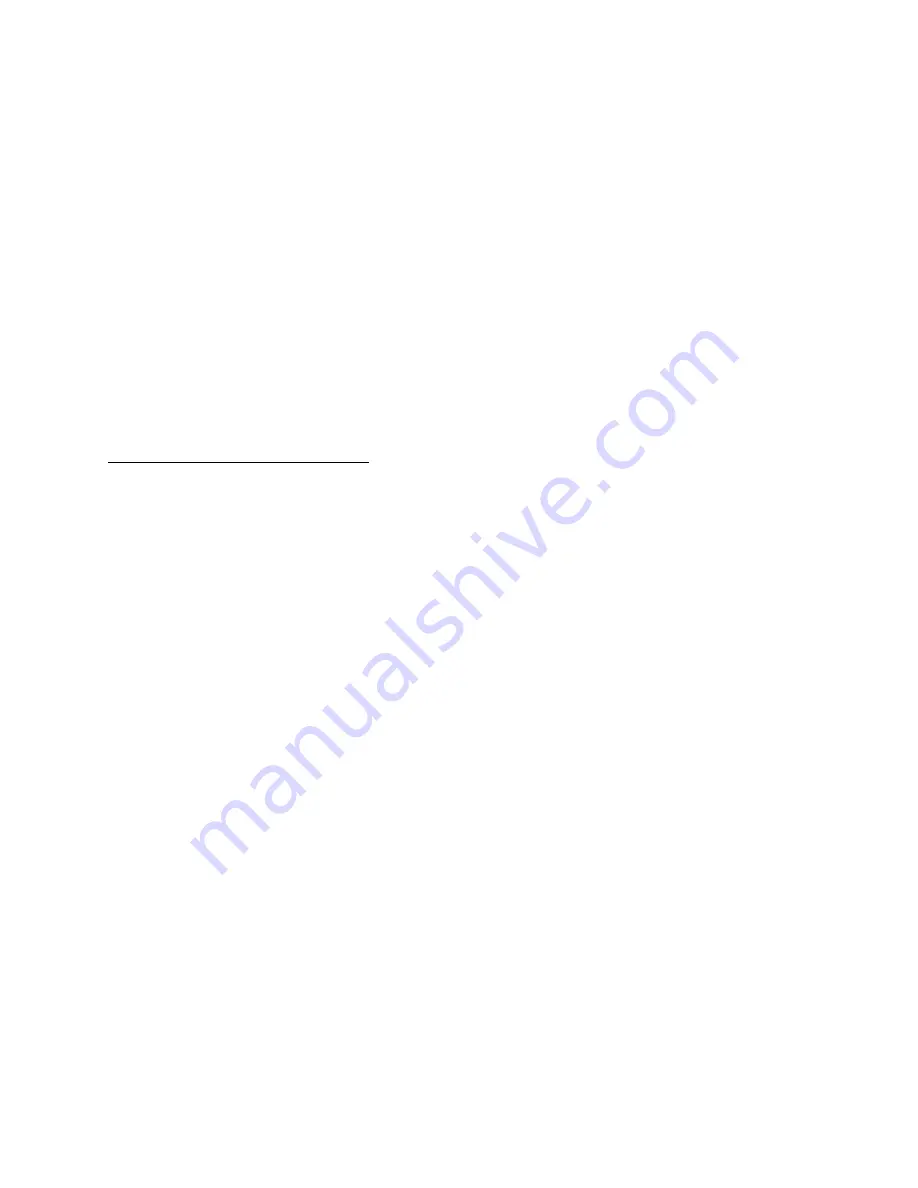
13
400 hours of operation or more often after wear begins. It is easily done when the rotor is removed as one
end is usually greatest so that it is not necessary to remove other end unless pinholes show wear. Inspect
and replace worn pins and boot seals whenever rotor and/or connecting rod is inspected. Also, inspect the
holes in both the rotor and drive shaft hub for wear. There are two sets of holes in each, so that an
alternate pair of holes can be used when wear is excessive on one set of holes. When both sets of holes
are worn, the drive shaft hub should be replaced.
Connected to the suction housing is the drive assembly that houses the packing chamber and chrome
sleeve, drift shaft and bearings. The bearings should be greased every 40 hours of operation only. The
packing chamber should be greased twice daily and always at the completion of the day.
Dismantling and Installing Pump Drive
Remove hydraulic motor from drive assembly adaptor or gear box from shaft depending on hydrostatic or
mechanical drive. Remove square head from drive collar. Loosen boot clamps, and slip off end boot.
Roll boot drive from collar. Remove four ½-inch bolts holding bearing housing to suction hopper.
Remove bottom half of frame cradle. Loosen set screws and fastening bolts on top half of frame cradle.
Entire unit will now lift clear of the suction hopper. There is approximately 1/16
th
-inch clearance all
around between the drive collar and the center hole into the suction hopper and plate. Set-up concrete
may block passage of drive collar through the housing. To install new unit, reverse the above procedures,
following the steps below. It is important to set frame cradle to bearing housing last in order, not to place
strain on it. Pack drive collar and Esso Nebula EP2 or equivalent grease. On the bearing housing is a
raised boss which fits into a counter bore in the suction hopper bolting face. Examine both of these
sections for burrs. Remove with flat mill file. Make sure all foreign matter is removed from all mating
surfaces. Wipe with grease after cleaning. Pull the four housing bolts up alternately, so that housing
faces contact all around. After drive unit is secured in place, tighten frame cradle set screws until cradle
is firm against bearing housing. Tighten lock nuts and mounting bolts. Complete balance of assembly in
reverse order of dismantling.