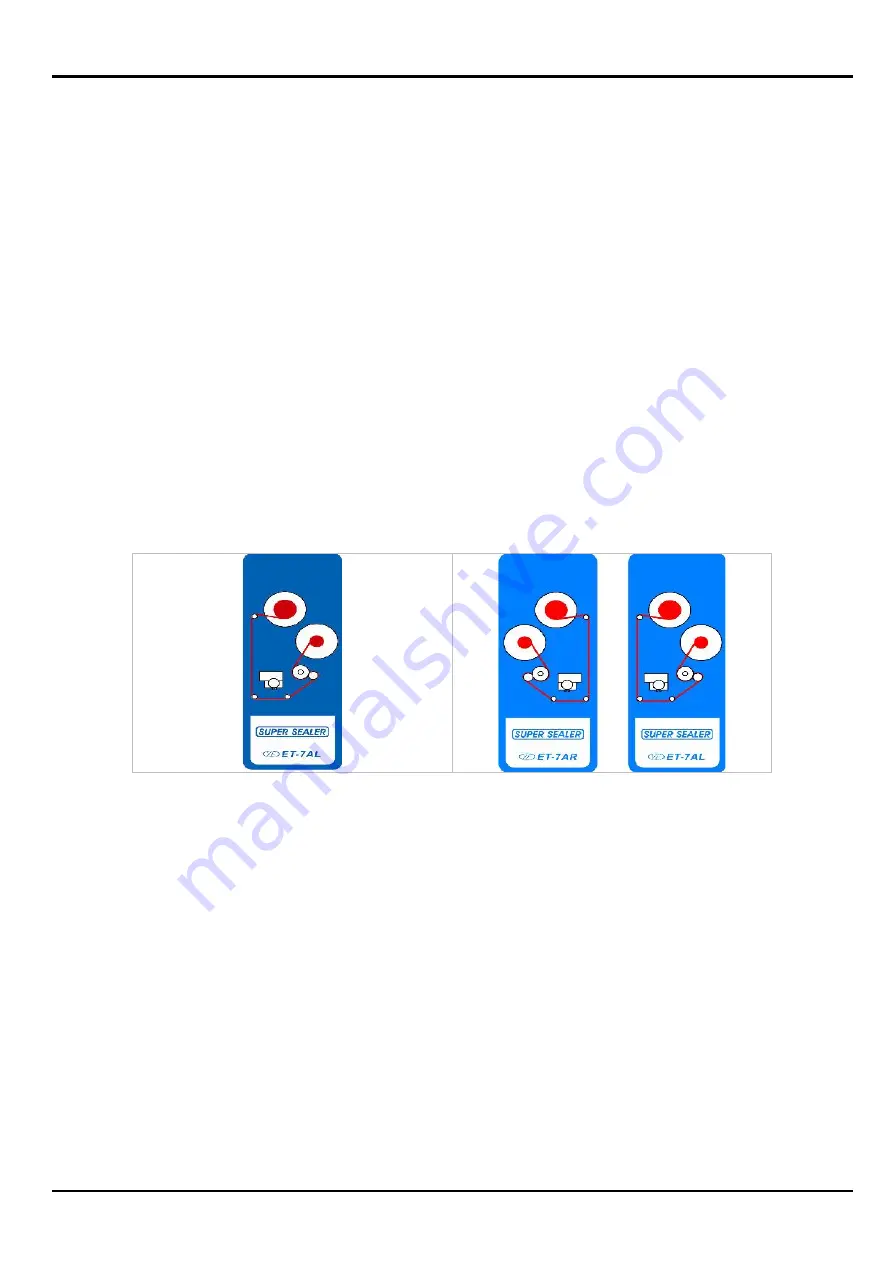
Updated: 15 November, 2011 Page 10
REF: REI-85-0045
6.
DATE PRINTER
Specification
Type
Manual Hot Ink Stamp
Maximum Number of Lines
Maximum 3 (Required before making)
Font / Font Size
Times Roman 10 font
Ribbon / Ribbon Color
100 meters/ Black (standard) or White
Maximum Number of Alphanumeric per line
9 (e.g. 20060918, EXP060918)
Temperature Setting (adjustable)
50- 180 C (Default 120)
Printer Position
The position can be adjusted manually
The information (e.g. date/time) is manually loaded on the date printer “alphanumeric holder”. Simply
slide in the information on a “MIRROR” direction.
WARNING! The printer uses HIGH temperature to function. Please ensure that you allow the printer to
COOL DOWN for at least 90 minutes before changing the information.
6.1 PRINTER RIBBON SETTING
(With 1 Date Coder)
(With 2 Date Coders)
7.
MOULD REMOVAL & REPLACEMENT
ELECTRICAL HAZARD
Always REMOVE the machine from the power outlet before performing any maintenance or cleaning
works.
BURN HAZARD
• Cleaning and maintenance should be performed by your trained personnel only
• Allow unit to cool at least 90 minutes before normal cleaning
• If hot machine must be opened, keep hands away from upper moulds and the printer