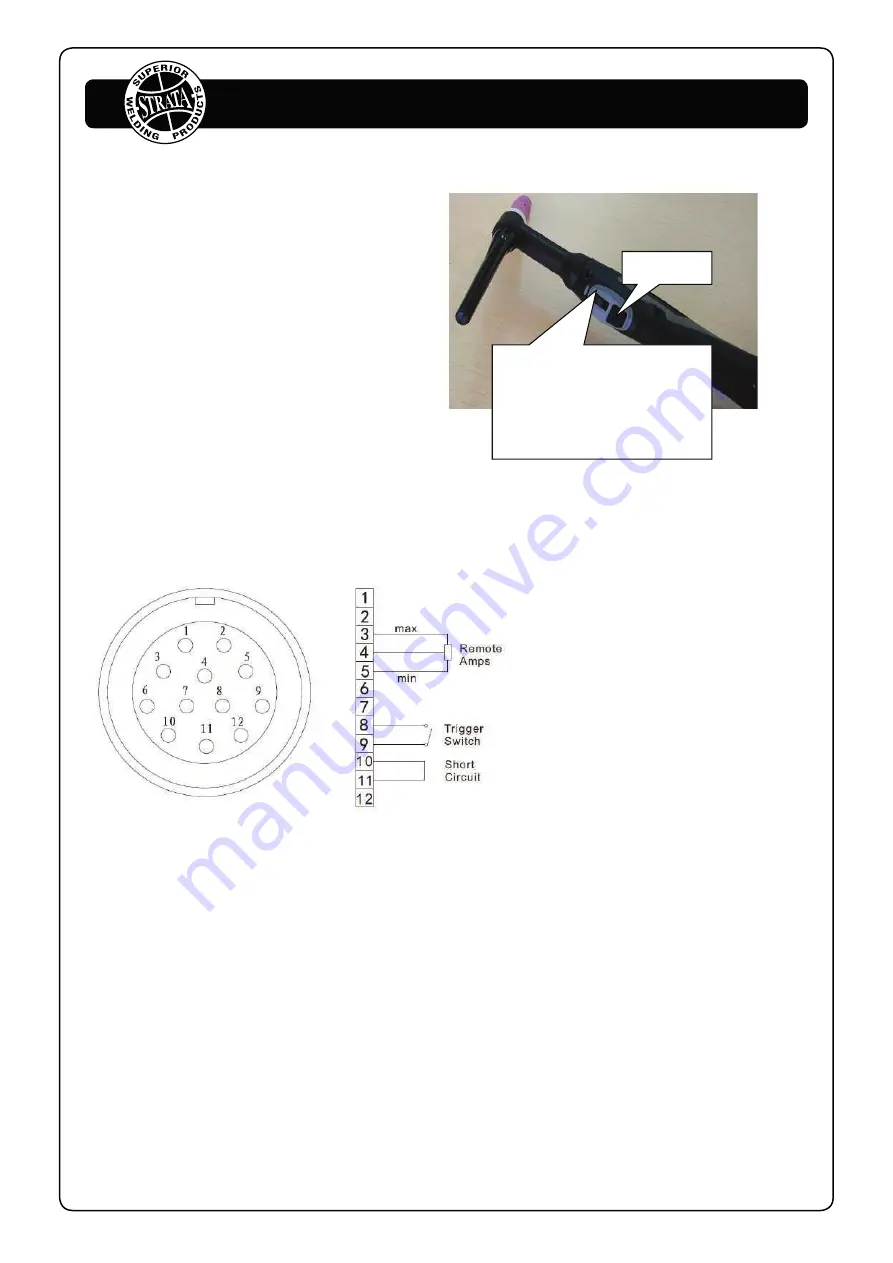
4.5 Remote current control
TIG series of welding machines can accept
remote current control from a potentiometer/
analogue signal or a digital up/down button
signal. Potentiometer remote control will
change the current from the 10A minimum to
the maximum set using the machine current
control . This is very useful for precision work.
12 Pin Remote Plug Connection
Gun switch
Adjust current roller wheel,
when it’s roll upwards, the
current decrease, when it’s roll
downwards, the current increase.
Potentiometer
Potentiometer
42
www.strata.co.nz
ADVANCEMULTI205P
Содержание ADVANCEMULTI205P
Страница 56: ...56 www strata co nz ADVANCEMULTI205P...
Страница 69: ...69 www strata co nz ADVANCEMULTI205P...