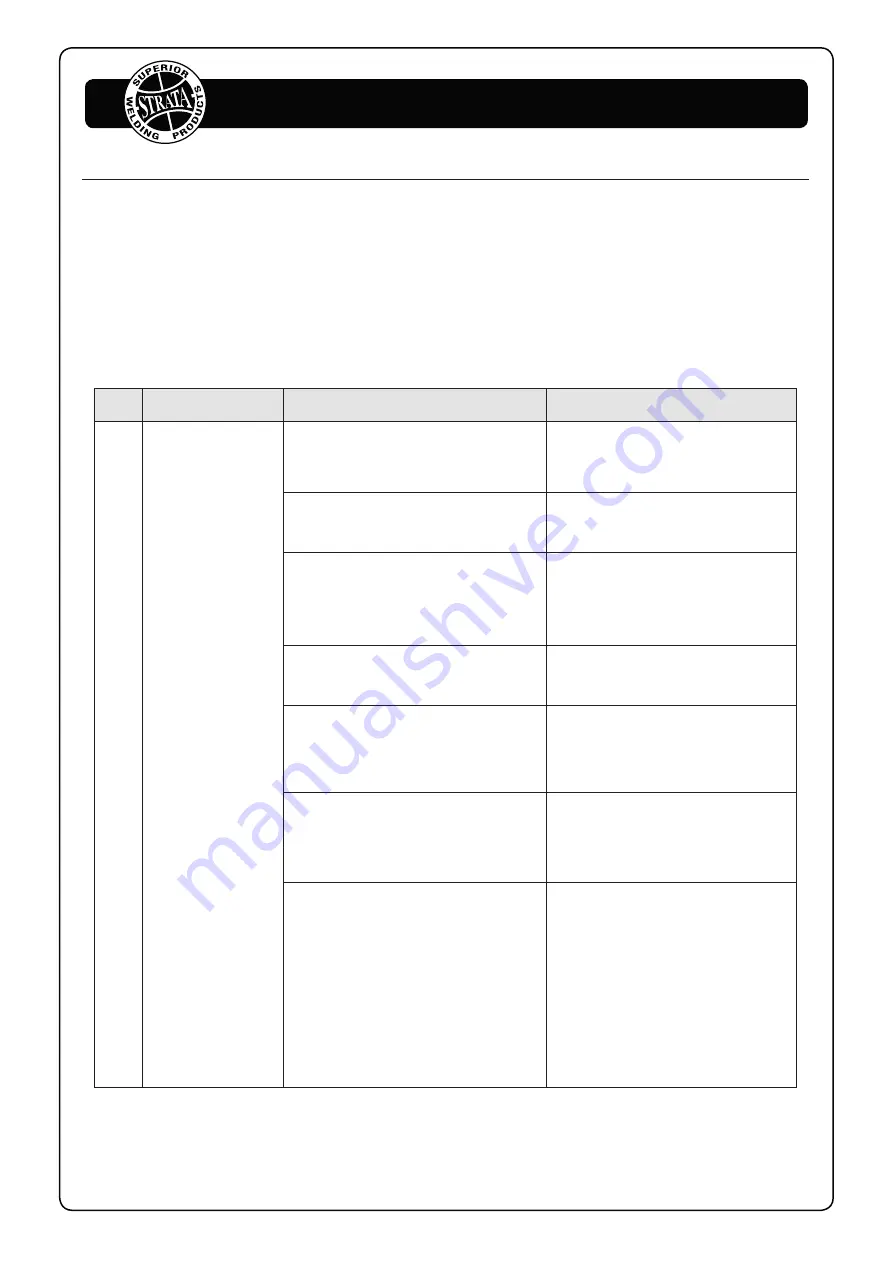
MAINTENANCE AND TROUBLESHOOTING
4 Welding trouble shooting
4.1 MIG welding trouble shooting
The following chart addresses some of the common problems of MIG welding. In all cases of
equipment malfunction, the manufacturer’s recommendations should be strictly adhered to and
followed.
NO.
Problem
Possible Reason
Suggested Remedy
1
Excessive
Spatter
Wire feed speed set too high
Select lower wire feed speed
Voltage too high
Select a lower voltage setting
Wrong polarity set
select the correct polarity for the
wire being used - see machine
setup guide
Stick out too long
Bring the torch closer to the work
Contaminated base metal
Remove materials like paint,
grease, oil, and dirt, including
mill scale from base metal
Contaminated mig wire
Use clean dry rust free wire. Do
not lubricate the wire with oil,
grease etc
Inadequate gas flow or too much
gas flow
Check the gas is connected, check
hoses, gas valve and torch are not
restricted. Set the gas flow
between 6-12 l/min flow rate.
Check hoses and fittings for
holes, leaks Protect the welding
zone from wind and drafts
58
www.strata.co.nz
ADVANCEMIG 255C