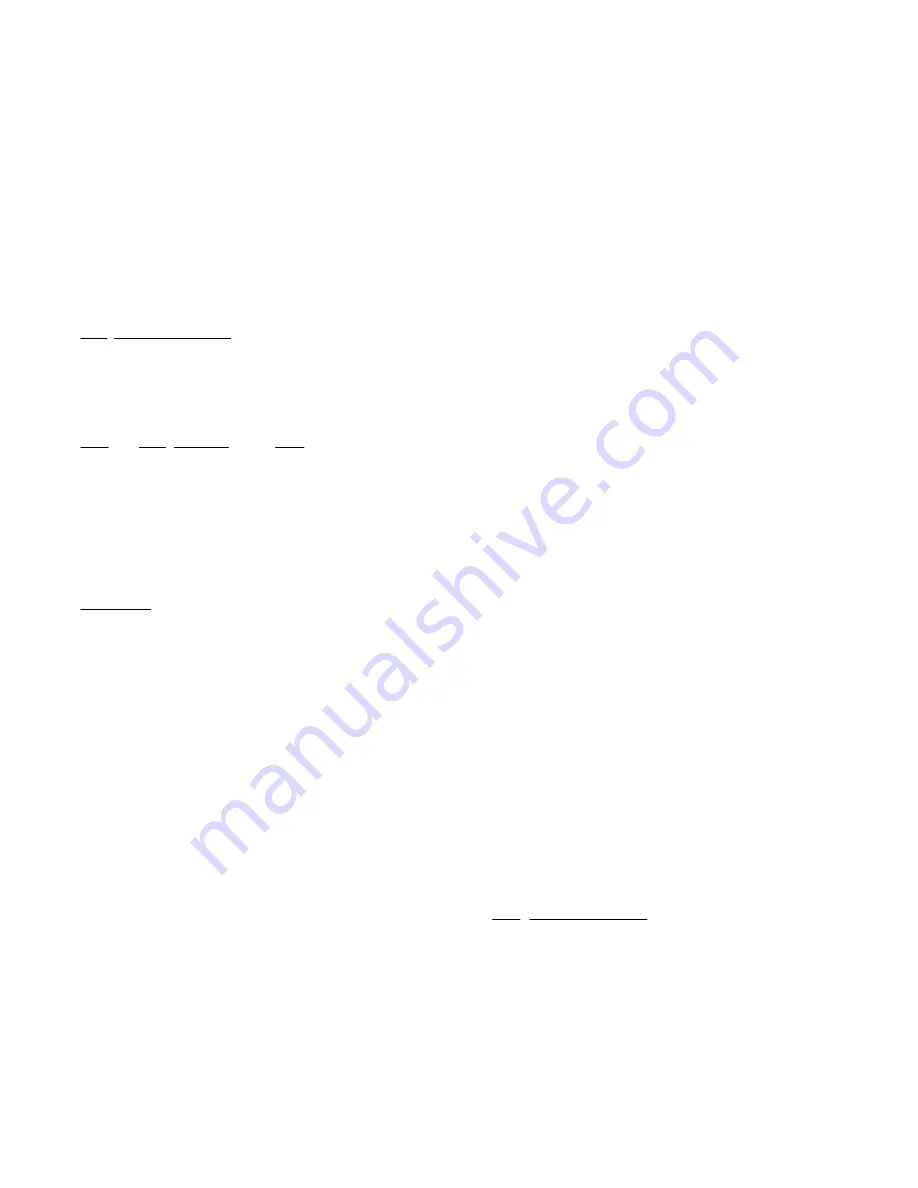
10
NOTE: The bar denotes low logic, active state
Wire Size:
28 AWG minimum
Run Length: 50 feet (15 meters) max.; 15 feet (4.6 meters) max.
for HI SPEED POT 1 and HI SPEED POT 2.
Shielded cable must be used for highest noise immunity. Be sure to
ground the shield only at one end of the cable.
3.6.2 Potentiometers (see Figure 9.0 for potentiometer locations)
R1 Deceleration
R3 High Speed
R2 Acceleration
R4 Base Speed
3.6.3 I/O Characteristics
RUN, BASE SPEED ONLY (Input Characteristics)
High Voltage Level
+5.5 VDC to +15 VDC
High Level Current
600 microamperes max.
Low Level Voltage
0 VDC to +4.5 VDC
Low Level Current
1.8 milliamperes max.
AWO, CW/CCW, PULSE IN, HALF/FULL (Input Characteristics)
High Level Input Sinking
Current
less than 1 milliampere
Low Level Input Sinking
Current
10 to 20 milliamperes
NOTE: These inputs are tied to Signal Common (7, 12) for a low
level input and open collectored for the high input level.
PULSE OUT Output Characteristics
High Level Output
Characteristics
+24 VDC
Low Level Output Voltage
+0.7 VDC max. at 40 milliam-
peres max.
3.7 ENVIRONMENTAL REQUIREMENTS
Storage Temp:
-40°F to +185°F (-40°C to +85°C)
Operating Temp:
Drive Module:
+32°F to +167°F (0°C to +75°C) on case
Oscillator:
+32°F to +122°F (0°C to +50°C) free air
ambient
Humidity:
95% max., noncondensing
Altitude:
10,000 feet (3048 meters) max.
Thermal
Requirements:
Maintain drive module case temperature
below 167°F (75°C)
NOTE: The drive module will operate within its temperature limit
if heat sink fins are vertical and free air ambient is within the
specified limits.
SECTION 4: FUNCTIONAL DESCRIPTION
4.1 OVERVIEW
The 230-TOH and 430-TOH are motor drive/translator/pulse gen-
erator modules that allow for the operation of all basic motor func-
tions.
External power to the unit is required.
The functions that the module performs are:
•
Adjustable acceleration and deceleration
•
Adjustable base speed
•
Clockwise/counterclockwise direction control
•
Full-step/half-step control
•
Run-stop control
•
Remote mechanical speed adjustment
4.2 Operational description
The 230-TOH and 430-TOH modules can be functionally divided into
four components:
1. Motor drive circuitry
2. Translator circuitry
3. Oscillator/pulse generator circuits
4. Logic control functions
To drive the motor, a technique called “chopping” is used. Com-
pared to older drive techniques, chopping gives improved motor per-
formance while allowing the drive circuitry to dissipate less power.
The voltage applied to the motor windings is turned on and off very
rapidly, or
chopped
, so that the desired current is produced.
The translator circuitry accepts a single pulse as an input and de-
termines which windings (phases) of the motor must be turned on
and off in order to advance the motor shaft one step, in the full-step
mode. The translator circuit is fully self-contained and is not acces-
sible through any of the function pins.
The pulse input to the translator is internally generated by the
oscillator.
This is accomplished by setting switch S1, position 4
to the “on” (closed) state, unless an external pulse source is
utilized.
The oscillator circuitry controls the frequency of the pulse
train for acceleration, deceleration, high and base speeds in accor-
dance with the settings of potentiometers R1 thru R4.
The logic control circuitry accepts high or low logic levels through
the pins on connector J1 and adjusts the motor operational param-
eters as described in Section 5.
The 230-TOH and 430-TOH enable the user to remotely control
the high speed rate by connecting a 500 k ohm potentiometer be-
tween pins 8 & 15 on connector J1.
If no external potentiometer is
required, set position 3 of switch S1 to the “on” (closed) state.
SECTION 5: PIN CONNECTIONS
(Reference Figure 2.2)
Connector J1, 15-pin “D” type connector, female
5.1 AWO (ALL WINDINGS OFF) - Pin 1
When connected to SIGNAL COMMON (closed), i.e., when acti-
vated, turns off all power to the motor windings. The motor shaft can
now be turned by hand. No motion can occur if this signal is active.
When this pin is left open, all windings are on.
WARNING:
Holding torque is eliminated when this signal is active. Ensure
that the motor load, when released by this command, will not
injure property or personnel.
Artisan Technology Group - Quality Instrumentation ... Guaranteed | (888) 88-SOURCE | www.artisantg.com